The Role of Substrates in UV Flatbed Printing Quality
The Role of Substrates in UV Flatbed Printing Quality
UV flatbed printing has emerged as a revolutionary technology in the digital printing industry, offering unparalleled versatility and high-quality output across a wide range of substrate materials. The success of UV flatbed printing is largely attributed to its ability to print on various substrates, from traditional paper and plastics to unconventional materials such as glass, wood, metal, and ceramics. In this article, we will explore the role of substrates in UV flatbed printing quality, examining how the choice of substrate impacts the final print output.
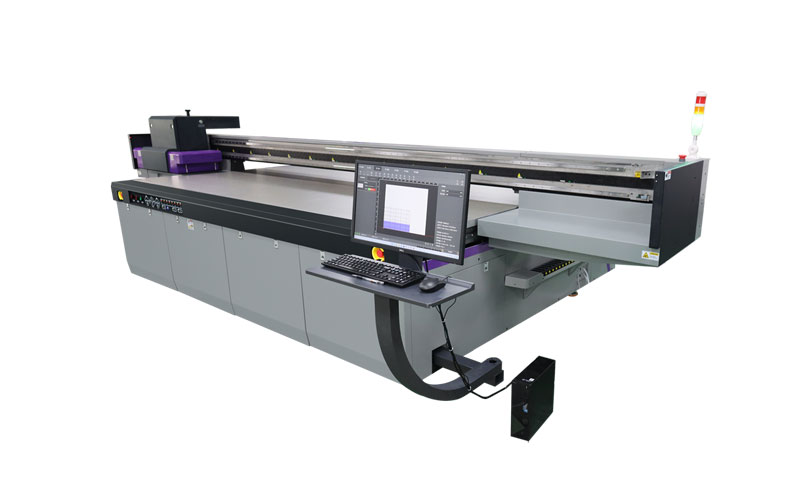
Introduction to UV Flatbed Printing
UV flatbed printing is a digital printing technique that utilizes UV-curable inks and digital printing technology to produce high-quality prints on a variety of materials. The UV inks are cured using ultraviolet light, which enables instant drying and allows for the printing of materials that cannot withstand the heat of traditional inkjet printing.
UV flatbed printers have several key advantages:
Versatility: UV flatbed printers can print on a wide range of substrate materials, including glass, wood, metal, plastics, and ceramics.
High Quality: UV inks offer vibrant, long-lasting images with excellent color reproduction and durability.
Efficiency: UV curing enables instant drying, which reduces production time and increases efficiency.
The Role of Substrates in UV Flatbed Printing Quality
The substrate is the material onto which the UV ink is printed. The choice of substrate significantly impacts the final print output in terms of quality, appearance, and durability. Here, we will explore the role of substrates in UV flatbed printing quality, examining factors such as substrate type, surface texture, ink absorption, and curing efficiency.
Substrate Type
UV flatbed printing can be applied to a wide range of substrate materials, each with its own unique properties that affect the print quality. Common substrate materials include:
Paper and Cardboard: Traditional printing substrates, offering good ink absorption and a range of finishes.
Plastics: Versatile materials with varying degrees of flexibility and rigidity, suitable for a wide range of applications.
Wood: Natural material offering a warm, tactile finish, but requiring careful surface preparation to achieve optimal print quality.
Metal: Durable and reflective materials, suitable for high-end applications such as signage and decorative elements.
Glass and Ceramics: Non-porous materials that require specific ink formulations and surface treatment to achieve good adhesion.
Surface Texture
The surface texture of the substrate plays a crucial role in UV flatbed printing quality. A smooth, even surface ensures uniform ink application and consistent print quality. Conversely, textured or uneven surfaces can lead to ink pooling, streaking, and other print defects.
For example, printing on rough wood surfaces requires careful surface preparation to achieve a smooth, printable surface. This may involve sanding, priming, or applying a coating to fill in the pores and create an even surface.
Ink Absorption
The ink absorption of the substrate is another important factor in UV flatbed printing quality. Highly absorbent substrates, such as uncoated paper, require inks with good wettability to ensure even ink distribution. Non-absorbent or low-absorbent substrates, such as plastics and glass, require inks formulated to adhere to the surface without soaking in.
Inks formulated for non-absorbent substrates often contain additives to improve adhesion and durability. These additives can affect the viscosity, cure speed, and color of the ink, which must be carefully balanced to achieve optimal print quality.
Curing Efficiency
UV curing is a critical step in UV flatbed printing, as it ensures that the ink is dried and fixed to the substrate. The curing efficiency is influenced by several factors, including the UV light intensity, the ink formulation, and the substrate material.
Different substrate materials have varying degrees of UV light transmission and absorption. For example, transparent materials such as glass and plastics allow UV light to pass through, while opaque materials block it. This can affect the curing speed and depth of cure, which must be carefully managed to achieve optimal print quality.
Substrate Preparation and Handling
To achieve optimal print quality with UV flatbed printing, it is essential to properly prepare and handle the substrate material. Here are some key considerations:
Surface Cleaning
Before printing, the substrate surface should be cleaned to remove any dirt, grease, or contaminants that could affect ink adhesion. This may involve using solvents, detergents, or abrasives, depending on the substrate material.
Surface Treatment
Some substrate materials may require specific surface treatments to improve ink adhesion. For example, plastics and metals often require priming or coating to create a printable surface. Glass and ceramics may require etching or sandblasting to increase surface roughness and improve adhesion.
Handling and Storage
Substrates should be handled with care to avoid scratches, dents, or other damage that could affect print quality. They should be stored in a clean, dry environment to prevent contamination and warping.
Case Studies and Applications
To further illustrate the role of substrates in UV flatbed printing quality, let’s examine a few case studies and applications:
Case Study 1: Glass Printing
UV flatbed printing is widely used in the glass industry for applications such as window decorations, mirrors, and architectural elements. The smooth, non-porous surface of glass requires specific ink formulations and surface treatment to achieve good adhesion.
In one case study, a UV flatbed printer was used to print vibrant, full-color images on glass panels for a high-end retail store. The glass panels were first cleaned and coated with a primer to improve ink adhesion. The printer then applied UV-curable inks, which were cured using UV light to create a durable, scratch-resistant finish.
Case Study 2: Wood Printing
UV flatbed printing is also popular in the woodworking industry for applications such as furniture, decorative panels, and signage. The natural texture and grain of wood require careful surface preparation to achieve optimal print quality.
In one case study, a UV flatbed printer was used to print custom designs on wooden panels for a luxury home renovation project. The wooden panels were first sanded and coated with a primer to create a smooth, printable surface. The printer then applied UV-curable inks, which were cured using UV light to create a durable, high-quality finish.
Case Study 3: Metal Printing
UV flatbed printing is increasingly being used in the metalworking industry for applications such as signage, decorative elements, and industrial components. The durable and reflective surface of metal requires specific ink formulations and surface treatment to achieve good adhesion.
In one case study, a UV flatbed printer was used to print custom logos and graphics on metal panels for a corporate event. The metal panels were first cleaned and coated with a primer to improve ink adhesion. The printer then applied UV-curable inks, which were cured using UV light to create a durable, scratch-resistant finish.
Conclusion
UV flatbed printing is a versatile and high-quality digital printing technology that can be applied to a wide range of substrate materials. The choice of substrate significantly impacts the final print output in terms of quality, appearance, and durability. By carefully selecting and preparing the substrate material, print professionals can achieve optimal print quality with UV flatbed printing.
As the digital printing industry continues to evolve, UV flatbed printing will likely play an increasingly important role in a wide range of applications. By understanding the role of substrates in UV flatbed printing quality, print professionals can harness the full potential of this revolutionary technology to create stunning, high-quality prints on a variety of materials.