UV Flatbed Printer: A Guide to Printing on Leather and Synthetic Materials
UV Flatbed Printer: A Guide to Printing on Leather and Synthetic Materials
In the realm of digital printing, UV flatbed printers have emerged as versatile and powerful tools, capable of producing high-quality images on a wide array of substrates. Among these substrates, leather and synthetic materials present unique opportunities and challenges for printers seeking to create visually stunning and durable prints. This guide aims to provide a comprehensive overview of using UV flatbed printers for printing on leather and synthetic materials, covering essential aspects such as material preparation, printing techniques, post-processing, and considerations for achieving optimal results.
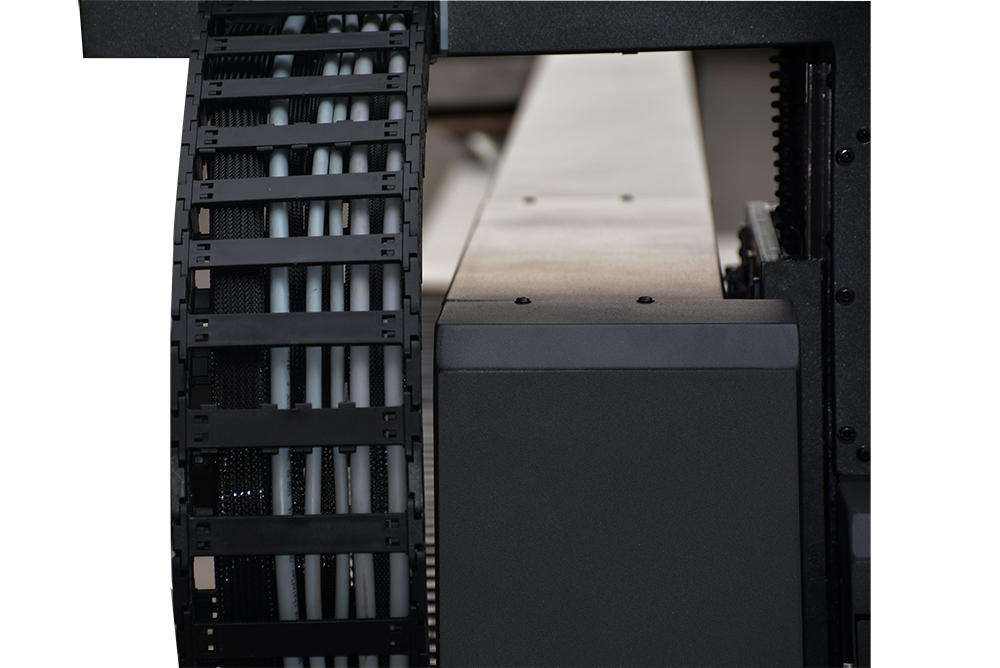
Understanding UV Flatbed Printers
UV flatbed printers utilize ultraviolet (UV) light to cure ink instantly as it is deposited onto the substrate. This process, known as UV curing, allows for precise control over ink placement and ensures that the ink adheres firmly to the material, resulting in vibrant, long-lasting prints. These printers are designed to handle rigid and semi-rigid materials, making them ideal for printing on items like leather, vinyl, plastic, glass, and metal.
One of the key advantages of UV flatbed printers is their ability to print directly onto the substrate without the need for transfer papers or additional layers, which can enhance image clarity and reduce material waste. Furthermore, UV inks are known for their excellent resistance to fading, scratching, and chemical exposure, making them suitable for both indoor and outdoor applications.
Leather: A Natural and Versatile Substrate
Leather, derived from animal hides, offers a unique combination of durability, flexibility, and aesthetic appeal. It is widely used in products such as furniture, accessories, and automotive interiors. When printing on leather, several factors must be considered to ensure optimal results:
Material Preparation:
Cleaning: Before printing, leather should be thoroughly cleaned to remove any dirt, oils, or contaminants that could affect ink adhesion.
Conditioning: Applying a suitable leather conditioner can help maintain the material’s suppleness and prevent cracking during or after the printing process.
Stretching and Flattening: Leather may need to be stretched or flattened to ensure a smooth and even printing surface. This is particularly important for avoiding ink bleeding or uneven coverage.
Printing Techniques:
Resolution and Ink Coverage: Adjusting the printer’s resolution and ink coverage settings is crucial for achieving the desired print quality on leather. Higher resolutions and lighter ink coverage are generally recommended to prevent ink from soaking into the leather excessively, which could lead to smudging or color distortion.
White Base Layer: Due to leather’s natural color variations, applying a white base layer before printing the actual design can help enhance color accuracy and vibrancy.
Post-Processing:
Curing: After printing, UV curing should be thoroughly performed to ensure the ink is fully set and adhered to the leather. This step is critical for the long-term durability of the print.
Finishing: Depending on the desired look and feel, additional finishes such as varnishes or protective coatings may be applied to enhance the leather’s appearance and protect the print from wear and tear.
Synthetic Materials: Versatility and Consistency
Synthetic materials, such as polyurethane (PU), polyvinyl chloride (PVC), and polyester, offer a wide range of textures, colors, and durability levels. They are often used as alternatives to natural materials like leather due to their cost-effectiveness, consistency, and ease of maintenance. When printing on synthetic materials, the following considerations are essential:
Material Selection:
Compatibility: Not all synthetic materials are suitable for UV printing. It is crucial to select materials that are specifically designed or approved for UV ink applications.
Texture and Finish: The texture and finish of the synthetic material can significantly impact the final print quality. Smooth, non-porous surfaces generally yield the best results, while textured or porous materials may require special preparation or coatings to ensure proper ink adhesion.
Printing Techniques:
Profiling: Each synthetic material may require a unique color profile to achieve accurate and consistent colors. Working with the material supplier or printer manufacturer to create or obtain the appropriate profile is essential.
Adhesion Testing: Before full-scale production, conduct adhesion tests to ensure the ink adheres properly to the synthetic material. This can help prevent issues such as ink cracking, peeling, or fading over time.
Post-Processing:
Curing: As with leather, thorough UV curing is essential for ensuring the ink is fully set and adhered to the synthetic material. Follow the printer manufacturer’s recommendations for curing times and intensities.
Lamination: Depending on the application and desired durability, laminating the printed surface can provide additional protection against scratches, UV exposure, and chemicals.
Common Challenges and Solutions
Printing on leather and synthetic materials with a UV flatbed printer can present several challenges. Understanding these challenges and their solutions can help ensure successful prints:
Ink Bleeding and Smudging:
Cause: Ink may bleed or smudge if it is absorbed too deeply into the material or if the material is not properly prepared.
Solution: Use lighter ink coverage settings, apply a white base layer, and ensure the material is properly cleaned and conditioned before printing.
Color Accuracy:
Cause: Variations in material color, texture, and porosity can affect color accuracy.
Solution: Create or obtain accurate color profiles for each material, and consider applying a white base layer to improve color consistency.
Adhesion Issues:
Cause: Ink may not adhere properly to certain materials, leading to cracking, peeling, or fading.
Solution: Conduct adhesion tests, use materials specifically designed for UV printing, and apply protective coatings or laminations as needed.
Material Handling:
Cause: Leather and synthetic materials can be difficult to handle and position on the printer bed, especially if they are flexible or have irregular shapes.
Solution: Use vacuum tables or other material handling systems to secure the material in place, and consider cutting or trimming the material to fit the printer bed more easily.
Best Practices for Successful Printing
To achieve the best results when printing on leather and synthetic materials with a UV flatbed printer, follow these best practices:
Work with Experienced Suppliers: Choose material suppliers and printer manufacturers with a proven track record in UV printing. They can provide valuable guidance on material selection, print settings, and post-processing.
Conduct Test Prints: Always conduct test prints before full-scale production to ensure the material, ink, and print settings are optimized for the desired results.
Maintain the Printer: Regularly clean and maintain the printer to ensure optimal performance and prevent issues such as ink nozzle clogging or misalignment.
Use High-Quality Inks: Invest in high-quality UV inks that are specifically designed for the materials you are printing on. This can help ensure better color accuracy, durability, and adhesion.
Consider Environmental Factors: Monitor and control environmental factors such as temperature, humidity, and dust, as these can affect print quality and ink adhesion.
Conclusion
UV flatbed printers offer a powerful and versatile solution for printing on leather and synthetic materials. By understanding the unique challenges and considerations associated with these substrates, and following best practices for material preparation, printing techniques, and post-processing, you can achieve stunning, durable prints that meet your customers’ expectations. With the right tools, knowledge, and attention to detail, UV flatbed printing can help you unlock the full potential of leather and synthetic materials in your digital printing projects.