Technical Insights into the Working of UV Flatbed Printers
In the realm of digital printing, UV flatbed printers have emerged as a game-changer, revolutionizing the way images and designs are applied to a wide array of substrates. These versatile machines have found their niche in various industries, including signage, packaging, textiles, and even interior decoration, owing to their ability to print on virtually any flat or slightly curved surface with exceptional precision and detail. The technology behind UV flatbed printers is a fascinating blend of advanced mechanics, sophisticated software, and innovative ink chemistry, all working in harmony to produce stunning, durable prints. This article delves into the technical intricacies of UV flatbed printers, shedding light on their operation, components, and the unique advantages they offer.
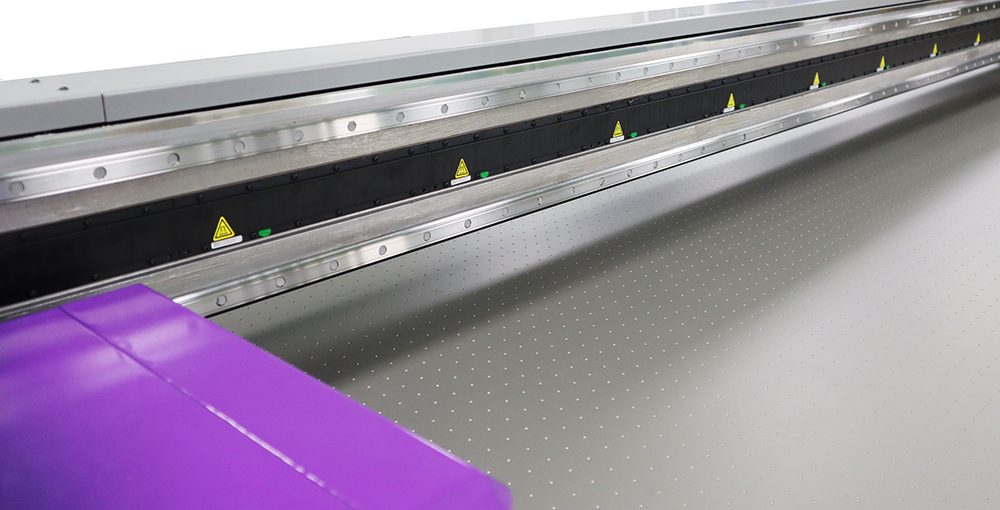
1. The Heart of the System: UV-Curable Inks
At the core of UV flatbed printing lies the use of UV-curable inks. Unlike traditional solvent-based or water-based inks, UV inks are formulated to solidify almost instantly upon exposure to ultraviolet light. This curing process is a chemical reaction triggered by the UV radiation, causing the ink’s monomers and oligomers to cross-link and form a solid, durable layer. The rapid curing time is a significant advantage, as it allows for immediate handling of the printed materials without the risk of smudging or bleeding.
UV-curable inks are composed of photoinitiators, oligomers, monomers, and various additives that enhance their performance characteristics. Photoinitiators are sensitive compounds that absorb UV light and initiate the polymerization process. Oligomers and monomers are the building blocks of the ink, which, when cross-linked, form a tough, flexible, and adherent film. Additives such as pigments, stabilizers, and flow agents tailor the ink’s properties to suit different applications.
2. The Printing Process: From Digital to Physical
The UV flatbed printing process begins with a digital file, typically created using graphic design software. This file is sent to the printer’s RIP (Raster Image Processor), which translates the vector or raster graphics into a format that the printer can understand. The RIP also manages color management, ensuring accurate color reproduction by converting the digital colors into the specific ink formulations used by the printer.
Once the file is processed, the printer’s print heads, equipped with tiny nozzles, deposit precise amounts of UV ink onto the substrate. These nozzles can eject droplets as small as a few picoliters, enabling high-resolution prints with intricate details. The print heads move across the substrate in a controlled manner, either through a gantry system for larger flatbed printers or by moving the substrate itself on a conveyor belt in some configurations.
Immediately after the ink is deposited, a UV light source, often in the form of LED lamps or mercury vapor lamps, follows closely behind, exposing the ink to UV radiation. This cures the ink almost instantaneously, fixing it to the substrate. The curing process not only solidifies the ink but also enhances its durability, making it resistant to fading, scratching, and chemical exposure.
3. Key Components and Their Functions
3.1 Print Heads and Ink Delivery System
The print heads are critical components, responsible for the accurate deposition of ink droplets. Piezoelectric or thermal technology is commonly used to eject ink droplets from the nozzles. Piezoelectric heads use crystals that change shape when an electric current is applied, forcing ink out of the nozzles. Thermal heads, on the other hand, use heat to create bubbles within the ink, propelling droplets outwards.
The ink delivery system ensures a consistent flow of ink to the print heads, maintaining optimal printing conditions. Ink tanks, supply lines, and filters are part of this system, working together to prevent clogs and ensure continuous operation.
3.2 UV Curing System
The UV curing system comprises UV lamps or LEDs that emit radiation at specific wavelengths effective for curing UV-curable inks. The lamps are positioned strategically to ensure even exposure across the printed area. Some printers use multiple lamps or dynamic curing systems that adjust the intensity and duration of exposure based on the ink type and substrate.
3.3 Motion Control System
Precise control over the movement of the print heads and the substrate is essential for high-quality prints. The motion control system, often driven by stepper motors or servo motors, ensures accurate positioning and smooth movement. Encoders and sensors provide feedback, allowing the printer to make real-time adjustments to maintain print accuracy.
3.4 Substrate Handling System
UV flatbed printers can accommodate a wide range of substrates, from rigid materials like glass, metal, and ceramics to flexible materials like textiles and films. The substrate handling system includes vacuum tables, clamps, or conveyor belts that secure the material in place during printing. Adjustable platforms and adapters further enhance the printer’s versatility, enabling it to handle different sizes and shapes of substrates.
4. Unique Advantages of UV Flatbed Printers
4.1 Versatility
One of the most significant advantages of UV flatbed printers is their versatility. They can print on almost any flat or slightly curved surface, making them ideal for a wide range of applications. This versatility eliminates the need for multiple printing processes and equipment, streamlining production and reducing costs.
4.2 Durability and Quality
UV-cured inks offer exceptional durability, resistance to fading, scratching, and chemical exposure. This makes UV flatbed prints suitable for outdoor and high-wear applications where longevity is crucial. The high resolution and precision of the prints also contribute to their superior quality, with vibrant colors and sharp details.
4.3 Environmental Benefits
UV-curable inks are more environmentally friendly than traditional solvent-based inks. They do not emit volatile organic compounds (VOCs), reducing air pollution and health risks associated with inhalation. Additionally, the instant curing process minimizes waste, as there is no need for drying time or special ventilation systems.
4.4 Efficiency and Cost-Effectiveness
The rapid curing time of UV inks significantly increases printing efficiency, allowing for faster turnaround times and higher productivity. Moreover, the ability to print directly on the final substrate eliminates the need for lamination or additional coating processes, reducing material and labor costs.
UV flatbed printers are a testament to the rapid advancements in digital printing technology. Their ability to print on a wide range of substrates with exceptional quality, durability, and efficiency has made them indispensable in various industries. The combination of UV-curable inks, precise print heads, advanced motion control systems, and innovative substrate handling solutions underpins their success. As technology continues to evolve, UV flatbed printers are likely to become even more versatile, efficient, and environmentally friendly, further expanding their applications and market reach. For businesses seeking to enhance their printing capabilities, investing in a UV flatbed printer is a decision that promises to deliver both immediate and long-term benefits.