The Role of Pre-Press Processes in UV Flatbed Printing Quality Control
In the realm of digital printing, UV flatbed printing stands out for its versatility, precision, and ability to print on a wide range of substrates. This technology has revolutionized the printing industry, especially for applications requiring durability, vibrant colors, and detailed graphics. However, achieving optimal print quality in UV flatbed printing is not solely dependent on the printing process itself; it begins much earlier in the workflow—during the pre-press stages. Pre-press processes are critical in ensuring that the final print meets the highest standards of quality, color accuracy, and overall appearance. This article delves into the intricacies of pre-press procedures and their indispensable role in UV flatbed printing quality control.
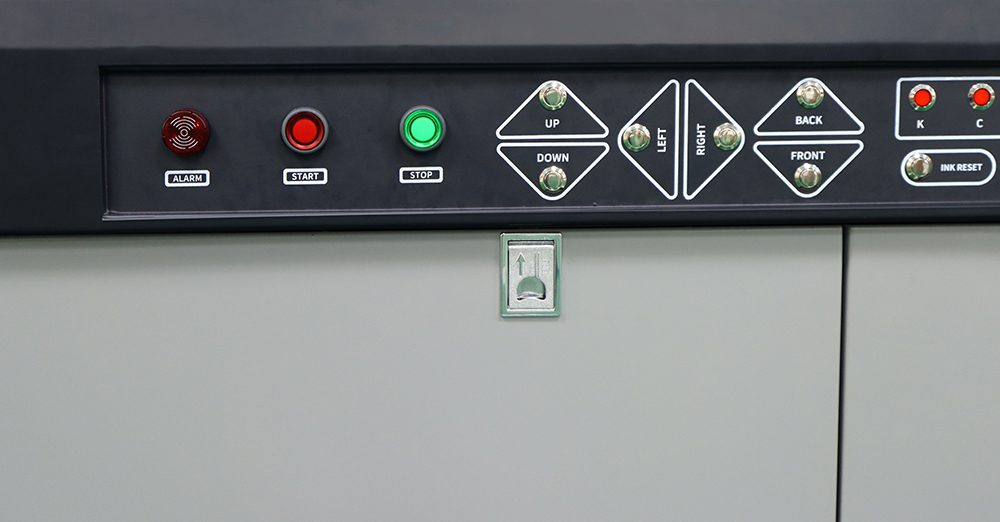
Understanding Pre-Press Processes
Pre-press processes encompass all the activities that occur before the actual printing begins. These processes involve preparing digital files, optimizing images, proofing, and ensuring that the printer settings are correctly configured. The primary goal of pre-press is to minimize errors, avoid costly reprints, and ensure that the print output matches the client’s expectations.
1. File Preparation and Optimization
The first step in pre-press is file preparation. This involves receiving the design files from the client, often in formats such as Adobe Illustrator, Photoshop, or PDF. It is crucial to check that these files are compatible with the printing software and equipment. Issues such as incompatible file formats, low-resolution images, or missing fonts can lead to printing errors or suboptimal print quality.
Image Resolution: High-resolution images are essential for crisp, clear prints. Images should have a resolution of at least 300 dpi (dots per inch) for optimal results in UV flatbed printing. Lower resolution images may appear pixelated or blurry.
Color Mode: Files should be in CMYK color mode, as UV flatbed printers typically use this four-color process. RGB files need to be converted to CMYK, as RGB colors may not translate accurately to the printed output.
Bleeds and Margins: Ensuring that there are proper bleeds (areas where the image extends beyond the trim edge) and margins (spaces around the design to avoid cutting into important elements) is crucial. This prevents any unprinted edges or white spaces from appearing in the final product.
2. Proofing and Color Matching
Proofing is a fundamental step in pre-press that involves creating a physical or digital sample of the final print. This proof allows for a visual inspection to ensure that colors, layout, and overall design meet the desired standards.
Digital Proofs: Digital proofs provide a quick and cost-effective way to preview the print. However, they may not always accurately represent the final printed colors, especially when viewed on different screens or under varying lighting conditions.
Hard Proofs: Hard proofs, or physical prints, offer a more accurate representation of the final product. They are printed on the same substrate and with similar ink settings as the final print run. This enables a more precise assessment of color accuracy, ink coverage, and overall print quality.
Color matching is critical, particularly for brands with strict color guidelines. Using color management tools like ICC profiles ensures that colors remain consistent across different devices and media. Regular calibration of monitors and printers is also essential to maintain color accuracy throughout the production process.
3. Printer Settings and Calibration
The configuration of printer settings is another vital aspect of pre-press. UV flatbed printers offer a myriad of adjustable settings, including ink density, print speed, and curing parameters. These settings need to be fine-tuned based on the specific job requirements, substrate type, and desired print quality.
Ink Density: Adjusting ink density affects the richness and saturation of colors. Too much ink can lead to smudging or over-saturation, while too little can result in washed-out colors.
Print Speed: While faster print speeds are desirable for increased productivity, they can sometimes compromise print quality. Slower speeds allow for better ink adhesion and more controlled curing.
Curing Parameters: UV flatbed printers use UV light to cure the inks instantly. The intensity and duration of the UV exposure need to be carefully set. Over-exposure can cause the substrate to warp or discolor, while under-exposure may result in inks not fully curing, leading to smudging or poor durability.
Regular calibration of the printer ensures that these settings remain accurate, minimizing variations in print quality across different print runs.
4. Substrate Preparation
The choice and preparation of the substrate significantly impact the final print quality. UV flatbed printers can print on a variety of materials, from rigid substrates like acrylic and metal to flexible ones like vinyl and fabric.
Substrate Compatibility: Ensuring that the substrate is compatible with UV inks is crucial. Some materials may require special treatments or coatings to enhance ink adhesion and durability.
Cleaning and Preparation: Substrates should be clean, dry, and free of any contaminants that could affect ink adhesion. For example, dust or oils on the surface can cause ink to scatter, resulting in a blotchy or uneven print.
Handling and Storage: Proper handling and storage of substrates before printing can prevent issues like static, which can attract dust and debris, or moisture, which can affect ink drying and curing.
5. Quality Control Checks
Throughout the pre-press stages, regular quality control checks are essential. These checks help identify and rectify potential issues before they become costly problems.
Visual Inspections: Regular visual inspections of proofs, substrates, and printer settings can catch issues early. This includes checking for color accuracy, image clarity, and proper alignment.
Automated Tools: Using automated quality control tools, such as color measurement devices and print inspection software, can provide more objective and consistent evaluations. These tools can detect subtle color variations or print defects that might be missed by visual inspections.
Feedback Loops: Establishing feedback loops with clients and within the production team ensures that any issues or concerns are addressed promptly. This fosters a culture of continuous improvement and helps maintain high standards of print quality.
Pre-press processes are the unsung heroes of UV flatbed printing quality control. From file preparation and optimization to proofing, printer settings configuration, substrate preparation, and quality control checks, each step plays a crucial role in ensuring that the final print meets or exceeds expectations. By investing time and resources into these processes, printing businesses can minimize errors, reduce waste, and deliver high-quality prints that satisfy their clients.
UV flatbed printing technology continues to evolve, offering new possibilities for creativity and innovation. However, the fundamentals of pre-press remain constant. They serve as the foundation upon which exceptional print quality is built, enabling businesses to harness the full potential of UV flatbed printing and stay ahead in a competitive market.