Technical Insights into the Benefits of Variable Data Printing with UV Flatbed Printers
In the realm of modern printing technology, the evolution from traditional offset and lithography methods to digital printing has ushered in a new era of versatility and efficiency. Among the various digital printing techniques, variable data printing (VDP) stands out for its ability to customize each printed piece with unique information, catering to the growing demand for personalized marketing materials, packaging, and more. When combined with UV flatbed printers, VDP offers a multitude of technical benefits that enhance print quality, flexibility, and productivity. This article delves into the technical intricacies of VDP with UV flatbed printers, highlighting the advantages they bring to the printing industry.
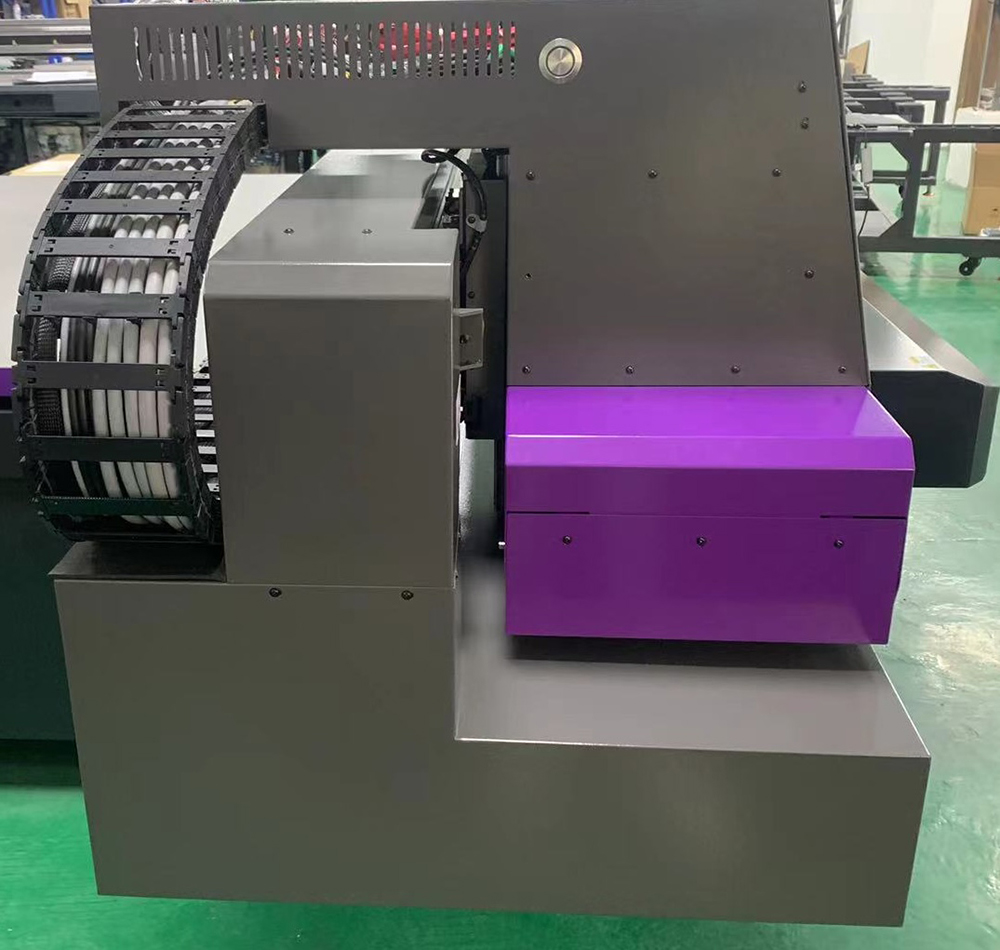
Understanding Variable Data Printing
Variable data printing is a form of digital printing that allows for the customization of each printed piece with unique elements such as text, images, and graphics. Unlike static printing, where every copy is identical, VDP enables the integration of dynamic data from databases or external sources, resulting in highly personalized outputs. This capability is particularly valuable in direct mail campaigns, where personalized content can significantly improve response rates and customer engagement.
At the heart of VDP lies sophisticated software that manages the integration of variable data into the print job. This software works in tandem with the printer’s RIP (Raster Image Processor) to ensure that each piece is rendered accurately and efficiently. The process involves several key steps: data preparation, template design, personalization, and output. Each step requires precision and coordination to achieve the desired results.
The Role of UV Flatbed Printers
UV flatbed printers are a type of digital printer that uses ultraviolet (UV) light to cure inks instantly as they are deposited onto the substrate. This technology offers several advantages over traditional solvent-based or water-based inks, including faster drying times, enhanced durability, and the ability to print on a wide range of materials.
One of the standout features of UV flatbed printers is their versatility. They can print on virtually any flat or slightly curved surface, including plastics, metals, glass, ceramics, and even textiles. This makes them ideal for a diverse range of applications, from industrial prototyping to high-end packaging and decorative printing.
Technical Benefits of Combining VDP with UV Flatbed Printers
High-Quality Output with Sharp Detail
UV flatbed printers are known for their ability to produce high-resolution prints with exceptional detail and color accuracy. When combined with VDP, this results in personalized pieces that not only look professional but also stand out due to their customized content. The instant curing of UV inks ensures that the print quality remains consistent, even on challenging substrates.
Enhanced Durability and Resistance
The UV-cured inks used in flatbed printers offer superior durability and resistance to fading, scratching, and chemicals. This is particularly important for outdoor signage, packaging, and other applications where the printed materials may be exposed to harsh environments. VDP, when applied to these durable prints, ensures that each piece not only looks great but also lasts longer.
Versatility in Substrate Handling
As mentioned earlier, UV flatbed printers can print on a wide range of materials. This versatility is further enhanced by VDP, allowing for the customization of prints on virtually any substrate. Whether it’s a custom-printed phone case, a personalized gift box, or a unique piece of art, the combination of VDP and UV flatbed printing makes it possible.
Efficient Production and Cost Savings
The instant curing of UV inks significantly reduces production times compared to traditional printing methods that require drying time. This efficiency is amplified when using VDP, as the printing process can be streamlined to handle large volumes of personalized pieces quickly. Furthermore, the ability to print directly onto substrates eliminates the need for pre-printing or lamination steps, reducing both material costs and waste.
Expanded Creative Possibilities
VDP unlocks a whole new level of creativity by enabling the integration of dynamic data into prints. With UV flatbed printers, this creativity can be pushed even further, as designers are not limited by the substrate type or the need for special coatings. The result is a virtually limitless range of personalized products that can be tailored to meet specific customer needs and preferences.
Improved Customer Engagement
Personalized prints have been shown to improve customer engagement and response rates. By using VDP with UV flatbed printers, businesses can create targeted marketing materials that resonate with individual customers. This level of personalization can lead to higher conversion rates, increased customer loyalty, and a stronger brand identity.
Technical Challenges and Solutions
While the benefits of combining VDP with UV flatbed printers are numerous, there are also some technical challenges that need to be addressed. One of the primary challenges is ensuring data integrity and accuracy throughout the printing process. This requires robust software solutions that can handle large datasets efficiently and ensure that each personalized piece is rendered correctly.
Another challenge is managing the curing process of UV inks, especially when printing on heat-sensitive substrates. Advancements in UV LED technology have helped to mitigate this issue, as they provide a cooler curing process that is less likely to damage delicate materials.
Additionally, the cost of UV flatbed printers and the associated software can be a barrier for some businesses. However, the long-term benefits in terms of efficiency, quality, and customer engagement often outweigh the initial investment.
The integration of variable data printing with UV flatbed printers represents a significant advancement in the printing industry. This combination offers a range of technical benefits, including high-quality output, enhanced durability, versatility in substrate handling, efficient production, expanded creative possibilities, and improved customer engagement. While there are technical challenges to overcome, the advancements in software and UV LED technology continue to push the boundaries of what is possible.
As businesses increasingly seek to differentiate themselves through personalized marketing and packaging, the role of VDP with UV flatbed printers will become even more crucial. By leveraging the unique capabilities of this technology, businesses can create highly customized prints that not only meet but exceed customer expectations. In the end, the technical insights gained from this combination will continue to drive innovation and growth in the printing industry for years to come.