Technical Insights: UV Flatbed Printer Calibration Procedures
Technical Insights: UV Flatbed Printer Calibration Procedures.In the realm of digital printing, achieving precision and consistency is paramount. UV flatbed printers, known for their versatility in handling a wide range of substrates and producing high-quality prints, are no exception. These printers utilize ultraviolet light to cure inks instantly, resulting in durable and vibrant prints. However, to ensure optimal performance and output quality, regular calibration of the UV flatbed printer is crucial. This article delves into the intricacies of UV flatbed printer calibration procedures, exploring the steps, tools, and techniques involved in maintaining print accuracy and consistency.
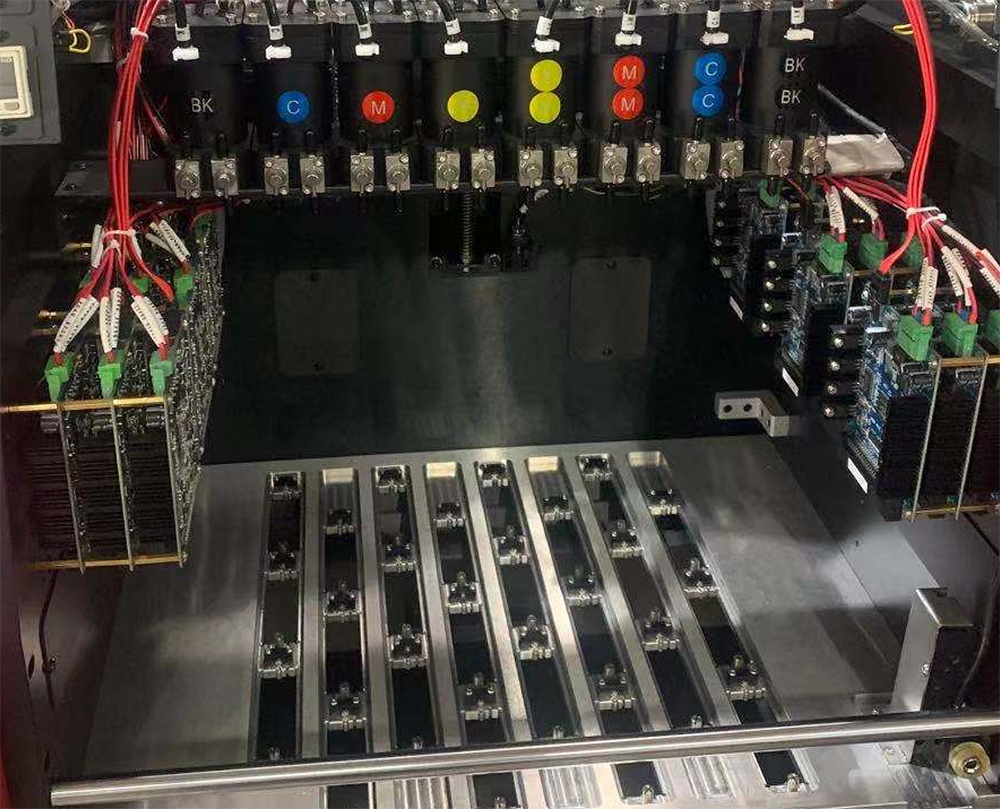
Understanding the Importance of Calibration
Calibration is the process of adjusting a printer’s settings to ensure that it produces accurate and consistent colors, image quality, and print positioning. In the context of UV flatbed printers, calibration involves fine-tuning various parameters such as ink flow, print head alignment, media positioning, and color profiling. Proper calibration not only enhances print quality but also reduces waste, improves productivity, and extends the lifespan of the printer’s components.
Preliminary Steps
Before diving into the calibration process, it’s essential to perform a few preliminary checks and preparations:
Cleanliness: Ensure that the printer, print heads, and platen are clean and free of dust, debris, and ink residue. A clean environment is critical for accurate calibration.
Media Preparation: Use high-quality media that is compatible with the printer’s specifications. Ensure that the media is flat, free of wrinkles, and properly loaded onto the printer’s platen.
Ink Levels: Check and refill ink cartridges or tanks as needed. Low ink levels can affect print quality and calibration accuracy.
Software Updates: Ensure that the printer’s firmware and associated software are up-to-date. Manufacturers often release updates that improve printer performance and address calibration issues.
Calibration Procedures
1. Print Head Alignment
Print head alignment is fundamental to ensuring that ink is deposited accurately on the media. Misalignment can result in banding, blurring, or uneven print quality.
Step-by-Step Guide:
Access the printer’s maintenance or calibration menu through the control panel or printer software.
Select the ‘Print Head Alignment’ option.
Follow the on-screen instructions to print an alignment pattern. This pattern typically consists of several lines or boxes that should align perfectly when printed correctly.
Examine the printed alignment pattern. If the lines or boxes are not aligned, use the printer’s adjustment controls to make fine corrections.
Repeat the process until the alignment pattern is perfect.
2. Color Calibration
Color calibration involves adjusting the printer’s color settings to match a desired color standard or profile. This step ensures that the colors in the print match the colors on the screen or a reference sample.
Step-by-Step Guide:
Use a color calibration tool or software to create a test chart. This chart contains a series of color patches that represent different color values.
Print the test chart on the UV flatbed printer.
Use a spectrophotometer or colorimeter to measure the color values of the printed patches.
Compare the measured values to the desired color standards.
Adjust the printer’s color settings, such as ink density, hue, and saturation, to align the printed colors with the standards.
Repeat the process until the color match is acceptable.
3. Media Positioning and Feed Adjustment
Accurate media positioning ensures that prints are centered and aligned correctly on the substrate. Feed adjustment is crucial for maintaining consistent print quality across the entire print area.
Step-by-Step Guide:
Load a test sheet or media into the printer.
Access the printer’s media positioning or feed adjustment settings.
Print a test pattern that includes markers or registration lines.
Examine the printed pattern. If the markers are not aligned or the print is skewed, adjust the media positioning or feed settings.
Make small adjustments and reprint the test pattern until the alignment is perfect.
4. Resolution and Ink Flow Calibration
Resolution calibration ensures that the printer’s dots per inch (DPI) setting matches the actual output. Ink flow calibration adjusts the amount of ink deposited on the media, affecting print density and clarity.
Step-by-Step Guide for Resolution Calibration:
Print a resolution test chart that includes fine lines and details.
Inspect the print for clarity and detail. If the lines are not sharp or the details are lost, adjust the printer’s DPI setting.
Reprint the test chart and evaluate the results until the desired resolution is achieved.
Step-by-Step Guide for Ink Flow Calibration:
Print a test pattern that includes solid color blocks.
Examine the print for consistency in color density and ink coverage.
If the ink flow is too heavy or too light, adjust the ink flow settings in the printer’s software.
Reprint the test pattern and adjust the settings as needed until the ink flow is balanced.
Advanced Calibration Techniques
For those seeking even higher precision, several advanced calibration techniques can be employed:
1. Linearization
Linearization ensures that the printer’s output is consistent across the entire grayscale or color range. This process involves creating a lookup table (LUT) that maps input values to output values, correcting for any nonlinearities in the printer’s response.
Process:
Print a linearization test chart that includes a series of graduated color patches.
Measure the color values of the patches using a spectrophotometer.
Use the measured values to create or adjust the LUT in the printer’s software.
Apply the LUT to ensure that the printer’s output is linearized.
2. Profiler Calibration
Profiler calibration involves creating custom color profiles that match the specific characteristics of the printer, ink, and media being used. This step is particularly important for achieving accurate color reproduction in critical applications.
Process:
Use a profiling software to generate a series of test charts.
Print the test charts on the UV flatbed printer.
Measure the color values of the printed charts using a spectrophotometer.
Use the measurement data to create a custom color profile.
Load the custom profile into the printer’s software to ensure accurate color matching.
UV flatbed printer calibration is a meticulous process that requires attention to detail and a thorough understanding of the printer’s capabilities. By following the outlined procedures and techniques, printer operators can ensure that their UV flatbed printers produce high-quality, consistent prints. Regular calibration not only enhances print quality but also maximizes printer efficiency and prolongs the life of the printer’s components. Whether you’re a seasoned professional or a newcomer to the world of UV flatbed printing, mastering the calibration process is essential for achieving optimal print results.