Technical Insights into Troubleshooting Common UV Flatbed Printer Issues
In the realm of digital printing, UV flatbed printers have revolutionized the way we approach print production, offering versatility, precision, and high-quality output across a wide range of materials. These printers utilize ultraviolet (UV) light to instantly cure inks, enabling rapid and efficient printing on substrates such as glass, metal, plastics, and even textiles. Despite their advanced capabilities, UV flatbed printers are not immune to issues that can disrupt workflow and compromise print quality. This article delves into the technical aspects of troubleshooting some of the most common problems encountered with UV flatbed printers, providing insights and practical solutions to help maintain optimal performance.
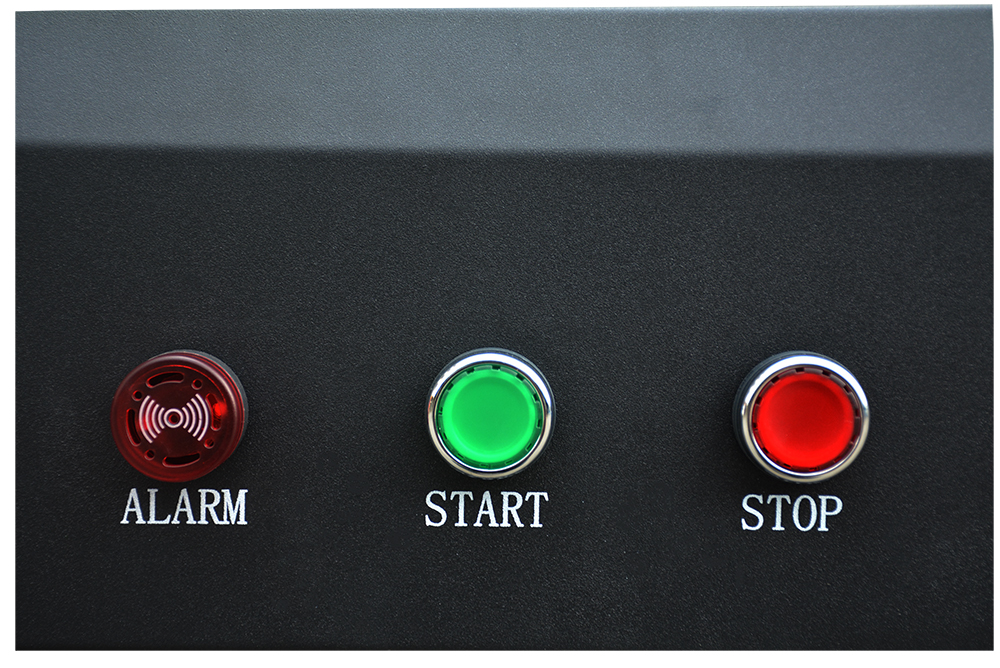
1. Print Quality Issues
A. Banding and Striping
Banding and striping are visible lines or patterns that appear perpendicular or parallel to the print direction. These imperfections can stem from several factors:
Nozzle Clogs: Over time, ink can dry or accumulate debris within the nozzles, obstructing ink flow. Regular cleaning cycles and maintenance routines are crucial to prevent clogs.
Ink Supply Problems: Air bubbles in the ink lines or inconsistent ink flow can cause intermittent printing. Check ink lines for bubbles and ensure the ink supply system is properly primed.
Mechanical Misalignment: Wear and tear or improper calibration of the print head carriage can lead to misalignment. Recalibrate the printer according to the manufacturer’s guidelines.
B. Poor Color Accuracy
Achieving accurate colors is paramount in professional printing. Discrepancies may arise due to:
Ink Profiles: Ensure that the correct ICC (International Color Consortium) profiles are used for both the printer and the specific media being printed on.
Ink Aging: UV inks can degrade over time, affecting color consistency. Store inks in cool, dark places and use them within their recommended shelf life.
Print Head Health: A partially clogged or worn-out print head can alter ink deposition, impacting color output. Regular inspections and cleanings are essential.
2. Curing Problems
A. Incomplete Curing
If inks do not fully cure, they may remain tacky or smudge easily. This issue often relates to:
UV Lamp Intensity: The UV lamps might be aging or not emitting sufficient energy. Use a UV meter to check lamp output and replace lamps as needed.
Lamp Positioning: Incorrect lamp positioning or angle can result in uneven curing. Adjust lamps to ensure even coverage across the print area.
Print Speed and Lamp Power: Faster print speeds may require higher UV lamp power to maintain adequate curing. Adjust settings to balance speed and curing efficiency.
B. Overcuring
Excessive curing can cause brittleness, cracking, or discoloration of the printed material. Consider the following:
Lamp Power Settings: Reduce UV lamp power or adjust the curing time to prevent overexposure.
Material Sensitivity: Some materials are more sensitive to UV light than others. Test different curing parameters for each material type.
3. Mechanical and Hardware Issues
A. Print Head Crashes
A print head crash occurs when the head comes into contact with the print bed or material, potentially damaging both. Causes include:
Z-Axis Calibration: Incorrect Z-axis height settings can cause the print head to be too low. Recalibrate the Z-axis to ensure proper clearance.
Material Thickness Variability: Variations in material thickness can affect print head clearance. Use material gauges or shims to maintain consistent height.
Software Glitches: Firmware bugs or software errors can miscalculate head movement. Update firmware and software to the latest versions.
B. Carriage Movement Issues
Smooth carriage movement is critical for precise printing. Problems may arise from:
Dirty Rails: Dust and debris can accumulate on the guide rails, impeding movement. Clean rails regularly with appropriate solvents.
Belt Tension: Loose or overly tight belts can cause erratic movement. Adjust belt tension according to the printer’s specifications.
Motor Failures: Worn-out or faulty motors can affect carriage movement. Test motors and replace if necessary.
4. Software and Connectivity Problems
A. Print Job Errors
Print jobs may fail to start or stop mid-print due to:
File Corruption: Corrupted print files can cause errors. Verify file integrity before printing and use reliable file transfer methods.
RIP Software Issues: Raster Image Processor (RIP) software malfunctions can disrupt print jobs. Update RIP software and ensure compatibility with printer drivers.
Network Connectivity: Unstable network connections can interrupt data transfer. Use wired connections when possible and ensure network stability.
B. Interface Lag
Slow or unresponsive printer interfaces can hinder operation:
Firmware Bugs: Outdated or buggy firmware can cause interface lag. Regularly update firmware to address known issues.
Computer Performance: Insufficient computer resources can affect interface responsiveness. Ensure the controlling computer meets the printer’s system requirements.
5. Environmental Considerations
A. Temperature and Humidity
Extreme temperatures and humidity levels can affect print quality and printer performance:
Temperature Control: Maintain the printer environment within the recommended temperature range to prevent ink viscosity changes and mechanical stress.
Humidity Levels: High humidity can cause condensation, while low humidity can lead to static electricity issues. Use dehumidifiers or humidifiers to maintain optimal levels.
B. Dust and Contaminants
Dust and other contaminants can settle on print heads, media, and internal components, leading to various issues:
Regular Cleaning: Implement a regular cleaning schedule for the printer and surrounding area. Use air filters to reduce dust accumulation.
Material Handling: Handle materials carefully to avoid introducing contaminants. Store materials in clean, dry conditions.
Troubleshooting UV flatbed printer issues requires a combination of technical knowledge, attention to detail, and proactive maintenance practices. By understanding the root causes of common problems—such as print quality issues, curing difficulties, mechanical failures, software glitches, and environmental factors—operators can efficiently diagnose and resolve issues, ensuring consistent and high-quality print output. Regular maintenance, proper calibration, and adherence to manufacturer guidelines are key to maximizing the lifespan and performance of UV flatbed printers. With these insights, printer operators can optimize their workflows, minimize downtime, and achieve outstanding print results.