The Role of Color Management in UV Flatbed Printing Quality Control
In the realm of digital printing, UV flatbed printing has emerged as a versatile and efficient technology, capable of producing high-quality prints on a wide range of substrates. From rigid materials like glass and metal to flexible media such as vinyl and fabric, UV flatbed printers have revolutionized the printing industry by offering unparalleled flexibility and durability. However, achieving consistent and accurate color reproduction across diverse materials and print jobs is a complex task that necessitates a robust color management system. This article delves into the intricacies of color management in UV flatbed printing, highlighting its significance in quality control and exploring the strategies employed to ensure optimal color output.
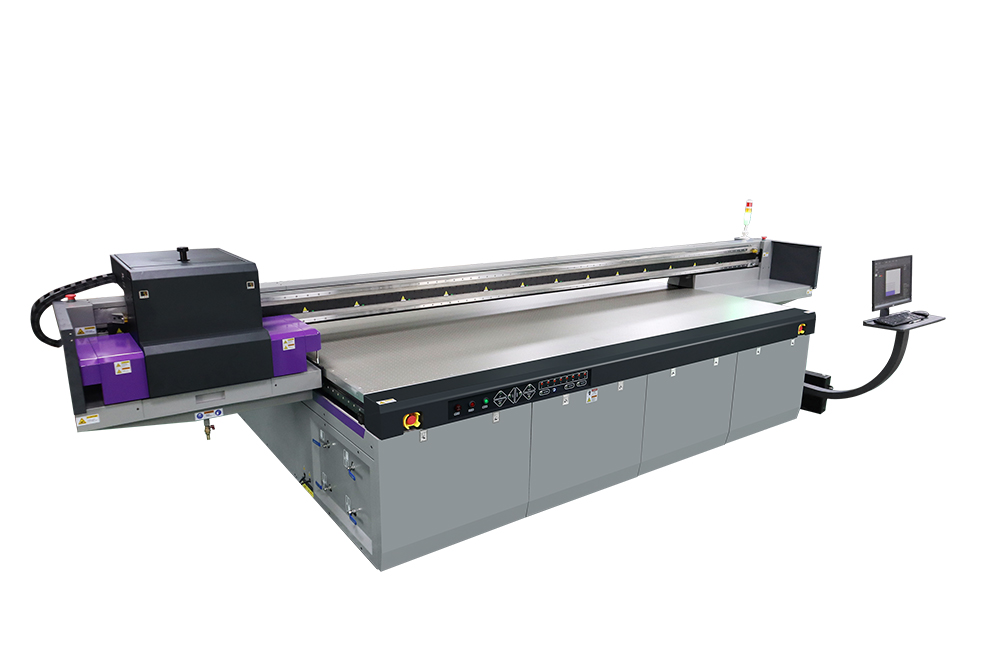
Understanding Color Management
Color management is a systematic approach to controlling and coordinating colors throughout the entire printing process. It involves the use of software, hardware, and standardized procedures to ensure that the colors displayed on a computer screen closely match those printed on the final product. In UV flatbed printing, where the ink is cured instantly by ultraviolet light, color management becomes even more critical due to the unique properties of UV inks and the variety of substrates used.
The Importance of Color Consistency
Consistency in color reproduction is paramount for several reasons. Firstly, it ensures brand integrity. For businesses, maintaining a consistent color palette across all marketing materials is essential for brand recognition and customer trust. Inconsistencies can lead to confusion and a lack of professionalism, undermining the brand’s image.
Secondly, color accuracy is crucial for legal and regulatory compliance. In sectors such as healthcare, where packaging and labeling must adhere to strict guidelines, any deviation in color can have serious consequences. Similarly, in the art world, accurate color reproduction is vital for preserving the artist’s intent and maintaining the value of the artwork.
Lastly, color consistency is a key factor in customer satisfaction. Whether it’s a small business owner ordering promotional materials or a large-scale manufacturer producing product packaging, customers expect high-quality prints that reflect their vision. Inconsistencies in color can lead to dissatisfaction and even lost business.
Components of Color Management in UV Flatbed Printing
Effective color management in UV flatbed printing involves several key components, each playing a crucial role in ensuring optimal color output:
Color Profiles: Color profiles, also known as ICC profiles (International Color Consortium), are mathematical descriptions of how a particular device, such as a printer or monitor, reproduces colors. They translate color data from one device’s color space to another, ensuring that colors remain consistent across different devices. In UV flatbed printing, specific profiles are created for different substrates and ink sets, accounting for variations in ink absorption, reflection, and curing characteristics.
Calibration: Calibration is the process of adjusting a device to ensure it performs within specified parameters. For UV flatbed printers, this includes calibrating the print heads, inks, and curing lamps to ensure consistent ink deposition and cure. Regular calibration helps maintain print quality and color accuracy over time.
Color Measurement: Accurate color measurement is essential for verifying the color accuracy of prints. Spectrophotometers and colorimeters are used to measure the color of printed samples and compare them to standard values. This data is then used to adjust the color profiles and improve print quality.
Workflow Management: Efficient workflow management ensures that color data is correctly managed and communicated throughout the printing process. This includes using color-managed software that supports ICC profiles, as well as implementing standardized procedures for file preparation, proofing, and production.
Operator Training: Skilled operators are the backbone of any successful printing operation. Proper training on color management principles, equipment operation, and troubleshooting ensures that operators can consistently produce high-quality prints.
Strategies for Optimizing Color Management
To further enhance color management in UV flatbed printing, several strategies can be employed:
Use of Standardized Test Charts: Printing standardized test charts, such as those provided by ISO or FOGRA, helps assess the printer’s color reproduction capabilities. By comparing the printed charts to reference values, adjustments can be made to improve color accuracy.
Regular Maintenance: Regular maintenance of the UV flatbed printer, including cleaning the print heads, replacing worn parts, and updating software, is crucial for maintaining optimal performance and color accuracy.
Ink Management: UV inks can vary in composition and performance. Using high-quality inks and adhering to the manufacturer’s recommendations for storage, handling, and mixing ensures consistent ink properties and color output.
Substrate Selection: Different substrates have varying properties that can affect ink absorption, reflection, and cure. Choosing substrates that are compatible with the UV inks and printing process, and testing them for color accuracy, helps ensure consistent results.
Color Management Software: Investing in advanced color management software that offers features such as automated profiling, color correction, and spot color matching can significantly improve color accuracy and reduce the need for manual adjustments.
Collaboration with Suppliers: Working closely with ink and substrate suppliers can provide valuable insights into the best practices for achieving optimal color reproduction. Suppliers often have extensive knowledge of their products and can offer recommendations for improving print quality.
Case Study: Implementing Color Management in a UV Flatbed Printing Operation
To illustrate the importance of color management in UV flatbed printing, consider the case of a large-format printing company that specializes in producing outdoor signage and display graphics. The company recently invested in a state-of-the-art UV flatbed printer to expand its service offerings. However, it soon encountered issues with color consistency, particularly when printing on different substrates.
To address these challenges, the company implemented a comprehensive color management system. It began by calibrating the printer and creating custom ICC profiles for each substrate and ink set. It also invested in advanced color management software that allowed for automated profiling and color correction.
Operators were trained on the new system and procedures, and regular maintenance schedules were established to ensure consistent printer performance. The company also worked closely with its ink and substrate suppliers to optimize ink selection and substrate compatibility.
The results were impressive. Color consistency improved significantly, and customer satisfaction rose as clients praised the high quality and accuracy of the prints. The company’s reputation in the industry grew, leading to increased business and new opportunities.
Color management is a critical component of UV flatbed printing quality control. By understanding the intricacies of color reproduction and implementing a robust color management system, printing companies can ensure consistent and accurate color output across diverse materials and print jobs. This not only enhances brand integrity and customer satisfaction but also helps maintain legal and regulatory compliance and reduces the risk of costly reprints and waste.
Investing in the right tools, training, and procedures is essential for achieving optimal color management in UV flatbed printing. By working closely with suppliers, leveraging advanced technology, and adhering to standardized practices, printing companies can elevate their print quality and stand out in a competitive market.