The Advantages of UV Curing in Flatbed Printing Processes
In the realm of digital printing, technology continues to evolve, bringing with it innovations that enhance efficiency, quality, and versatility. Among these advancements, UV curing has emerged as a game-changer, particularly in flatbed printing processes. This technique offers a multitude of benefits that make it a preferred choice for printers seeking to optimize their operations and deliver superior results. By examining the intricacies of UV curing and its application in flatbed printing, we can better understand why this technology has gained such widespread acceptance.
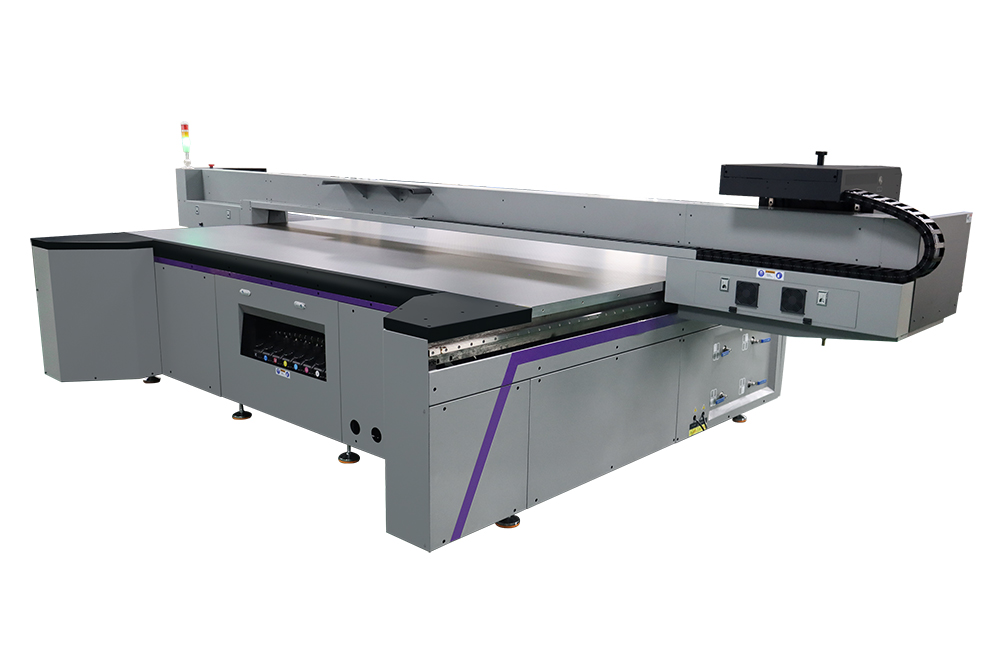
Understanding UV Curing
UV curing is a process that utilizes ultraviolet light to instantly dry or cure inks, adhesives, and other coatings. This technology works on the principle of photochemical reactions, where specific formulations of inks and coatings are designed to react when exposed to UV light. The process involves applying a liquid ink or coating to a substrate and then exposing it to UV radiation, typically in the range of 200 to 400 nanometers. This exposure triggers a chemical reaction that causes the ink or coating to solidify or cure almost immediately.
Flatbed Printing: A Versatile Platform
Flatbed printers are known for their ability to print on a wide range of substrates, including rigid materials like acrylic, glass, metal, wood, and various types of plastics. This versatility makes flatbed printing ideal for applications in signage, packaging, artistic reproductions, and more. Traditional printing methods often require lengthy drying times or the use of heat to cure inks, which can limit the types of materials that can be printed on and the overall efficiency of the process.
The Advantages of UV Curing in Flatbed Printing
1. Instant Curing
One of the most significant advantages of UV curing is its ability to provide instant drying and curing of inks. Unlike solvent-based or water-based inks that require time to air dry or need to be heat-cured, UV-curable inks solidify almost instantly upon exposure to UV light. This rapid curing time allows for faster turnaround times, increased productivity, and the ability to handle a higher volume of prints in a shorter period.
Moreover, instant curing eliminates the need for additional drying equipment or space, reducing both the footprint of the printing operation and its operational costs. The immediate curing also means that prints can be handled, stacked, or further processed immediately after printing, streamlining the entire workflow.
2. Enhanced Print Quality
UV-curable inks offer superior color saturation and vibrancy compared to traditional inks. The chemical reaction that occurs during UV curing results in a more uniform and durable ink film. This leads to prints that have a glossier finish, sharper details, and more consistent color reproduction. For applications where image quality is paramount, such as high-end packaging or fine art reproductions, UV curing can provide a significant competitive advantage.
Furthermore, UV inks are less prone to bleeding or smudging, ensuring clean lines and edges even on intricate designs. This precision is especially important in flatbed printing, where the ability to print on a variety of textures and surfaces requires a high level of control over the ink’s behavior.
3. Versatility in Substrate Compatibility
UV-curable inks are compatible with a wide range of substrates, making flatbed printing even more versatile. Traditional inks might require specific treatments or primers to adhere properly to certain materials, especially non-absorbent ones like metals or plastics. UV inks, however, can be formulated to adhere directly to these substrates without the need for additional preparations.
This compatibility extends the range of applications for flatbed printing, allowing printers to explore new markets and offer unique printing services. From printing directly onto electronic components to creating durable signage for outdoor use, UV curing opens up a world of possibilities.
4. Environmental Benefits
UV curing is a more environmentally friendly process compared to traditional printing methods. Solvent-based inks emit volatile organic compounds (VOCs) that can contribute to air pollution and require special handling and disposal. Water-based inks, while more environmentally benign, still require significant energy for drying.
In contrast, UV-curable inks contain fewer harmful solvents and do not require heat for curing, reducing energy consumption and emissions. Additionally, the instant curing process minimizes waste, as there is no need for overspray or runoff control measures. The reduced environmental impact of UV curing aligns well with the growing trend towards sustainable manufacturing practices.
5. Durability and Resistance
Prints produced with UV-curable inks are known for their durability and resistance to environmental factors. The chemical bonds formed during UV curing create a hard, protective layer on the substrate’s surface. This layer is resistant to fading, scratching, and chemical degradation, ensuring that the prints maintain their quality over time.
For outdoor applications, such as signage or vehicle wraps, this durability is crucial. UV-cured prints can withstand exposure to sunlight, rain, and extreme temperatures without significant deterioration. This longevity reduces the need for frequent replacements, lowering overall costs and environmental impact.
6. Cost Efficiency
While the initial investment in UV curing equipment and inks might be higher than traditional setups, the long-term cost savings can be substantial. The increased productivity and reduced waste associated with UV curing quickly offset the initial outlay. The elimination of drying time and the associated equipment also contributes to lower operational costs.
Furthermore, the durability of UV-cured prints reduces the need for frequent reprints or repairs, saving on both materials and labor. For businesses that rely heavily on print quality and longevity, the cost efficiency of UV curing becomes even more apparent.
7. Flexibility in Design and Customization
UV curing allows for greater flexibility in design and customization. The ability to print on a wide range of substrates and achieve high-quality results means that printers can cater to more diverse customer needs. Whether it’s creating unique packaging designs, personalized signage, or custom artistic pieces, UV curing provides the versatility to bring creative visions to life.
Moreover, the precise control over ink deposition and curing enables printers to experiment with new techniques and effects, such as textured finishes or variable data printing. This flexibility enhances the creative potential of flatbed printing and opens up new avenues for innovation.
The advantages of UV curing in flatbed printing processes are manifold, ranging from instant curing and enhanced print quality to environmental benefits and cost efficiency. This technology not only improves the efficiency and versatility of flatbed printing but also aligns with the industry’s trends towards sustainability and innovation. As digital printing continues to evolve, UV curing will undoubtedly play a pivotal role in shaping its future, offering printers the tools they need to meet the growing demands of the market and deliver exceptional results.
In summary, UV curing represents a significant advancement in flatbed printing, providing a multitude of benefits that enhance the overall printing experience. From its ability to cure inks instantly and produce high-quality prints to its environmental friendliness and cost efficiency, UV curing is a technology that is here to stay. As printers continue to explore new ways to improve their operations and satisfy customer demands, UV curing will undoubtedly be at the forefront of these efforts, driving the industry towards a brighter and more innovative future.