Troubleshooting Common Software Issues in UV Flatbed Printers
UV flatbed printers have revolutionized the printing industry, offering high-quality, durable prints on a wide range of materials. These printers utilize ultraviolet (UV) light to cure inks instantly, resulting in vibrant, scratch-resistant, and water-resistant prints. However, like any sophisticated piece of equipment, UV flatbed printers can encounter software-related issues that may disrupt their operation. This article aims to provide a comprehensive guide to troubleshooting some of the most common software problems encountered in UV flatbed printers, ensuring smooth and efficient printing processes.
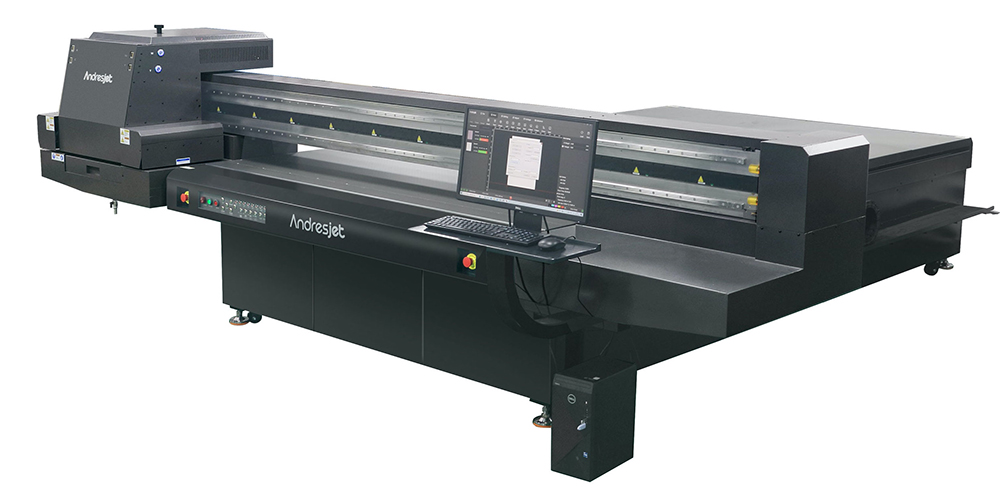
1. Printer Not Responding
One of the most frustrating issues is when the printer fails to respond to commands from the computer. This can stem from several factors:
USB Connection Issues: Ensure that the USB cable connecting the printer to the computer is securely plugged in at both ends. Try using a different USB port on the computer or a different USB cable to rule out any physical defects.
Driver Problems: Outdated or corrupted printer drivers can cause communication failures. Visit the printer manufacturer’s website to download and install the latest drivers. Always uninstall the old drivers before installing the new ones to avoid conflicts.
Firewall or Antivirus Interference: Sometimes, security software can block communication between the printer and the computer. Temporarily disable the firewall or antivirus software to see if it resolves the issue. Remember to re-enable them after troubleshooting.
Print Spooler Service: The print spooler service manages print jobs and can sometimes stop working. On Windows, you can restart the service by going to ‘Services’ (type services.msc in the Run dialog), finding ‘Print Spooler’, right-clicking it, and selecting ‘Restart’.
2. Print Quality Problems
Poor print quality can manifest as banding, streaking, or faded colors. Addressing these issues often involves calibrating the printer and checking the ink system:
Nozzle Check: Run a nozzle check to ensure all ink nozzles are firing correctly. If some nozzles are clogged, perform a cleaning cycle. Be cautious with frequent cleanings, as they can consume a significant amount of ink and potentially damage the print head if overused.
Calibration: Improper calibration can lead to misaligned prints. Follow the printer’s manual for calibrating the print head and media feed. This process ensures that the ink is deposited accurately on the media.
Ink Levels and Quality: Low ink levels or using non-genuine ink can affect print quality. Check ink levels and replace cartridges if necessary. Always use ink recommended by the printer manufacturer to maintain optimal performance.
RIP Software Settings: Raster Image Processor (RIP) software settings can impact print quality. Ensure that the resolution, color profiles, and pass settings are appropriately configured for the type of media and desired print quality.
3. Software Crashes or Freezes
Software crashes or freezes can halt the printing process and are often related to software conflicts or resource limitations:
Update Software: Ensure that both the printer’s firmware and the RIP software are up to date. Manufacturers regularly release updates to fix bugs and improve compatibility.
System Resources: Check your computer’s system resources. Running too many applications simultaneously can overwhelm the system, causing the printer software to crash. Close unnecessary programs and restart your computer before attempting to print again.
Compatibility Issues: Verify that the RIP software is compatible with your operating system. Sometimes, newer operating systems may not fully support older software versions. Consider running the software in compatibility mode if available.
Corrupted Files: A corrupted print file can cause the software to freeze or crash. Re-export the file from your design software, ensuring it’s in a compatible format and free of errors.
4. Job Stuck in Print Queue
A print job getting stuck in the print queue can be a major annoyance. Here’s how to resolve it:
Clear Print Queue: Access the print queue through the printer settings in your operating system. Cancel all stuck jobs and try printing again. On Windows, you can do this by opening ‘Devices and Printers’, right-clicking the printer, and selecting ‘See what’s printing’. From there, you can cancel all jobs.
Restart Printer and Computer: Sometimes, simply restarting both the printer and the computer can clear out stuck print jobs and reset the communication between devices.
Print Directly from Software: If the issue persists, try printing directly from the design or RIP software instead of using a generic print dialog. This can bypass some of the operating system’s print handling and may resolve the issue.
5. Network Printing Issues
For network-connected UV flatbed printers, issues can arise from network configurations:
Network Connection: Ensure the printer is properly connected to the network. Check the network cable or Wi-Fi connection, and verify that the printer’s IP address is correctly assigned and accessible.
Printer Sharing: If the printer is shared on a network, ensure that the sharing settings are correctly configured on the host computer. Also, verify that other network users have the necessary permissions to access the printer.
Firewall Settings: Network firewalls can block printer communication. Ensure that the necessary ports are open, or temporarily disable the firewall on the host computer to test if it resolves the issue.
Firmware and Network Settings: Update the printer’s firmware to the latest version, as it may contain improvements to network connectivity. Also, check the printer’s network settings to ensure they match the network configuration (e.g., IP address, subnet mask, gateway).
Conclusion
Troubleshooting software issues in UV flatbed printers can be a meticulous process, but by following a systematic approach, most problems can be resolved efficiently. Regular maintenance, such as updating software and firmware, checking connections, and performing routine calibrations, can prevent many common issues. When problems do arise, understanding the potential causes and having a structured troubleshooting plan can minimize downtime and ensure high-quality printing.
Remember, the key to successful troubleshooting is patience and a methodical approach. By addressing each potential issue step-by-step, you can identify and resolve software problems in UV flatbed printers, keeping your printing operations running smoothly.