Technical Tips for Achieving Fine Detail in UV Flatbed Printing
UV flatbed printing has revolutionized the printing industry, offering unparalleled versatility and precision in producing high-quality prints on a wide range of substrates. Whether you’re printing on rigid materials like glass, metal, or plastic, or flexible media like vinyl or fabric, UV flatbed printers can deliver stunning results with intricate details and vibrant colors. However, achieving fine detail in UV flatbed printing is not just about having the right equipment; it also requires a deep understanding of the printing process, meticulous preparation, and careful management of various technical parameters. In this article, we will explore some essential technical tips to help you achieve exceptional detail in your UV flatbed printing endeavors.
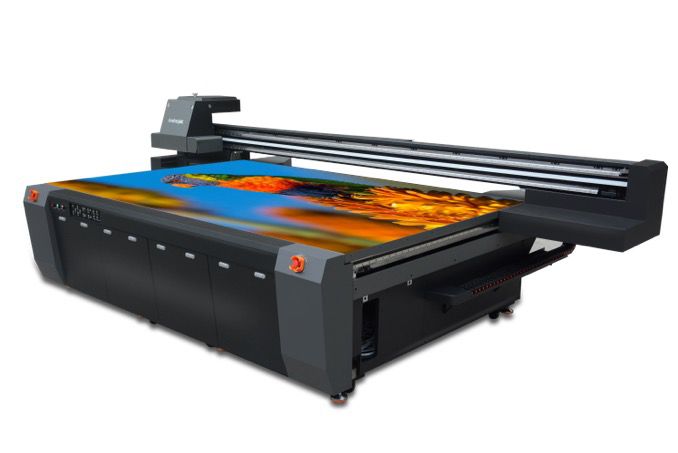
1. Understanding the Importance of Resolution
Resolution is a critical factor in determining the level of detail that can be achieved in any printing process. In UV flatbed printing, resolution refers to the number of dots per inch (DPI) that the printer can produce. Higher DPI means more dots per inch, resulting in finer details and sharper images. Most modern UV flatbed printers offer resolutions ranging from 600 DPI to 1440 DPI or even higher. While higher resolution generally leads to better detail, it’s essential to strike a balance between resolution and other factors like print speed and ink usage.
Tip: For the finest details, aim for a resolution of at least 1200 DPI. However, consider the specific requirements of your project and adjust the resolution accordingly to optimize both quality and efficiency.
2. Choosing the Right Ink and Substrate
The choice of ink and substrate plays a crucial role in the final print quality. UV inks are designed to cure instantly under UV light, providing excellent adhesion and durability. However, not all UV inks are created equal. Some inks are better suited for specific substrates or require particular printing conditions to achieve optimal results.
Tip: Work with your ink supplier to choose a high-quality UV ink that is compatible with your printer and the substrate you’re printing on. Additionally, ensure that the substrate is clean, dry, and free of any contaminants that could affect ink adhesion.
3. Proper Printer Calibration
Printer calibration is the process of adjusting the printer’s settings to ensure accurate color reproduction and print quality. This includes calibrating the print heads, aligning them correctly, and setting the appropriate ink drop sizes. Improper calibration can lead to issues like banding, color shifting, and loss of detail.
Tip: Perform regular printer calibration checks, especially before starting a new project or after making significant changes to the printer settings. Use calibration tools and software provided by the printer manufacturer to ensure precise and consistent results.
4. Managing Print Speed and Curing
Print speed and curing are intertwined factors that can significantly impact the detail and quality of your prints. Faster print speeds can increase productivity but may sacrifice some detail due to ink spread or incomplete curing. On the other hand, slower speeds may provide better detail but can reduce efficiency and increase production costs.
Tip: Find the optimal balance between print speed and curing. Test different speed settings and observe the impact on print quality. Ensure that the UV lamps are properly maintained and calibrated to provide consistent and thorough curing of the ink.
5. Using High-Quality Print Files
The quality of your print files is just as important as the printing process itself. Low-resolution images, poorly designed graphics, or incorrect file formats can all lead to a loss of detail in the final print.
Tip: Start with high-resolution digital files (preferably 300 DPI or higher). Use professional graphic design software to create or edit your files, ensuring that all elements are properly aligned and scaled. Save your files in a printer-friendly format like PDF or TIFF to maintain image quality.
6. Adjusting Ink Density and Drop Size
Ink density and drop size are two parameters that can be adjusted to fine-tune the level of detail in your prints. Ink density refers to the amount of ink deposited on the substrate, while drop size refers to the volume of ink in each droplet.
Tip: Experiment with different ink density and drop size settings to find the optimal combination for your specific project. Higher ink densities and smaller drop sizes can enhance detail but may require more precise control of the printing process.
7. Controlling Print Head Height
The distance between the print heads and the substrate, known as the print head height, can affect the quality and detail of the print. If the heads are too close, they may cause smearing or damage to the substrate. If they’re too far, the ink droplets may spread, reducing detail.
Tip: Adjust the print head height according to the manufacturer’s recommendations and the specific characteristics of your substrate. For materials with uneven surfaces, consider using a printer with adjustable head height or employing techniques like shimming to ensure consistent print quality.
8. Utilizing Advanced Printing Techniques
Advanced printing techniques like multi-pass printing, variable dot printing, and grayscale printing can further enhance the level of detail in your UV flatbed prints.
Tip: Multi-pass printing involves laying down multiple layers of ink to build up color and detail gradually. Variable dot printing adjusts the size of ink droplets to create smoother gradients and finer details. Grayscale printing uses a wider range of dot sizes to simulate continuous tones, improving image quality. Experiment with these techniques to see which ones work best for your projects.
9. Regular Maintenance and Cleaning
Maintaining your UV flatbed printer is essential for ensuring consistent print quality and longevity. Regular cleaning of the print heads, wiper blades, and other components can prevent clogs, ink build-up, and other issues that can affect detail and overall print quality.
Tip: Follow the manufacturer’s maintenance schedule and guidelines for cleaning and servicing your printer. Use approved cleaning solutions and tools to avoid damaging the printer or its components.
10. Post-Processing Techniques
Finally, post-processing techniques like cutting, trimming, and laminating can help enhance the final appearance and durability of your prints, especially when it comes to fine details.
Tip: Use precision cutting tools and equipment to ensure clean, accurate edges. Consider applying a protective laminate or coating to your prints to protect them from wear and tear, UV exposure, and other environmental factors that could degrade the detail over time.
In conclusion, achieving fine detail in UV flatbed printing requires a combination of high-quality equipment, careful preparation, and meticulous attention to detail throughout the entire printing process. By following the tips outlined in this article, you can optimize your UV flatbed printing workflow to produce stunning prints with exceptional detail and clarity. Whether you’re a seasoned professional or just starting out in the world of UV printing, these techniques will help you take your prints to the next level.