Technical Guide to Optimizing Print Settings on a UV Flatbed Printer
UV flatbed printers have revolutionized the printing industry by offering versatility, high resolution, and durability in print outputs. Whether you’re printing on rigid materials like glass, metal, or ceramics, or on flexible media such as vinyl or fabric, UV flatbed printers can deliver stunning results. However, achieving optimal print quality requires a keen understanding of the printer’s settings and how to fine-tune them for different applications. This technical guide aims to provide comprehensive insights into optimizing print settings on a UV flatbed printer to ensure the best possible outcomes.
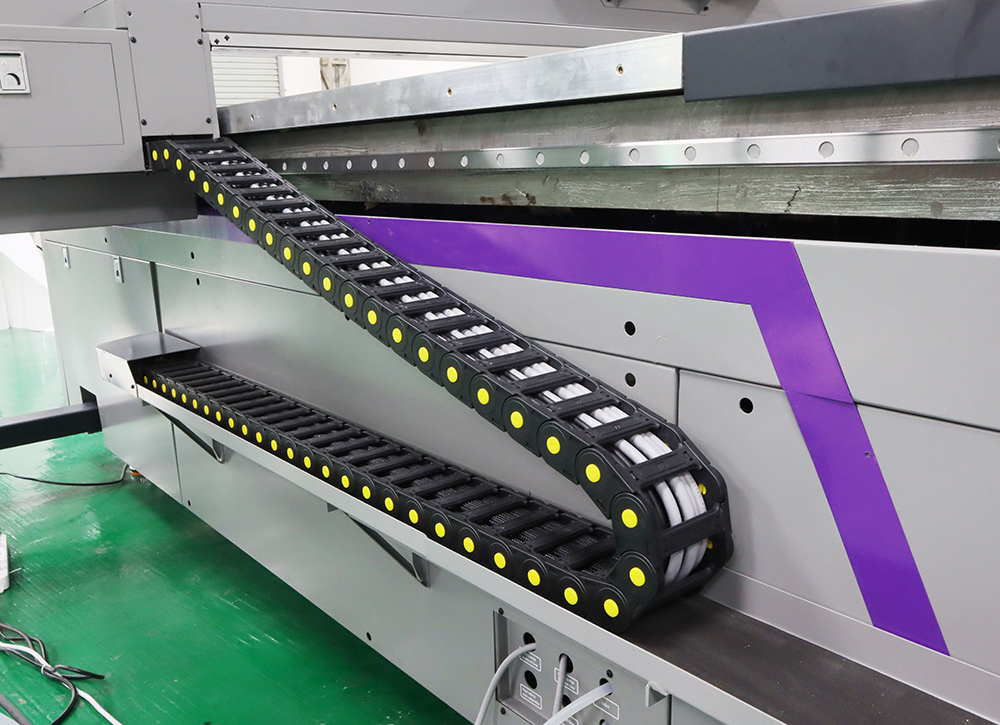
Understanding the Basics of UV Flatbed Printing
UV flatbed printers utilize ultraviolet (UV) light to cure inks instantly upon contact with the material. This process ensures fast drying times, enhanced durability, and the ability to print on a wide range of substrates without the need for pre-treatment or coating. The printer’s UV lamps emit high-energy light that triggers a chemical reaction in the ink, causing it to solidify and adhere permanently to the surface.
Key Factors Affecting Print Quality
Several factors influence the quality of prints produced by a UV flatbed printer. These include:
Ink Type and Quality: Different inks are formulated for specific applications and materials. Choosing the right ink is crucial for achieving desired color accuracy, adhesion, and durability.
Print Resolution: Measured in dots per inch (DPI), print resolution determines the sharpness and detail of the output. Higher DPI values generally result in better image quality.
Print Speed: Faster print speeds can compromise quality due to reduced ink coverage and curing time. Finding the right balance between speed and quality is essential.
Curing Settings: The intensity and duration of UV exposure significantly affect ink curing. Inadequate curing can lead to poor adhesion and smudging, while overcuring may cause material distortion or ink cracking.
Substrate Properties: The type, texture, and porosity of the material being printed on can impact ink absorption and adhesion.
Printer Calibration: Regular calibration ensures that the printer’s heads, beds, and UV lamps are aligned correctly, maintaining consistent print quality.
Optimizing Print Settings
To optimize print settings on a UV flatbed printer, consider the following steps:
1. Select the Right Ink
Material Compatibility: Choose inks that are compatible with the substrate you’re printing on. For example, flexible inks work best on vinyl and fabric, while rigid inks are suited for glass and metal.
Color Accuracy: Use high-quality inks with a broad color gamut to achieve accurate and vibrant colors.
Durability: Opt for inks with good resistance to fading, scratching, and chemicals, especially if the prints will be exposed to harsh environments.
2. Set the Appropriate Print Resolution
General Graphics: For standard graphics and text, a resolution of 300 DPI is usually sufficient.
High-Detail Images: For photographs or intricate designs, increase the resolution to 600 DPI or higher for optimal clarity and detail.
Large Format Prints: When printing large-scale graphics, lower resolutions (e.g., 150-200 DPI) may be acceptable to reduce file size and printing time without significantly compromising quality.
3. Adjust Print Speed
Quality vs. Speed: Find the optimal balance between print speed and quality. Slower speeds allow for better ink coverage and curing, resulting in higher quality prints.
Test Prints: Perform test prints at different speeds to assess the impact on quality and adjust accordingly.
4. Configure Curing Settings
UV Intensity: Adjust the UV lamp intensity based on the ink type and substrate. Higher intensities may be needed for thicker or more absorbent materials.
Curing Time: Ensure adequate curing time to prevent smudging and ensure proper ink adhesion. Overcuring can damage the material or cause ink to crack, so monitor and adjust as necessary.
Curing Distance: Maintain the correct distance between the UV lamp and the print surface to ensure even curing.
5. Prepare the Substrate
Cleaning: Ensure the substrate is clean and free of dust, oil, and moisture, which can affect ink adhesion.
Priming (if necessary): Some materials may require a primer to improve ink adhesion and durability.
Flatness: Ensure the substrate is flat and secure on the print bed to prevent misregistration and ink bleeding.
6. Calibrate the Printer
Head Alignment: Regularly check and adjust the print heads to ensure they are aligned correctly for accurate printing.
Bed Leveling: Ensure the print bed is level to avoid uneven ink deposition and curing.
UV Lamp Alignment: Verify that the UV lamps are positioned correctly to ensure even curing across the print area.
7. Use Rip Software Effectively
Color Management: Utilize RIP (Raster Image Processor) software to manage color profiles and ensure accurate color reproduction.
Print Preview: Use the print preview feature to check for any potential issues, such as misregistration or ink coverage, before printing.
Queue Management: Efficiently manage the print queue to optimize printing time and resource utilization.
Troubleshooting Common Issues
Even with optimized settings, issues can arise during UV flatbed printing. Here are some common problems and their solutions:
Banding: This occurs due to uneven ink deposition. Check and clean the print heads, adjust the print speed, and ensure proper head alignment.
Smudging: Inadequate curing can cause smudging. Increase UV intensity or curing time, and ensure the substrate is dry and clean.
Poor Adhesion: If the ink doesn’t adhere well, check ink compatibility with the substrate, use a primer if necessary, and ensure proper curing.
Color Shifting: Incorrect color profiles or RIP settings can cause color shifting. Calibrate the printer and RIP software, and use ICC profiles specific to the ink and substrate.
Optimizing print settings on a UV flatbed printer involves a combination of selecting the right ink, setting appropriate resolutions and speeds, configuring curing settings, preparing the substrate, calibrating the printer, and effectively using RIP software. By carefully considering these factors and regularly performing test prints, you can achieve consistent, high-quality results. Remember, the key to successful UV flatbed printing lies in understanding the interaction between the printer, the ink, the substrate, and the curing process. With patience, attention to detail, and a willingness to experiment, you can unlock the full potential of your UV flatbed printer.