Troubleshooting Guide for Ink Smearing in UV Flatbed Printing
UV flatbed printing has revolutionized the printing industry with its ability to produce high-quality, vibrant prints on a wide range of substrates. However, like any technology, it is not without its challenges. One common issue that printers may encounter is ink smearing, a phenomenon where the ink spreads or blurs unintentionally during or after the printing process. This guide aims to provide a comprehensive troubleshooting approach to address ink smearing in UV flatbed printing, ensuring optimal print quality and customer satisfaction.
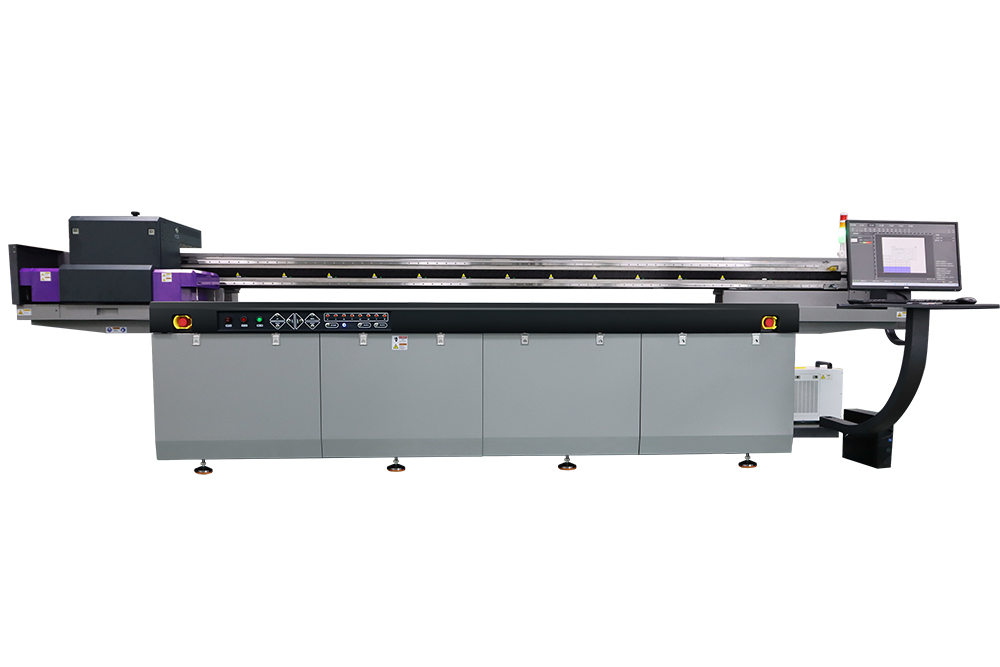
Understanding Ink Smearing
Ink smearing can manifest in various forms, including streaking, blurring, or uneven ink distribution. It often occurs due to a combination of factors related to the printer’s settings, the ink’s properties, the substrate’s characteristics, and the environmental conditions. Identifying the root cause of ink smearing is crucial for implementing an effective solution.
Initial Diagnostics
Before diving into specific troubleshooting steps, conduct an initial diagnostic to gather information about the printing environment and process. This includes:
Reviewing Print Settings: Examine the printer’s settings, such as ink density, print speed, and curing parameters. Incorrect settings can significantly contribute to ink smearing.
Inspecting the Substrate: Evaluate the substrate for its absorbency, texture, and compatibility with UV inks. Some materials may require special pre-treatment or adjustments to the printing process.
Environmental Check: Assess the ambient temperature, humidity, and air circulation in the printing area. Extreme conditions can affect ink behavior and cure quality.
Ink Quality and Handling: Verify that the ink is within its shelf life, properly stored, and mixed according to the manufacturer’s instructions. Old or improperly handled ink can lead to smearing.
Troubleshooting Steps
1. Adjust Printer Settings
Print Speed: Reducing the print speed can help the ink adhere more evenly to the substrate, minimizing the risk of smearing.
Ink Density: Adjust the ink density to ensure that an excessive amount of ink is not being deposited, which could lead to smearing.
Curing Parameters: Optimize the UV curing process by adjusting the lamp intensity and exposure time. Over-curing can cause ink to become tacky, while under-curing can result in ink not setting properly.
2. Substrate Preparation
Cleaning: Ensure the substrate is clean and dust-free before printing. Contaminants can interfere with ink adhesion.
Pre-Treatment: Apply a suitable pre-treatment to enhance ink adhesion, especially for non-absorbent materials like glass or metal.
Testing: Conduct test prints on different substrates to determine which ones are most compatible with your UV ink and printing process.
3. Ink Management
Viscosity Control: Maintain the ink’s viscosity within the recommended range. Too low viscosity can cause the ink to spread excessively, while too high can lead to poor ink flow.
Agitation: Regularly agitate the ink to prevent settling and ensure a consistent ink formulation.
Replacement: Replace old or expired ink with fresh supplies to maintain optimal print quality.
4. Environmental Controls
Temperature and Humidity: Maintain a stable temperature and humidity level in the printing area. Ideal conditions typically range between 20-25°C (68-77°F) and 40-60% relative humidity.
Air Circulation: Ensure adequate air circulation to prevent the accumulation of volatile organic compounds (VOCs) released during the curing process, which can affect ink cure and cause smearing.
5. Print Head Maintenance
Cleaning: Regularly clean the print heads to remove any ink residue or debris that could interfere with ink flow and cause smearing.
Alignment: Ensure the print heads are properly aligned to avoid misregistration and ink overlap, which can lead to smearing.
Nozzle Check: Perform a nozzle check to ensure all nozzles are functioning correctly and not causing uneven ink distribution.
6. Curing System Optimization
Lamp Maintenance: Regularly inspect and replace UV lamps as needed. Aged lamps may not provide consistent curing, leading to ink smearing.
Curing Distance: Adjust the distance between the UV lamps and the substrate to ensure proper cure without over-exposing the ink.
Curing Stages: Implement a multi-stage curing process, if possible, to gradually cure the ink and reduce the risk of smearing.
Advanced Troubleshooting
If the basic troubleshooting steps do not resolve the issue, consider the following advanced strategies:
Ink Formulation: Consult with your ink supplier about formulating a custom ink that better suits your specific substrate and printing conditions.
Print Profile Adjustment: Develop or refine print profiles that take into account the unique characteristics of your printing setup and materials.
Training and Expertise: Invest in training for your operators to ensure they understand the intricacies of UV flatbed printing and can identify and address potential issues promptly.
Consultation: Seek expert advice from a printing consultant or technician who specializes in UV flatbed printing to gain insights into less common causes of ink smearing.
Preventive Measures
To minimize the occurrence of ink smearing in the future, implement the following preventive measures:
Regular Maintenance: Establish a routine maintenance schedule for your printer, including regular cleaning, calibration, and inspection of all components.
Quality Control: Implement a stringent quality control process to monitor print quality and catch potential issues early.
Supplier Communication: Maintain open communication with your ink and substrate suppliers to stay informed about product updates and recommendations.
Documentation: Keep detailed records of your printing processes, including settings, substrate types, and ink batches, to facilitate troubleshooting and ensure consistency.
Ink smearing in UV flatbed printing can be a frustrating and costly issue, but with a systematic approach to troubleshooting, it can be effectively addressed. By understanding the root causes and implementing the appropriate adjustments to printer settings, substrate preparation, ink management, environmental controls, and print head maintenance, you can achieve optimal print quality and minimize downtime. Remember, preventive measures and ongoing quality control are key to maintaining consistent and reliable printing operations. With the right strategies in place, you can overcome the challenge of ink smearing and deliver exceptional prints every time.