UV Flatbed Printer: A Guide to Media Handling Best Practices
In the realm of digital printing, UV flatbed printers have revolutionized the way we approach printing on a multitude of substrates. These versatile machines offer unparalleled flexibility, enabling printers to produce high-quality images on materials ranging from rigid boards to flexible fabrics. However, harnessing the full potential of a UV flatbed printer requires more than just pushing a button. It demands a thorough understanding of media handling best practices to ensure optimal print quality, efficiency, and equipment longevity. This guide delves into the essentials of media handling for UV flatbed printers, providing insights that can elevate your printing game.
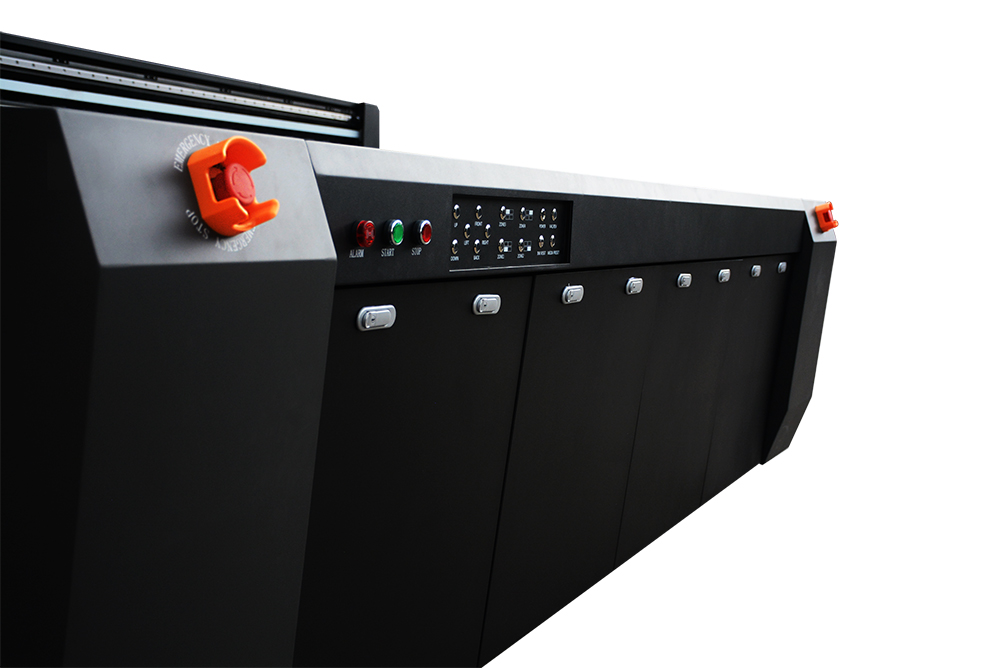
Understanding the Basics of UV Flatbed Printers
UV flatbed printers utilize ultraviolet light to cure inks instantly upon contact with the substrate. This process allows for precise control over the ink’s deposition and curing, resulting in vibrant, durable prints. The ability to print on a wide array of materials without the need for pre-treatment or primers is a hallmark of UV flatbed technology. However, this versatility also presents unique challenges, particularly in terms of media handling.
Media Preparation: The First Step to Success
Before loading any material into your UV flatbed printer, it’s crucial to prepare it adequately. Here are some key steps:
Cleaning and Drying: Ensure that the substrate is clean, dry, and free of dust, oils, or any contaminants that could affect ink adhesion. Use a lint-free cloth and a mild cleaning solution if necessary, followed by thorough drying.
Flatness and Stability: The material should be flat and stable to prevent warping or shifting during printing. For rigid materials, ensure they are properly supported to maintain flatness. Flexible materials may require tensioning systems to keep them taut.
Size and Thickness: Verify that the media’s dimensions and thickness are within the printer’s specifications. Exceeding these limits can cause jams, damage to the print heads, or poor print quality.
Choosing the Right Media for Your Project
The choice of media can significantly impact the final outcome of your print job. Consider the following factors when selecting a substrate:
Ink Absorption: Different materials absorb ink differently. Some may require more ink to achieve the desired color saturation, while others may be prone to ink bleeding or pooling. Understanding the media’s absorption properties will help you adjust the ink settings accordingly.
Surface Texture: The texture of the material can affect the way ink adheres and the overall appearance of the print. Smooth surfaces generally yield the best results, while textured or porous materials may require special handling or additional coats of ink.
Durability Requirements: Depending on the application, the printed material may need to withstand wear and tear, exposure to the elements, or chemical resistance. Choose a substrate that meets these durability requirements.
Loading and Positioning the Media
Proper loading and positioning of the media are critical to achieving accurate prints. Follow these guidelines:
Alignment: Ensure the media is correctly aligned with the printer’s registration marks or guides. Misalignment can lead to cropping issues or image distortion.
Tension Control: For flexible materials, maintain the correct tension to prevent sagging or stretching. Too much tension can cause the material to tear, while too little can result in wrinkles or creases.
Support Structures: When printing on rigid or thick materials, use support structures or spacers to ensure even ink deposition and prevent the print heads from coming into contact with the media.
Printing Techniques and Adjustments
Once the media is properly loaded, it’s time to focus on the printing process itself. Here are some techniques and adjustments that can enhance print quality:
Ink Coverage and Layering: Adjust the ink coverage settings to match the media’s absorption capabilities. In some cases, multiple thin layers of ink may produce better results than a single thick layer.
Curing Settings: The UV curing process is crucial for ink adhesion and durability. Adjust the curing intensity and duration according to the media type and ink used. Overcuring can cause brittleness, while undercuring may result in poor ink adhesion.
Test Prints: Always perform test prints before starting a full production run. This allows you to fine-tune the settings and ensure that the print quality meets your expectations.
Post-Printing Handling and Care
The job doesn’t end once the printing is complete. Proper post-printing handling and care are essential to preserve the quality of the printed material:
Drying and Curing: Allow the printed material to cool down and fully cure before handling or further processing. Some materials may require additional time or post-curing processes to achieve maximum durability.
Cutting and Finishing: Use appropriate tools and techniques for cutting and finishing the printed material. Ensure that the cutting edges are sharp to prevent tearing or fraying.
Storage and Transportation: Store the printed materials in a cool, dry place away from direct sunlight and extreme temperatures. Use protective packaging for transportation to prevent damage.
Troubleshooting Common Issues
Despite your best efforts, issues may arise during media handling and printing. Here are some common problems and their solutions:
Ink Bleeding or Smudging: This can be caused by excessive ink coverage or insufficient curing. Adjust the ink settings and curing parameters accordingly.
Image Distortion: Misalignment or incorrect media tension can lead to image distortion. Re-align the media and adjust the tension as needed.
Print Head Clogs: Clogs can occur due to dried ink or debris. Regularly clean and maintain the print heads to prevent clogging.
Mastering media handling for UV flatbed printers is a journey that requires patience, attention to detail, and a willingness to learn. By following the best practices outlined in this guide, you can ensure that your UV flatbed printer produces high-quality prints consistently, efficiently, and reliably. Remember, the key to success lies in proper preparation, careful loading and positioning, meticulous printing techniques, and diligent post-printing care. With these principles in mind, you’ll be well on your way to becoming a UV flatbed printing expert.