Technical Tips for Operating a UV Flatbed Printer
Technical Tips for Operating a UV Flatbed Printer
Operating a UV flatbed printer requires a combination of technical know-how, attention to detail, and an understanding of the printer’s unique capabilities. UV flatbed printers are known for their versatility in printing on various materials and substrates, making them a popular choice for businesses in the signage, packaging, and promotional products industries. To ensure optimal performance and print quality, here are some technical tips for operating a UV flatbed printer effectively.
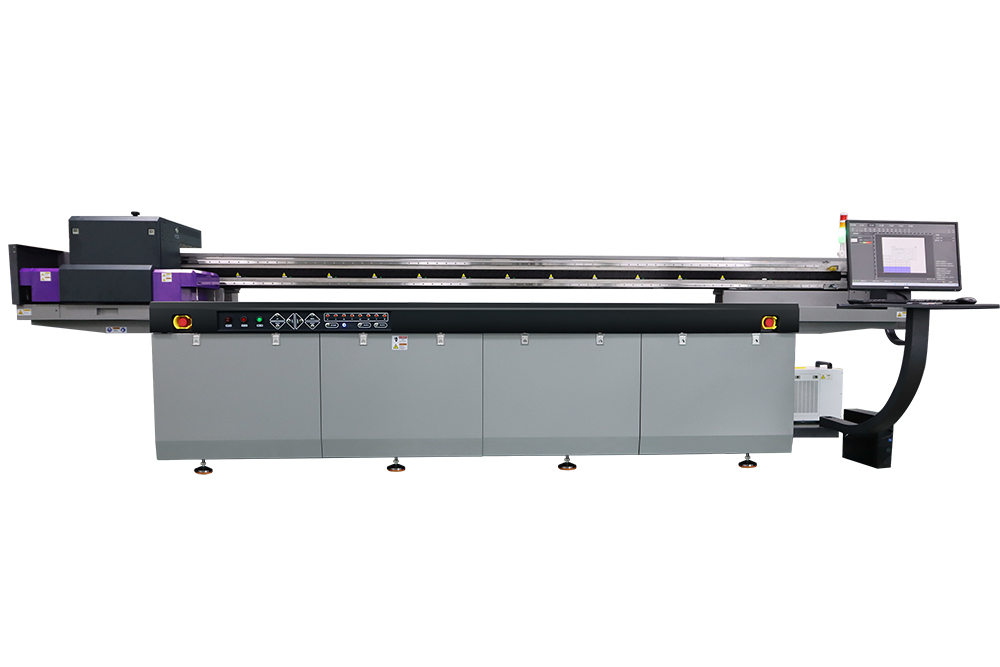
1. Understanding UV Flatbed Printer Technology
UV flatbed printers use ultraviolet (UV) light to cure or dry ink immediately after it is applied to the substrate. This process allows for faster printing speeds and eliminates the need for drying time, making UV printers ideal for high-volume production. The printer typically consists of a flatbed where the material is placed, inkjet print heads that deposit ink onto the material, and a UV light source that cures the ink instantly.
2. Preparing the Workspace
Before operating the UV flatbed printer, ensure that the workspace is clean, dust-free, and well-ventilated. Dust particles can affect print quality, causing imperfections in the final output. Additionally, proper ventilation is crucial when using UV ink, as some formulations may emit volatile organic compounds (VOCs) during the curing process.
3. Material Preparation
Not all materials are suitable for UV printing. It’s essential to choose materials that are compatible with UV ink and the printer’s specifications. Prepare the material by ensuring it is clean, dry, and free from any contaminants that could affect print quality. For best results, perform a test print on a small section of the material to ensure compatibility and color accuracy.
4. Printer Calibration and Maintenance
Regular calibration and maintenance are vital for achieving consistent print quality. Calibrate the printer according to the manufacturer’s recommendations, which may include adjusting print head alignment, ink flow, and UV light intensity. Additionally, clean the print heads regularly to prevent ink buildup and clogged nozzles.
5. Ink Management
UV ink is more viscous than traditional inkjet ink, requiring careful management to ensure optimal print quality. Keep ink cartridges or tanks sealed and avoid exposing them to direct sunlight or extreme temperatures, which can affect ink consistency. Monitor ink levels regularly and replace cartridges promptly to avoid interruptions during printing.
6. Color Management
Achieving accurate colors is crucial in UV printing. Use a color management system to ensure consistent color reproduction across different prints and materials. Calibrate the printer’s color settings using industry-standard color profiles or create custom profiles for specific materials and applications.
7. Print Settings and Resolution
Adjust print settings according to the material and desired output quality. Higher resolutions are suitable for detailed graphics and fine text, but they may increase print time. Find the right balance between resolution and production speed to optimize efficiency.
8. Print Bed Preparation
Ensure the print bed is level and secure before starting a print job. Use the printer’s built-in leveling tools or add shims if necessary to achieve a flat, even surface. Proper bed preparation is essential for achieving uniform ink deposition and preventing smudging or banding.
9. UV Light Curing
UV light curing is a critical step in the printing process. Monitor the UV light source for any signs of degradation, such as reduced intensity or uneven curing. Replace the UV bulbs according to the manufacturer’s recommended schedule to maintain consistent print quality.
10. Software and File Preparation
Use printer-specific software or a compatible design program to prepare print files. Ensure that files are in the correct format, such as PDF or TIFF, and that they are optimized for UV printing. Check for any design errors or issues that could affect print quality, such as low-resolution images or incompatible color profiles.
11. Test Prints and Quality Control
Before starting a large print job, perform test prints to ensure everything is set up correctly. Check for issues such as ink bleeding, color accuracy, and print resolution. Implement a quality control process to inspect prints regularly and make adjustments as needed to maintain consistent output.
12. Safety Considerations
UV ink and the curing process can pose safety risks. Wear appropriate personal protective equipment (PPE), such as gloves and safety glasses, when handling UV ink or operating the printer. Follow the manufacturer’s safety guidelines and local regulations for UV printing equipment.
13. Environmental Considerations
UV printing is generally more environmentally friendly than traditional printing methods, as it does not require solvents or produce harmful emissions during the curing process. However, it’s still essential to dispose of ink cartridges and other consumables according to local regulations and to minimize waste through efficient material usage.
14. Training and Support
Ensure that operators are trained in the proper use and maintenance of the UV flatbed printer. Regular training sessions can help operators stay up-to-date on new techniques and best practices. Additionally, maintain a relationship with the printer manufacturer for technical support and assistance with any issues that may arise.
Conclusion
Operating a UV flatbed printer requires attention to detail and a thorough understanding of the printer’s capabilities and limitations. By following these technical tips, businesses can ensure optimal print quality, efficient production, and long-term reliability from their UV flatbed printers. Regular maintenance, proper material preparation, and attention to safety and environmental considerations are key to success in UV printing. With the right approach, UV flatbed printers can be a valuable asset for businesses in a wide range of industries.