UV Flatbed Printer: A Guide to Printing on Fabric
UV Flatbed Printer: A Guide to Printing on Fabric
In the realm of digital printing, the UV flatbed printer has emerged as a versatile and innovative tool, particularly when it comes to printing on fabric. This technology has revolutionized the way textiles are decorated, allowing for intricate designs, vibrant colors, and a wide range of applications. From fashion apparel to home decor, UV flatbed printers have opened up new possibilities for creativity and customization. In this guide, we will delve into the world of UV flatbed printing on fabric, exploring its working principles, advantages, limitations, and the steps involved in achieving optimal results.
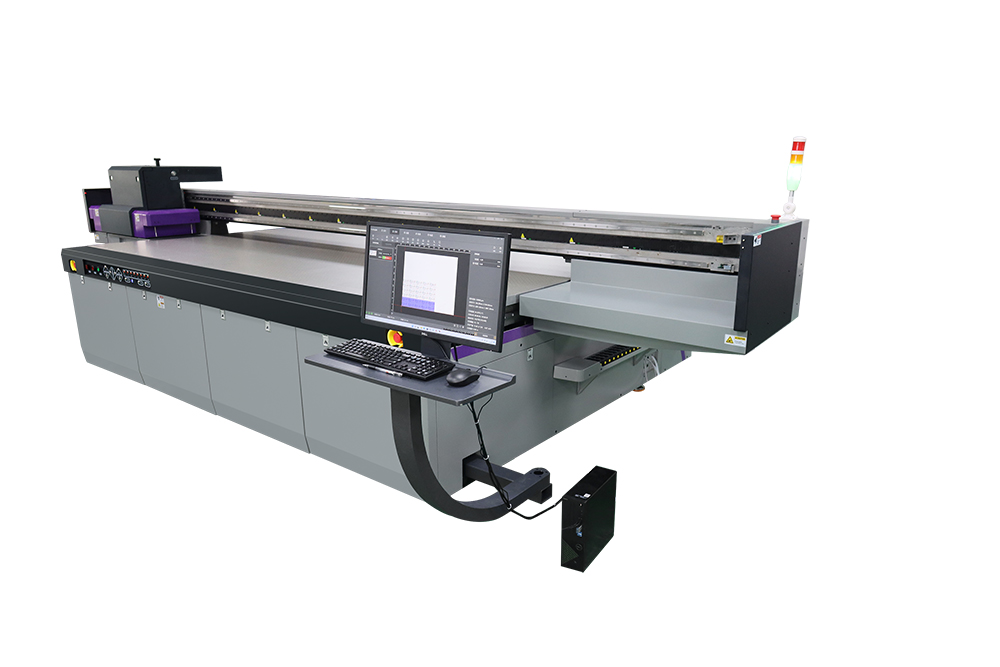
Understanding UV Flatbed Printers
A UV flatbed printer is a type of digital printing machine that uses ultraviolet (UV) light to cure ink as it is applied to a substrate. Unlike traditional inkjet printers that rely on solvent-based or water-based inks, UV printers use special UV-curable inks that solidify when exposed to UV light. This process enables the printer to produce high-quality, durable prints that are resistant to fading, scratching, and water damage.
The flatbed design of these printers allows for the printing of rigid or semi-rigid materials, including but not limited to, glass, metal, plastic, wood, and, importantly, fabric. The printer’s bed can accommodate various sizes and shapes of materials, making it highly flexible for different printing needs.
Printing on Fabric: Unique Considerations
When it comes to printing on fabric, several factors must be taken into account to ensure a successful print job. These include the type of fabric, its pretreatment, ink adhesion, and post-printing processes.
Fabric Types
Not all fabrics are suitable for UV flatbed printing. Natural fibers like cotton and silk, as well as synthetic materials such as polyester and nylon, can be printed on, but each requires specific handling. For instance, natural fibers may need pre-treatment to improve ink absorption, while synthetic fabrics might require special coatings to enhance ink adhesion.
Pre-Treatment and Preparation
Before printing, fabrics often need to be pre-treated to ensure optimal ink absorption and adhesion. This process can involve applying a special coating or primer that helps the UV ink bond securely to the fabric’s surface. Pre-treatment also helps to prevent ink bleeding or spreading, ensuring a sharp and clear print.
Additionally, the fabric should be properly stretched or mounted on the printer’s bed to avoid any wrinkles or creases that could affect the print quality. This step is crucial for achieving a smooth and uniform print.
Ink Adhesion and Durability
One of the key advantages of UV flatbed printing is the durability of the prints. The UV-curable inks form a strong bond with the fabric, creating a print that is resistant to fading, scratching, and even some chemicals. However, the adhesion strength can vary depending on the fabric type and pre-treatment used.
To ensure long-lasting prints, it is important to choose high-quality UV inks and follow the manufacturer’s recommendations for pre-treatment and curing times. Proper curing is essential as it allows the ink to fully harden and adhere to the fabric.
Advantages of UV Flatbed Printing on Fabric
High-Quality Prints
UV flatbed printers are capable of producing highly detailed and vibrant prints. The use of UV-curable inks results in sharp lines, smooth gradients, and vivid colors that can rival traditional dye-sublimation or screen-printing methods.
Versatility
The ability to print on a wide range of fabrics and substrates makes UV flatbed printing highly versatile. From thin and delicate silk to thick and sturdy canvas, the printer can handle various materials with ease. This versatility allows for creative applications in fashion, home decor, and even industrial settings.
Customization
UV flatbed printing enables high levels of customization. With digital files, it is easy to make changes to designs, add personalization, or create one-off pieces. This makes it ideal for small-batch production, prototypes, or custom orders.
Durability
As mentioned, UV-cured inks are highly durable and resistant to fading, scratching, and water damage. This makes UV-printed fabrics suitable for outdoor use, such as banners, awnings, and even upholstery in high-traffic areas.
Limitations and Challenges
While UV flatbed printing on fabric offers many benefits, it also comes with its own set of challenges and limitations.
Cost
UV flatbed printers and their associated inks can be more expensive than traditional printing methods. The initial investment in equipment and the ongoing cost of consumables can be a barrier for some businesses.
Fabric Compatibility
Not all fabrics are suitable for UV printing. Some materials may require extensive pre-treatment or special coatings, which can add to the overall cost and complexity of the process.
Curing Time
The UV curing process requires time, which can affect production speed. Depending on the ink and the printer’s settings, curing times can vary, potentially slowing down the overall printing process.
Steps to Successful UV Flatbed Printing on Fabric
To achieve optimal results when printing on fabric with a UV flatbed printer, follow these steps:
Choose the Right Fabric: Select a fabric that is compatible with UV printing and suitable for your intended application. Consider factors such as fiber content, weight, and texture.
Pre-Treat the Fabric: Follow the manufacturer’s recommendations for pre-treating the fabric. This may involve applying a special coating or primer to improve ink adhesion.
Prepare the Digital File: Create or obtain a high-resolution digital file of your design. Ensure that the file is in the correct format and has the appropriate color profile for UV printing.
Mount the Fabric: Properly stretch or mount the fabric on the printer’s bed. Use clips, tape, or other methods to ensure that the fabric is smooth and wrinkle-free.
Print and Cure: Set up the printer with the appropriate ink and settings. Print the design onto the fabric, following the printer’s instructions for ink coverage and curing times.
Post-Processing: After printing, allow the fabric to cool and the ink to fully cure. Depending on the application, you may need to perform additional steps, such as cutting, sewing, or applying finishing treatments.
Quality Control: Inspect the printed fabric for any defects or issues. Make any necessary adjustments to the design or printing process to ensure consistent quality.
Conclusion
UV flatbed printing on fabric offers a world of creative possibilities, combining high-quality prints with versatility and durability. By understanding the principles of UV printing, the unique considerations for fabric, and the steps involved in the process, you can achieve stunning results that meet your creative and functional needs. Whether you’re a fashion designer, a home decor enthusiast, or a business looking to expand your product offerings, UV flatbed printing on fabric is a technology worth exploring. With the right equipment, materials, and techniques, you can unlock the full potential of this innovative printing method and bring your visions to life.