Technical Insights: UV Flatbed Printer Head Alignment Procedures
In the realm of digital printing, UV flatbed printers have revolutionized the way we approach print production, especially for a wide range of materials and applications. These versatile machines offer high-quality, durable prints on substrates varying from rigid materials like glass and metal to flexible ones such as vinyl and fabric. A crucial aspect of maintaining optimal print quality in UV flatbed printers is the precise alignment of the print heads. Misalignment can lead to a myriad of issues, including banding, color registration errors, and overall poor image quality. This article delves into the technical intricacies of UV flatbed printer head alignment procedures, providing a comprehensive guide to ensure accurate and consistent print outputs.
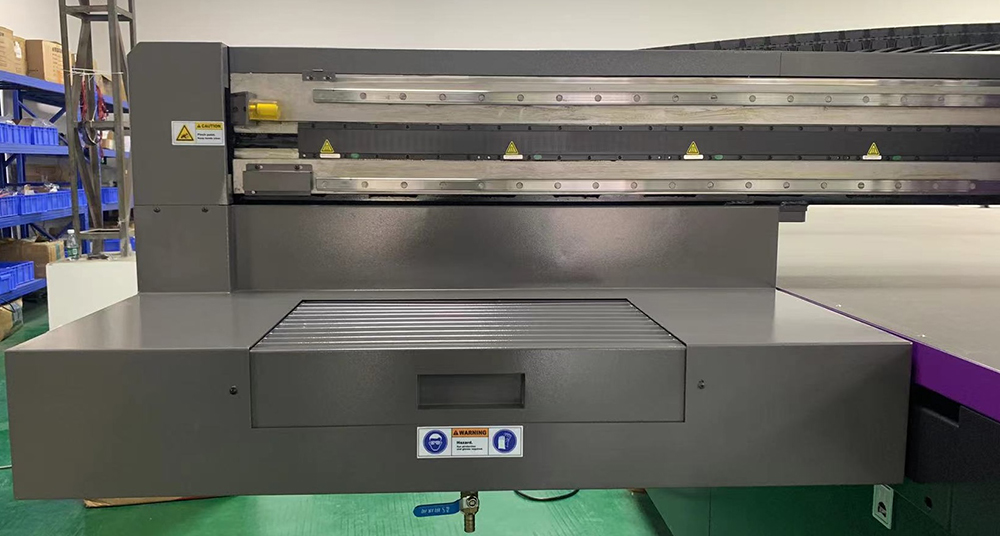
Understanding the Importance of Print Head Alignment
Print head alignment is a fundamental process that ensures each nozzle in the print head deposits ink in the exact position relative to the others. This precision is vital because even minute misalignments can result in visible artifacts on the printed material, compromising the overall aesthetic and professionalism of the output. Proper alignment not only enhances image quality but also maximizes the efficiency and lifespan of the printer by preventing unnecessary wear and tear on the print heads and other components.
Preliminary Checks and Preparations
Before embarking on the alignment procedure, it is essential to perform a series of preliminary checks to ensure that the printer is in optimal condition. Start by inspecting the printer for any visible signs of damage or debris that might interfere with the alignment process. Clean the print heads and the surrounding area thoroughly using approved cleaning solutions and materials to avoid any contaminants that could affect performance.
Next, verify that the printer’s firmware is up to date. Manufacturers often release firmware updates that can improve printer performance and address alignment-related issues. Additionally, ensure that the media is correctly loaded and secured to prevent any shifting during the printing process, which could mistakenly be interpreted as alignment problems.
Initial Alignment Procedure
The initial alignment procedure typically involves both automatic and manual steps, depending on the printer model. Most modern UV flatbed printers are equipped with advanced sensors and software that can perform a significant portion of the alignment automatically.
Automatic Alignment:
Access the printer’s control panel or software interface.
Navigate to the maintenance or settings menu and select the ‘Print Head Alignment’ option.
The printer will then initiate an automatic alignment sequence. This may involve printing a test pattern on a special alignment sheet or directly on the print bed if equipped with a built-in sensor array.
The printer’s sensors will scan the test pattern to detect any misalignments and make the necessary adjustments.
Manual Fine-Tuning (if required):
In some cases, automatic alignment may not achieve perfect results, necessitating manual intervention.
Print a detailed test pattern that includes fine lines, cross-hairs, or color blocks.
Visually inspect the test pattern for any misalignments. Look for gaps, overlaps, or color shifts between different sections.
Use the printer’s adjustment tools to manually tweak the position of each print head. This may involve adjusting screws, using a digital interface to input precise offset values, or a combination of both.
Advanced Alignment Techniques
For applications requiring extremely high precision, such as fine art reproduction or industrial printing, advanced alignment techniques may be necessary. These techniques often involve:
Micro-Adjustment Tools:
Some printers offer micro-adjustment capabilities that allow for fine-tuning the print head position in increments as small as fractions of a millimeter.
Utilize these tools to make minute adjustments based on detailed visual inspections or high-resolution scans of test prints.
Custom Alignment Patterns:
Develop custom alignment patterns tailored to the specific requirements of your print jobs. These patterns can include intricate details that highlight even the smallest misalignments.
Print and analyze these patterns under controlled lighting conditions to accurately assess and adjust the print head alignment.
Software-Assisted Alignment:
Leverage advanced software tools that can analyze scanned images of test prints and provide precise alignment recommendations.
These tools use sophisticated algorithms to detect and correct misalignments with a high degree of accuracy.
Post-Alignment Verification
After completing the alignment procedure, it is crucial to verify the results to ensure that the print heads are correctly aligned. This can be done by:
Printing a Verification Pattern:
Print a new test pattern that includes elements similar to those used during the alignment process.
Carefully inspect the pattern for any signs of misalignment, paying close attention to detail and color registration.
Real-World Print Test:
Perform a test print on the actual material and with the settings that will be used for the final print job.
Evaluate the print for quality, ensuring that there are no visible alignment issues.
Maintenance and Regular Alignment Checks
Maintaining proper print head alignment is an ongoing process. Regularly scheduled alignment checks and maintenance procedures can help prevent misalignments and ensure consistent print quality. Factors such as temperature fluctuations, frequent use, and the type of materials being printed can all affect alignment over time.
Establish a routine maintenance schedule that includes periodic alignment checks, cleaning of the print heads and surrounding areas, and inspections for any signs of wear or damage. Additionally, train operators to recognize the signs of potential alignment issues and to perform basic alignment adjustments as needed.
UV flatbed printer head alignment is a critical aspect of achieving high-quality print outputs. By following a systematic approach that includes preliminary checks, automatic and manual alignment procedures, advanced techniques for precision, and post-alignment verification, you can ensure that your UV flatbed printer produces consistent, professional-grade prints. Regular maintenance and operator training are also essential to maintain optimal alignment and print quality over time. With proper attention to detail and a thorough understanding of the alignment process, you can maximize the potential of your UV flatbed printer and deliver outstanding results for a wide range of applications.