UV Flatbed Printer: A Guide to Printing on Foam Board and Gatorfoam
In the realm of digital printing, versatility and precision are paramount. Among the myriad of printing technologies available, UV flatbed printers stand out for their ability to print directly onto a wide variety of substrates, including foam board and Gatorfoam. These materials, known for their lightweight yet sturdy characteristics, are favorites in the signage, display, and architectural industries. This guide delves into the intricacies of using a UV flatbed printer to achieve outstanding prints on foam board and Gatorfoam, exploring preparation techniques, printer settings, and post-processing tips to ensure optimal results.
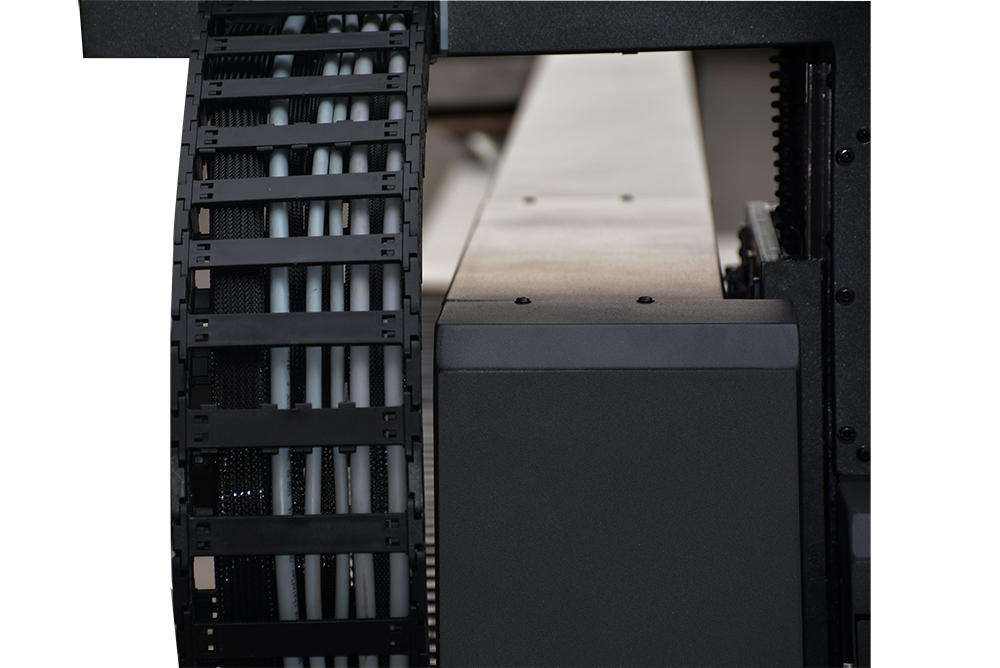
Understanding Foam Board and Gatorfoam
Before diving into the printing process, it’s essential to understand the substrates at hand. Foam board, also known as foam core, is a sandwich-structured material consisting of a polystyrene foam core bonded between two layers of paper or cardstock. It is lightweight, easy to cut, and versatile, making it ideal for applications like mounting photographs, creating presentations, and crafting signs.
Gatorfoam, on the other hand, is a more robust variant, often used in high-impact or outdoor applications. It features a polystyrene foam core but is encased in a thicker, more durable layer of exterior paper or plastic. This added durability makes Gatorfoam suitable for long-term displays, exhibition panels, and architectural models where strength and weather resistance are crucial.
Preparing for Printing
Success in UV printing on foam board and Gatorfoam begins with proper preparation. Here are the key steps to ensure your substrates are ready for optimal print quality:
Cleaning the Surface: Dust, dirt, and oils can interfere with the ink’s adhesion to the substrate. Use a lint-free cloth and a mild cleaning solution to thoroughly clean the surface. Allow it to dry completely before proceeding.
Handling and Storage: Store foam board and Gatorfoam in a dry, flat environment to prevent warping or moisture absorption. Handle them with care to avoid fingerprints and scratches.
Cutting and Sizing: Ensure your substrate is cut to the exact size required for your print job. Precision is vital as UV flatbed printers rely on accurate registration for multi-pass printing.
Coating Considerations: Some foam boards may require a primer or coating to enhance ink adhesion and reduce ink absorption, which can lead to smearing. Consult your substrate manufacturer or printer’s guidelines for specific recommendations.
Printer Setup and Calibration
Achieving high-quality prints on foam board and Gatorfoam necessitates careful printer setup and calibration. Here’s how to fine-tune your UV flatbed printer:
Printer Bed Adjustment: Ensure the printer bed is level and free of debris. Adjust the height settings to accommodate the thickness of your substrate, preventing any head strikes during printing.
Ink Profile Selection: UV inks come in various formulations, each optimized for different substrates. Choose an ink profile specifically designed for foam-based materials. This ensures proper ink cure, adhesion, and color accuracy.
Calibration: Run a color calibration test to ensure that your printer’s colors match your desired output. This step is crucial for maintaining consistency across prints, especially when working with different substrates.
Resolution and Pass Settings: Adjust the printer’s resolution and number of passes to balance print quality with production speed. Higher resolutions and more passes generally result in finer details and smoother gradients but may increase print time.
Printing Techniques
With your substrate prepared and printer calibrated, it’s time to print. Here are some techniques to optimize your UV printing on foam board and Gatorfoam:
Test Prints: Always start with a test print, especially when working with a new substrate or ink. This allows you to assess ink adhesion, color accuracy, and any potential issues with the printing process.
Ink Coverage: Be mindful of ink coverage, particularly in solid areas. Excessive ink can lead to pooling, smearing, or even damage to the substrate. Use printer software to adjust ink density as needed.
Curing: UV inks require proper curing to achieve maximum durability and color saturation. Ensure your printer’s UV lamps are functioning correctly and set to the appropriate curing intensity and duration for foam-based materials.
Multi-Layer Printing: For best results, consider using a multi-layer printing technique. This involves printing in layers, allowing each layer to cure before adding the next. This approach enhances color depth, ink adhesion, and overall print quality.
Post-Processing Tips
Once your prints are complete, post-processing is essential to protect and enhance your work. Here are some tips for finishing your foam board and Gatorfoam prints:
Drying and Curing: After printing, allow your prints to fully cure. This may involve additional time under UV lights or in a drying rack, depending on your printer’s specifications.
Cutting and Trimming: Use a sharp utility knife or cutting machine to trim excess material and achieve clean edges. For intricate cuts, consider using a laser cutter or router.
Lamination: To further protect your prints and enhance their durability, consider laminating them with a clear, UV-resistant film. This step is particularly beneficial for outdoor or high-traffic applications.
Mounting and Display: Depending on your application, you may need to mount your foam board or Gatorfoam prints. Use appropriate adhesives or mounting hardware to ensure they are securely attached to their display surface.
Troubleshooting Common Issues
Even with the best preparations, issues can arise during UV printing on foam board and Gatorfoam. Here are some common problems and their solutions:
Ink Adhesion Issues: If ink is not adhering properly, check for contamination on the substrate surface, incorrect ink profiles, or insufficient curing. Cleaning the substrate and adjusting printer settings can often resolve this issue.
Warping or Curling: Foam-based materials can warp or curl if not handled properly. Ensure they are stored flat and avoid exposing them to extreme temperatures or humidity.
Color Inconsistencies: If colors appear dull or inaccurate, recalibrate your printer and check your ink profiles. Ensure your printer’s UV lamps are at the correct intensity and that your substrates are consistent in thickness and composition.
Smearing or Bleeding: Excessive ink coverage can lead to smearing or bleeding. Adjust your printer’s ink density settings and consider using a primer or coating to improve ink absorption.
UV flatbed printing on foam board and Gatorfoam offers a versatile, high-quality solution for a wide range of applications. By understanding your substrates, properly preparing them, fine-tuning your printer settings, and employing best practices in printing and post-processing, you can achieve outstanding results that meet the demands of even the most discerning clients. Whether you’re creating vibrant signage, detailed architectural models, or durable outdoor displays, UV flatbed printing on foam-based materials is a powerful tool in your digital printing arsenal.