Technical Tips for Reducing Banding and Other Artifacts in UV Flatbed Printing
UV flatbed printing has revolutionized the printing industry, offering high-quality, durable prints on a wide range of substrates. However, like any advanced technology, it comes with its own set of challenges. One of the most common issues faced by UV flatbed printer operators is the occurrence of banding and other artifacts. These imperfections can detract from the overall appearance of the print and, in some cases, render it unusable. In this article, we will delve into the technical aspects of reducing banding and other artifacts in UV flatbed printing, providing practical tips and strategies to help you achieve superior print quality.
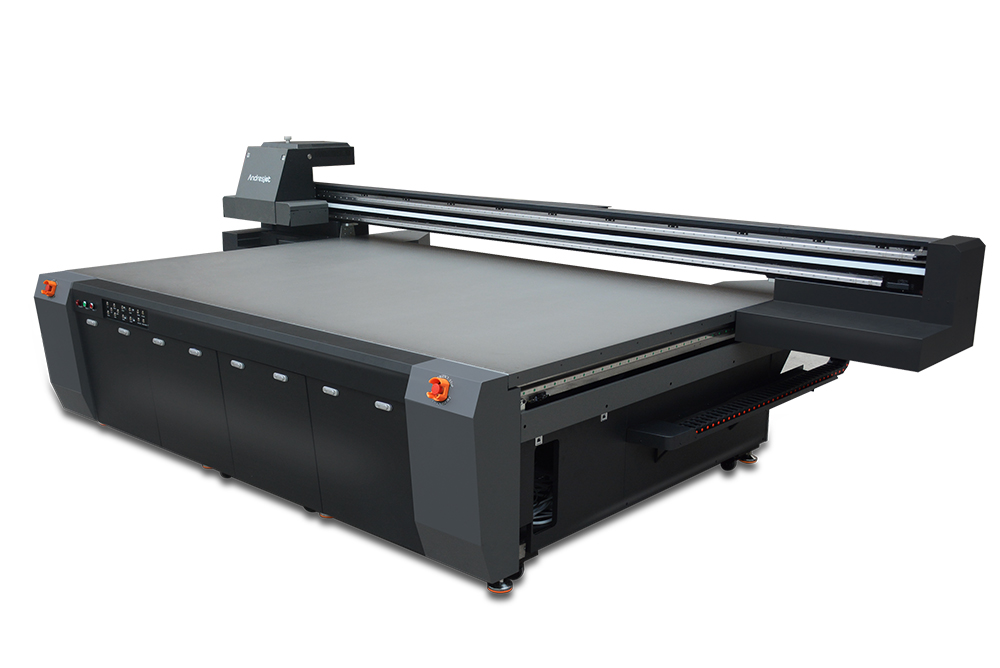
Understanding Banding and Artifacts
Before we dive into the solutions, it’s essential to understand what banding and artifacts are. Banding refers to visible lines or stripes that appear across the printed image, often running perpendicular to the direction of the print heads. Artifacts, on the other hand, are any unwanted marks, distortions, or irregularities in the print. These can include streaks, dots, smudges, and color inconsistencies.
Banding and artifacts can stem from various sources, including mechanical issues, ink flow problems, and software-related factors. Identifying the root cause is crucial for effective troubleshooting and resolution.
Mechanical Adjustments
One of the first areas to examine when dealing with banding and artifacts is the mechanical setup of the printer. Here are some key adjustments that can make a significant difference:
Print Head Alignment:
Ensure that the print heads are correctly aligned. Misalignment can lead to uneven ink deposition, resulting in banding.
Use the printer’s built-in alignment tools to fine-tune the position of each print head.
Print Bed Leveling:
A level print bed is essential for consistent ink application. An uneven bed can cause the substrate to move or flex, leading to artifacts.
Regularly check and adjust the print bed leveling using the manufacturer’s recommended procedures.
Media Handling:
Ensure that the media is securely loaded and properly tensioned. Loose or slipping media can cause shifting during printing, resulting in banding.
Use media guides and clamps to keep the substrate stable throughout the printing process.
Maintenance and Cleaning:
Regular maintenance, including cleaning the print heads and wiper blades, can prevent ink build-up and clogging, which are common causes of banding.
Follow the printer’s maintenance schedule and use approved cleaning solutions and tools.
Ink and Ink Flow
Ink-related issues are another common source of banding and artifacts. Here are some strategies to address these problems:
Ink Viscosity:
Maintain the correct ink viscosity for optimal flow and print quality. Ink that is too thick or too thin can cause banding and other artifacts.
Use the printer’s ink management system to monitor and adjust ink viscosity as needed.
Ink Channel Clogging:
Clogged ink channels can disrupt the ink flow, leading to inconsistent printing.
Perform regular nozzle checks and cleanings to keep the ink channels clear.
Ink Jetting Frequency:
Adjust the ink jetting frequency to ensure consistent ink deposition. Too high or too low a frequency can cause banding.
Experiment with different jetting settings to find the optimal balance for your specific printing needs.
Ink Temperature:
Ink temperature can affect its viscosity and flow properties. Ensure that the ink is within the recommended temperature range for optimal performance.
Use a heated ink system if necessary to maintain a consistent ink temperature.
Software and Printing Parameters
Software settings and printing parameters also play a crucial role in reducing banding and artifacts. Here are some tips for optimizing your software and printing settings:
Resolution and Pass Count:
Increase the print resolution and pass count for better ink coverage and reduced banding.
However, be mindful of the trade-off between quality and printing speed. Higher resolutions and pass counts will slow down the printing process.
Print Speed:
Printing too fast can cause the ink to dry incompletely, leading to banding and other artifacts.
Reduce the print speed to allow for proper ink drying and adhesion.
Rasterization and Ripping:
Ensure that the rasterization and ripping processes are optimized for your specific printer and ink type.
Use high-quality raster image processors (RIPs) to ensure accurate and consistent image rendering.
Color Management:
Implement robust color management practices to ensure consistent color reproduction and reduce color banding.
Calibrate your printer and monitor regularly to maintain color accuracy.
Environmental Factors
Finally, environmental conditions can also impact the quality of UV flatbed prints. Here are some environmental factors to consider:
Temperature and Humidity:
Control the temperature and humidity in your printing environment to prevent ink from drying too quickly or too slowly.
Use a dehumidifier or humidifier as needed to maintain optimal conditions.
Dust and Contaminants:
Keep your printing environment clean and free of dust and other contaminants that can adhere to the print heads or substrate, causing artifacts.
Use air filters and regular cleaning procedures to maintain a clean printing environment.
UV Light Exposure:
Ensure that the UV lights are functioning correctly and are not overexposed or underexposed.
Regularly check and replace UV bulbs as needed to maintain consistent curing performance.
Reducing banding and other artifacts in UV flatbed printing requires a comprehensive approach that addresses mechanical, ink-related, software, and environmental factors. By following the tips and strategies outlined in this article, you can significantly improve the quality of your prints and achieve the professional results that your customers expect.
Remember, the key to success is ongoing monitoring and adjustment. Regularly check your printer’s performance, and don’t hesitate to make adjustments as needed. With patience and attention to detail, you can master the art of UV flatbed printing and produce stunning prints that stand the test of time.