Technical Insights into the Design and Construction of UV Flatbed Printers
In the realm of digital printing technology, UV flatbed printers have emerged as a game-changer, revolutionizing the way images and graphics are applied to a wide array of substrates. These versatile machines leverage advanced ultraviolet (UV) curing technology to instantly dry ink upon deposition, enabling high-quality, durable prints on materials ranging from rigid plastics and metals to flexible fabrics and films. This article delves into the technical intricacies of the design and construction of UV flatbed printers, exploring the key components, engineering principles, and innovative features that distinguish them from traditional printing systems.
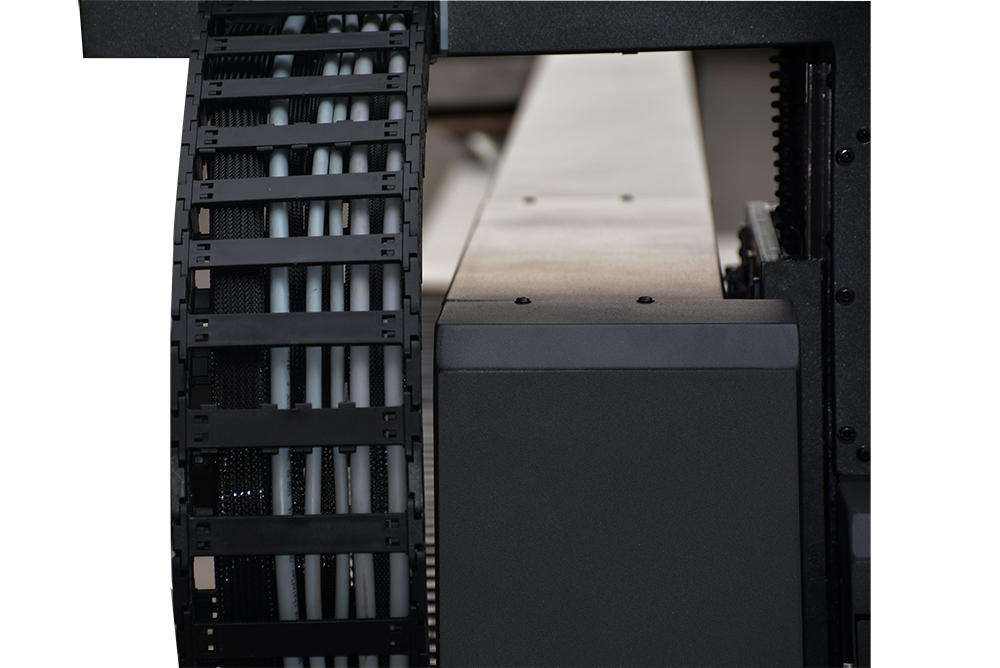
1. Understanding UV-Curing Technology
At the heart of UV flatbed printers lies the UV-curing process, a method that employs ultraviolet light to instantly solidify ink after it has been jetted onto the substrate. This technology offers several advantages over solvent-based or aqueous inks, which require time to dry and can sometimes produce harmful volatile organic compounds (VOCs). UV inks, on the other hand, are 100% solid when cured, resulting in minimal environmental impact and reduced waste.
The UV-curing mechanism typically involves a series of high-intensity UV lamps or LEDs positioned along the print path. These light sources emit UV radiation at specific wavelengths, typically in the range of 200 to 400 nanometers, which triggers a chemical reaction in the ink. This reaction, known as polymerization, converts the liquid ink into a solid, creating a durable and smudge-resistant print. The speed and efficiency of the curing process are critical, as they directly affect the printer’s productivity and the quality of the output.
2. Key Components and Their Functions
2.1 Print Heads and Ink Delivery System
UV flatbed printers utilize piezoelectric or thermal inkjet print heads to deposit ink droplets onto the substrate with high precision. Piezoelectric heads use crystals that change shape when an electric current is applied, forcing ink out of the nozzles. In contrast, thermal heads heat a small chamber of ink, causing a bubble to form and eject a droplet. The choice of print head technology depends on factors such as print resolution, speed, and ink type.
The ink delivery system ensures a consistent flow of ink to the print heads, often incorporating a closed-loop system to maintain optimal ink pressure and prevent clogging. Some printers employ a recirculating ink system, where ink continuously flows through the head and returns to a reservoir, helping to maintain ink temperature and viscosity.
2.2 Substrate Handling and Positioning
Effective substrate handling is crucial for achieving accurate and consistent prints. UV flatbed printers typically feature a flatbed table that can accommodate substrates of various sizes and thicknesses. The table may be equipped with vacuum pumps or clamps to secure the material in place during printing, preventing movement and ensuring precise registration.
Advanced models incorporate automated systems for loading and unloading substrates, as well as adjustable table heights to accommodate different material thicknesses. Some printers also offer multi-zone vacuum systems, allowing for simultaneous printing and material preparation, thereby increasing productivity.
2.3 UV Curing System
The UV curing system is a vital component, responsible for instantly solidifying the ink. It may consist of UV lamps or LED arrays, each with its own set of advantages. UV lamps offer high-intensity light output but require regular replacement and can generate heat. LEDs, on the other hand, are more energy-efficient, have a longer lifespan, and produce less heat, making them ideal for sensitive substrates.
The curing system’s design must account for uniform light distribution across the print area to avoid curing artifacts. Some printers employ multiple UV sources or dynamic curing systems that move in tandem with the print heads to ensure consistent curing.
2.4 Control Systems and Software
The control systems of UV flatbed printers are sophisticated, integrating motion control, ink delivery, and UV curing functions. They rely on advanced algorithms to manage print head operation, substrate positioning, and curing parameters, ensuring precise and efficient printing.
The printer’s software, often referred to as RIP (Raster Image Processor) software, plays a crucial role in converting digital files into a format that the printer can understand. It handles color management, image processing, and print job optimization, enabling users to achieve the desired print quality and efficiency.
3. Innovative Features and Trends
3.1 Multi-Layer Printing
One of the standout features of UV flatbed printers is their ability to print multiple layers of ink, allowing for the creation of textured effects, raised images, and three-dimensional prints. This capability is particularly valuable in applications such as packaging, where tactile elements can enhance product appeal.
3.2 White and Clear Ink Capabilities
The ability to print white and clear ink opens up new possibilities for creative expression. White ink can be used as a base layer to enhance color vibrancy on transparent or dark substrates, while clear ink can be applied as a varnish to create glossy or matte finishes, adding depth and texture to prints.
3.3 Automation and Connectivity
As with many modern manufacturing processes, automation is becoming a key driver in the evolution of UV flatbed printers. Automated features, such as material handling systems, reduce manual intervention, increasing productivity and consistency. Additionally, connectivity options, such as Wi-Fi and Ethernet, enable remote monitoring and control, facilitating integration into smart factories and workflows.
3.4 Sustainable Practices
Environmental concerns are prompting manufacturers to develop more sustainable UV flatbed printers. This includes the use of eco-friendly inks, energy-efficient UV-LED curing systems, and designs that minimize waste and energy consumption. Some printers also offer recycling programs for ink cartridges and other consumables.
UV flatbed printers represent a significant advancement in digital printing technology, offering unparalleled versatility, precision, and efficiency. Their design and construction are the result of a complex interplay of mechanical, electronic, and software systems, each optimized to deliver high-quality prints on a wide range of substrates.
As technology continues to evolve, we can expect UV flatbed printers to become even more sophisticated, with enhanced automation, improved sustainability, and innovative features that push the boundaries of what is possible in digital printing. Whether for industrial applications, signage, or artistic expression, UV flatbed printers are poised to remain at the forefront of the printing industry, enabling new levels of creativity and productivity.
In summary, the design and construction of UV flatbed printers are a testament to the ingenuity of engineers and manufacturers who continuously strive to innovate and improve. By leveraging advanced UV-curing technology, precise ink delivery systems, and sophisticated control software, these printers are transforming the way we think about digital printing, opening up new avenues for creativity and efficiency.