Technical Tips for Improving Print Resolution in UV Flatbed Printers
Technical Tips for Improving Print Resolution in UV Flatbed Printers
In the realm of digital printing, UV flatbed printers have revolutionized the way we approach printing on a variety of substrates. Their ability to produce high-quality prints on rigid materials such as metal, glass, wood, and plastics has made them indispensable in industries ranging from signage to fine art. However, achieving optimal print resolution can sometimes be a challenge, especially when dealing with intricate designs or demanding clients. This article aims to provide a comprehensive guide to improving print resolution in UV flatbed printers through a series of technical tips that focus on both hardware adjustments and software optimizations.
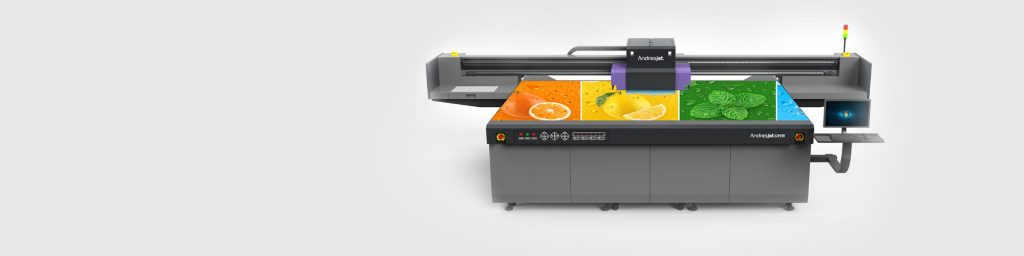
1. Understanding Print Resolution
Before diving into the tips, it’s crucial to understand what print resolution means in the context of UV flatbed printers. Print resolution refers to the number of ink droplets per inch (dpi) that the printer can deposit on the substrate. Higher dpi values generally result in sharper, more detailed images. Most UV flatbed printers offer resolutions ranging from 300 dpi to 1440 dpi or even higher. However, simply setting the printer to its highest resolution does not always guarantee the best print quality. Various factors must be considered to ensure that the printer performs at its best.
2. Calibrating the Printer
Proper calibration is the foundation of achieving excellent print resolution. Calibration involves adjusting the printer’s settings to ensure that colors are accurate, ink droplet placement is precise, and the overall print quality is optimal. Here are some steps to calibrate your UV flatbed printer:
Color Calibration: Use a color calibration tool or software to align the printer’s color output with industry standards. This process typically involves printing a series of test patterns and adjusting the printer’s color settings accordingly.
Head Alignment: Ensure that the print heads are aligned correctly. Misaligned heads can result in banding, blurring, or uneven ink distribution. Most printers have a built-in head alignment feature that can be accessed through the printer’s control panel or software.
Media Settings: Adjust the printer’s media settings to match the type of substrate being used. Different materials require different ink adhesion properties and drying times. Consult the printer’s manual or the manufacturer’s website for recommended settings.
3. Choosing the Right Ink and Substrate
The quality of the ink and the substrate plays a significant role in determining print resolution. Here are some tips for selecting the best ink and substrate:
Ink Quality: Opt for high-quality UV-curable inks that are specifically designed for your printer model. Cheap or incompatible inks can cause clogging, poor adhesion, and reduced print quality.
Substrate Compatibility: Choose a substrate that is compatible with UV inks and suitable for your application. Some substrates may require special pre-treatment or coating to ensure proper ink adhesion and cure. Test different substrates to find the one that provides the best results for your specific project.
Ink Viscosity: Adjust the ink viscosity according to the printer’s specifications and the substrate being used. Incorrect viscosity can lead to ink bleeding, poor detail reproduction, and other print defects.
4. Optimizing Print Settings
The printer’s software provides a wealth of settings that can be adjusted to improve print resolution. Here are some key settings to consider:
Resolution Setting: While setting the printer to its highest resolution may seem like the best option, it’s not always necessary. Higher resolutions can slow down the printing process and increase ink consumption. Determine the optimal resolution based on the complexity of the design and the viewing distance of the final print.
Pass Count: The number of times the print heads pass over the substrate (pass count) can affect print quality. More passes generally result in better ink coverage and detail reproduction but can also increase printing time. Experiment with different pass counts to find the best balance between quality and efficiency.
Dot Gain: Dot gain refers to the enlargement of ink dots on the substrate due to ink spread. Adjust the dot gain settings to ensure that the printed image matches the intended design. Too much dot gain can lead to overly dark or blurred images, while too little can result in light or patchy prints.
Drying/Curing Time: Ensure that the UV lamps are properly calibrated to provide the right amount of curing energy. Over-curing can cause ink to crack or fade, while under-curing can result in poor adhesion and smudging. Follow the manufacturer’s recommendations for curing times and lamp intensity.
5. Maintaining the Printer
Regular maintenance is essential for maintaining optimal print resolution. Here are some maintenance tips:
Cleaning the Print Heads: Regularly clean the print heads to remove any ink residue or debris that may clog the nozzles. Most printers have a built-in cleaning function that can be accessed through the printer’s software.
Replacing Ink Cartridges: Replace ink cartridges when they are low or empty to avoid running the printer with insufficient ink. Empty cartridges can cause print heads to clog and reduce print quality.
Checking for Wear and Tear: Inspect the printer’s components, such as belts, rollers, and guides, for signs of wear and tear. Replace any worn parts to ensure smooth and accurate operation.
Updating Firmware and Software: Keep the printer’s firmware and software up to date to ensure compatibility with new inks, substrates, and features. Manufacturers often release updates that address known issues and improve printer performance.
6. Post-Processing Techniques
Finally, post-processing techniques can further enhance print resolution and overall print quality. Here are some techniques to consider:
Lamination: Applying a protective laminate can improve the durability and appearance of the print. Lamination can also help to even out the ink’s appearance and reduce the visibility of any minor imperfections.
Varnishing: A UV varnish can be applied to specific areas of the print to add a glossy or matte finish, enhancing the contrast and depth of the image.
Cutting and Trimming: Use a precision cutter or trimmer to ensure that the edges of the print are clean and straight. This is especially important for prints that will be framed or displayed in a way that highlights the edges.
Achieving optimal print resolution in UV flatbed printers requires a combination of proper calibration, ink and substrate selection, print setting optimizations, regular maintenance, and post-processing techniques. By following the tips outlined in this article, you can improve the print quality of your UV flatbed printer and produce high-resolution prints that meet the demands of even the most discerning clients. Remember that the key to success is experimentation and continuous learning. Don’t be afraid to try new settings, inks, and substrates to find the perfect combination for your specific needs.