The Science Behind UV-Curing Technology in Printing
The Science Behind UV-Curing Technology in Printing
In the realm of modern printing, the pursuit of efficiency, precision, and durability has driven the industry towards innovative solutions that transcend traditional methods. One such advancement is UV-curing technology, a process that has revolutionized the way inks and coatings are dried and cured on various substrates. This technology leverages the power of ultraviolet (UV) light to initiate a chemical reaction that rapidly solidifies inks and coatings, offering numerous advantages over conventional drying techniques. In this exploration, we delve into the science behind UV-curing technology, examining its principles, applications, benefits, and the intricate processes that make it a cornerstone of contemporary printing practices.
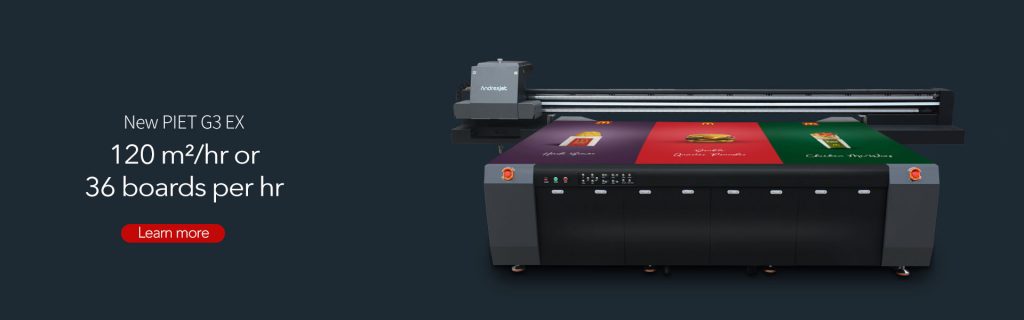
The Fundamentals of UV-Curing
UV-curing technology is rooted in the principles of photochemistry, where specific wavelengths of ultraviolet light interact with chemical compounds to trigger polymerization reactions. At its core, this technology employs UV-curable inks and coatings that contain photoinitiators—chemicals sensitive to UV light. When exposed to UV radiation, these photoinitiators absorb the energy and undergo a molecular transformation, generating reactive species such as free radicals or ions.
These highly reactive species then act as catalysts, initiating a chain reaction that causes the polymer molecules within the ink or coating to cross-link and form a solid network. This process, known as polymerization, occurs rapidly, often within seconds or fractions of a second, resulting in an instant cure. The speed and efficiency of UV-curing are significant advantages, particularly in high-volume printing operations where time is a critical factor.
The UV-Curing Process
The UV-curing process can be broken down into several key stages:
Application: UV-curable inks or coatings are applied to the substrate using various printing techniques such as offset, flexography, screen printing, or digital printing.
Exposure to UV Light: The printed material is then exposed to UV light, typically in the range of 200 to 400 nanometers (nm), emitted by UV lamps. These lamps can be mercury vapor, metal halide, or more recently, LED-based systems. The choice of lamp depends on factors such as the type of ink, desired cure speed, and substrate compatibility.
Initiation and Polymerization: Upon absorption of UV light, the photoinitiators in the ink or coating are activated, leading to the formation of reactive species that initiate the polymerization process. As the polymer chains cross-link, the material transitions from a liquid or viscous state to a solid, fully cured state.
Post-Cure (Optional): In some cases, a post-cure step may be necessary to ensure complete polymerization and optimize the final properties of the print. This involves exposing the cured material to additional UV light or heat to further strengthen the polymer network.
Benefits of UV-Curing Technology
The adoption of UV-curing technology in printing has been driven by its myriad benefits, which include:
Rapid Curing: The primary advantage of UV-curing is its speed. The almost instantaneous curing process significantly reduces production times compared to traditional air-drying or thermal-curing methods.
Enhanced Durability: UV-cured inks and coatings exhibit superior resistance to abrasion, chemicals, and environmental factors such as UV radiation and moisture. This results in prints that are more durable and long-lasting.
Energy Efficiency: UV-curing is a more energy-efficient process than thermal curing, as it directly targets the ink or coating with UV light, minimizing heat loss and reducing overall energy consumption.
Environmental Friendliness: UV-curable products often contain fewer volatile organic compounds (VOCs) than solvent-based alternatives, contributing to reduced environmental impact and improved workplace safety.
Versatility: UV-curing technology can be applied to a wide range of substrates, including paper, plastics, metals, and glass, making it suitable for diverse printing applications.
Improved Print Quality: The rapid curing process reduces the risk of ink bleeding or smearing, leading to sharper images and more precise prints.
Applications of UV-Curing in Printing
The versatility and advantages of UV-curing technology make it ideal for various printing applications across different industries:
Graphic Arts: UV-curing is widely used in the production of posters, banners, and other large-format graphics, where fast turnaround times and durable prints are essential.
Packaging: In the packaging industry, UV-cured inks and coatings provide a high level of resistance to scuffing, abrasion, and chemicals, ensuring that product packaging remains attractive and protective throughout its lifecycle.
Labels and Tags: UV-curing enables the production of durable labels and tags that can withstand harsh environments, such as those found in outdoor or industrial settings.
Functional Printing: In areas such as electronics and sensor technology, UV-curing is used to create conductive inks and coatings that require precise curing to achieve desired electrical properties.
3D Printing: UV-curing also plays a role in 3D printing, particularly in stereolithography (SLA) processes where liquid resin is cured layer by layer using a UV laser.
Challenges and Considerations
Despite its many benefits, UV-curing technology is not without its challenges. Some considerations include:
Equipment Costs: The initial investment in UV-curing equipment can be higher than that for traditional drying systems. However, the long-term benefits in efficiency and cost savings often justify this expenditure.
Health and Safety: While UV-curable products generally have lower VOC emissions, the use of UV lamps requires proper handling and safety measures to protect workers from potential exposure to UV radiation.
Substrate Compatibility: Not all substrates are compatible with UV-curing. Some materials may absorb UV light, causing unwanted changes in color or properties. It is crucial to test substrates for compatibility before full-scale production.
Curing Uniformity: Ensuring uniform exposure to UV light across the entire print area can be challenging, particularly for complex shapes or large formats. Advances in UV lamp design and control systems are continuously addressing this issue.
Future Trends
As UV-curing technology continues to evolve, several trends are emerging that will further shape its application in printing:
LED-Based UV Systems: LED technology is increasingly being adopted for UV-curing due to its energy efficiency, longer lifespan, and ability to provide more targeted and consistent UV output.
Smart Curing Systems: The integration of sensors and control systems is enabling more precise and adaptive curing processes, optimizing cure speed and quality based on real-time feedback.
Bio-Based Inks and Coatings: The development of bio-based UV-curable materials is addressing environmental concerns, offering sustainable alternatives to petroleum-based products.
Expanded Applications: As the technology matures, new applications in areas such as textile printing, printable electronics, and personalized medicine are being explored, pushing the boundaries of what UV-curing can achieve.
In conclusion, UV-curing technology stands as a pillar of innovation in the printing industry, offering a blend of speed, efficiency, and durability that aligns with the demands of modern manufacturing. By harnessing the power of ultraviolet light, this technology not only enhances the quality and performance of prints but also contributes to a more sustainable and efficient production process. As research and development continue to advance, UV-curing will undoubtedly unlock new possibilities and further solidify its role in the future of printing.