Troubleshooting Guide for Banding Issues in UV Flatbed Printing
UV flatbed printing has revolutionized the printing industry with its ability to produce high-quality, vibrant prints on a wide range of substrates. However, like any advanced technology, it is not immune to issues that can affect print quality. One such issue is banding, which refers to visible lines or stripes that appear across the printed image. Banding can detract from the aesthetic appeal of the print and, in severe cases, render it unusable. This comprehensive troubleshooting guide aims to help printers diagnose and resolve banding issues in UV flatbed printing, ensuring consistent, high-quality output.
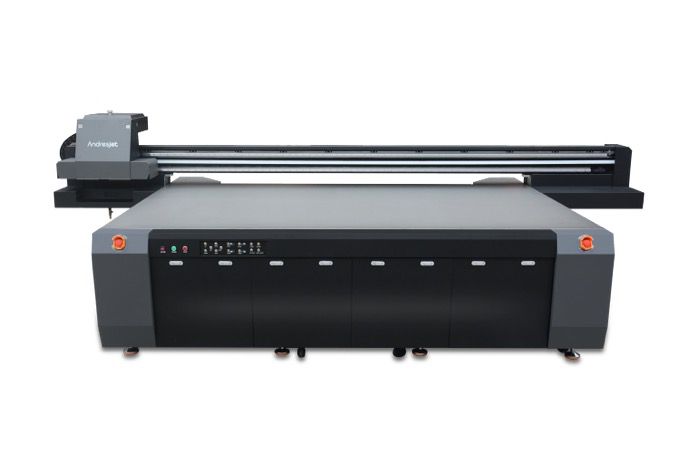
Understanding Banding
Before diving into the solutions, it’s essential to understand the causes of banding. Banding can result from various factors, including mechanical, electronic, and environmental issues. These factors can interact in complex ways, making it crucial to approach troubleshooting systematically.
Mechanical Causes
Print Head Alignment: Misalignment of print heads can lead to uneven ink deposition, causing banding. Regular calibration and alignment checks are crucial.
Media Handling: Incorrect media tension or uneven media feed can create banding. Ensure that the media is securely loaded and that the feed mechanism is functioning smoothly.
Print Bed Issues: An uneven or dirty print bed can affect ink application, leading to banding. Keep the print bed clean and ensure it is level.
Electronic Causes
Inkjet Nozzle Clogs: Clogged or partially blocked nozzles can result in inconsistent ink flow, causing banding. Regular maintenance, such as nozzle cleaning and flushing, is necessary.
Driver and Firmware Issues: Outdated drivers or firmware can cause communication problems between the printer and its components, leading to banding. Keep all software up to date.
Inconsistent Ink Supply: Fluctuations in ink pressure or supply can cause banding. Check the ink delivery system for leaks, blockages, or air bubbles.
Environmental Causes
Temperature and Humidity: Extreme or fluctuating temperatures and humidity levels can affect ink viscosity and drying rates, contributing to banding. Maintain a stable printing environment within the manufacturer’s recommended range.
Airflow: Drafts or uneven airflow in the printing area can disrupt the ink application process, leading to banding. Ensure the printing area is well-ventilated but protected from drafts.
Troubleshooting Steps
With an understanding of the causes, let’s explore the steps to troubleshoot and resolve banding issues.
Step 1: Check Print Head Alignment and Calibration
Perform a Print Head Alignment Test: Most UV flatbed printers have built-in alignment tools. Follow the manufacturer’s instructions to perform an alignment test and adjust as necessary.
Calibrate the Printer: Calibration ensures that the printer’s internal sensors and motors are synchronized. This process may involve adjusting the media feed, print head positioning, and other parameters.
Step 2: Inspect Media Handling
Check Media Tension: Ensure that the media is properly tensioned to avoid movement during printing. Adjust the tension settings as needed.
Examine the Feed Mechanism: Look for any signs of wear, damage, or debris in the media feed path. Clean and lubricate as necessary.
Use Quality Media: Low-quality or incompatible media can contribute to banding. Always use media that is recommended by the printer manufacturer.
Step 3: Maintain the Print Bed
Clean the Print Bed: Use a lint-free cloth and a suitable cleaning solution to remove any dust, debris, or ink residue from the print bed.
Check for Levelness: Use a leveling tool to ensure the print bed is flat and even. Adjust if necessary.
Inspect for Damage: Look for any cracks, scratches, or other damage that could affect print quality. Repair or replace the print bed as needed.
Step 4: Address Nozzle and Ink Issues
Clean the Nozzles: Regularly clean the print heads using the printer’s built-in cleaning cycles. If banding persists, perform a more thorough cleaning using a cleaning solution and soft brush.
Check Ink Levels and Supply: Ensure that all ink cartridges or tanks are properly filled and that there are no leaks or air bubbles in the ink lines.
Replace Old or Damaged Nozzles: If cleaning does not resolve the issue, some nozzles may need to be replaced. Consult the printer’s manual for instructions on nozzle replacement.
Step 5: Update Software and Drivers
Check for Updates: Visit the printer manufacturer’s website to see if there are any updates available for the printer’s firmware, drivers, or software.
Install Updates: Follow the manufacturer’s instructions to install any available updates. This can often resolve compatibility issues or bugs that may be causing banding.
Step 6: Control the Environment
Monitor Temperature and Humidity: Use a hygrometer to monitor the printing environment. Adjust the climate control settings to maintain a stable temperature and humidity level within the recommended range.
Minimize Airflow Disruptions: Ensure that the printing area is protected from drafts and uneven airflow. This may involve closing doors, using curtains, or installing barriers to block drafts.
Use a Humidifier or Dehumidifier: If necessary, use a humidifier or dehumidifier to maintain optimal humidity levels.
Step 7: Optimize Print Settings
Adjust Ink Drop Size: Some printers allow you to adjust the size of the ink drops. Experiment with different settings to find the optimal drop size for your specific application.
Change Print Speed: Slowing down the print speed can sometimes improve ink application and reduce banding.
Use a Higher Resolution: Increasing the print resolution can help to mask minor banding issues by creating a smoother, more uniform appearance.
Step 8: Seek Professional Help
If the above steps do not resolve the banding issue, it may be time to seek professional help. Contact the printer manufacturer’s technical support team or a qualified printer repair service. They can provide more advanced diagnostics and repairs, such as replacing faulty components or adjusting internal settings.
Prevention Tips
To minimize the risk of banding in the future, consider the following prevention tips:
Regular Maintenance: Schedule regular maintenance checks and cleanings to keep the printer in optimal condition.
Use High-Quality Inks and Media: Always use inks and media that are recommended by the printer manufacturer to ensure compatibility and quality.
Monitor Environmental Conditions: Keep a close eye on temperature, humidity, and airflow in the printing area, and make adjustments as needed.
Train Operators: Ensure that all operators are trained in proper printer usage and maintenance to avoid common mistakes that can lead to banding.
By following this comprehensive troubleshooting guide, printers can effectively diagnose and resolve banding issues in UV flatbed printing. With regular maintenance and attention to detail, it’s possible to achieve consistent, high-quality prints that meet the demands of even the most discerning customers.