UV Flatbed Printer: A Guide to Printing on Plastic Materials
UV Flatbed Printer: A Guide to Printing on Plastic Materials
UV flatbed printers have revolutionized the printing industry, offering versatile and efficient solutions for printing on a wide range of materials, including plastics. This guide delves into the intricacies of using a UV flatbed printer for printing on plastic materials, highlighting its benefits, the types of plastics suitable for printing, the printing process, and tips for achieving optimal results.
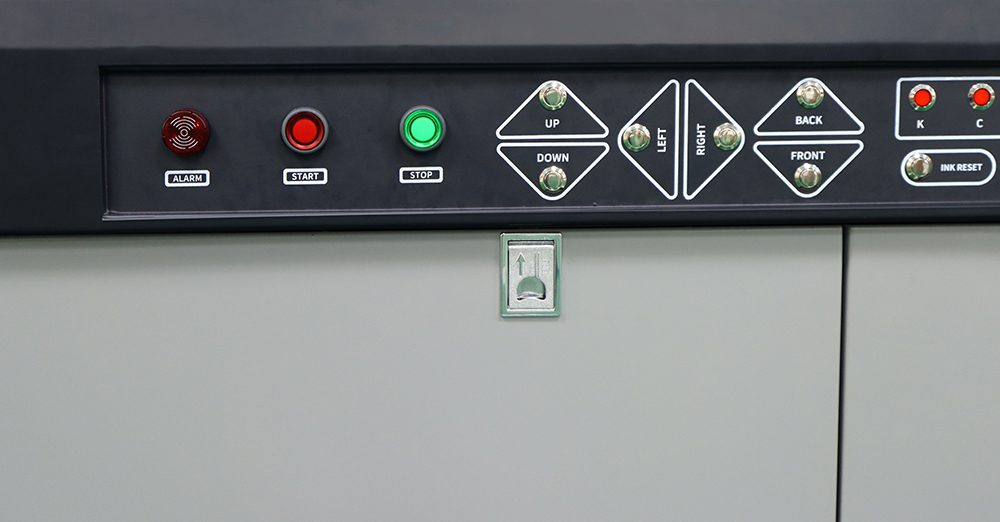
Introduction
In today’s fast-paced world, businesses constantly seek innovative ways to enhance their product offerings and marketing strategies. One such innovation that has significantly impacted various industries is the UV flatbed printer. This advanced printing technology enables direct printing onto flat surfaces, including plastics, offering unparalleled versatility in design and application.
UV flatbed printers utilize ultraviolet (UV) light to cure inks instantly, providing a durable and high-quality finish. This guide aims to explore the specifics of printing on plastic materials using UV flatbed printers, offering insights into the process, material compatibility, and best practices.
Understanding UV Flatbed Printers
What is a UV Flatbed Printer?
A UV flatbed printer is a digital printing machine that uses UV-curable inks to print directly onto flat or slightly curved surfaces. Unlike traditional printing methods, UV flatbed printers do not require printing plates or extensive setup processes, making them ideal for short-run and custom printing jobs.
Key Features
UV-Curable Inks: These inks cure instantly when exposed to UV light, resulting in quick turnaround times and durable prints.
Versatility: Capable of printing on a wide range of materials, including various types of plastics, metals, glass, wood, and more.
High Resolution: Offers high-resolution prints with vibrant colors and sharp details.
Customizability: Easily accommodates customization and variable data printing.
Benefits of Printing on Plastic with UV Flatbed Printers
Durability
UV-cured inks create a strong bond with the plastic surface, resulting in prints that are resistant to fading, scratching, and chemicals. This durability is particularly beneficial for outdoor applications and products that require long-lasting graphics.
Cost-Effectiveness
UV flatbed printing eliminates the need for printing plates and reduces material waste. It also allows for on-demand printing, minimizing inventory costs and enabling businesses to respond quickly to market demands.
Design Flexibility
With UV flatbed printers, you can print intricate designs, gradients, and even photographs directly onto plastic materials. This versatility opens up endless possibilities for creative applications.
Eco-Friendliness
UV-curable inks are often more environmentally friendly than traditional inks. They cure quickly, reducing the emission of volatile organic compounds (VOCs) and minimizing waste.
Types of Plastics Suitable for UV Flatbed Printing
Not all plastics are created equal, and their compatibility with UV flatbed printing varies. Here are some of the most common types of plastics suitable for this printing method:
1. Acrylic
Acrylic, also known as plexiglass, is a transparent or translucent thermoplastic often used for signage, displays, and architectural applications. It is highly suitable for UV flatbed printing due to its smooth surface and ability to adhere well to UV inks.
2. Polycarbonate
Polycarbonate is a strong and durable plastic commonly used in engineering applications, including electronics, automotive components, and safety glasses. Its impact resistance and heat stability make it an excellent choice for UV printing.
3. ABS
Acrylonitrile Butadiene Styrene (ABS) is a common thermoplastic known for its strength, flexibility, and heat resistance. It is widely used in consumer products, automotive parts, and electronic housings. ABS can be successfully printed on using UV flatbed printers, provided the surface is properly prepared.
4. Polyethylene (PE) and Polypropylene (PP)
These plastics are often used in packaging, containers, and piping due to their chemical resistance and flexibility. While they can be challenging to print on due to their non-porous nature, special primers and treatments can improve ink adhesion.
5. PVC
Polyvinyl Chloride (PVC) is a versatile plastic used in construction, electrical wiring, and packaging. It can be printed on using UV flatbed printers, but like PE and PP, surface preparation is crucial for optimal ink adhesion.
The Printing Process
Step-by-Step Guide
Material Preparation
Ensure the plastic surface is clean, dry, and free of any contaminants.
If necessary, apply a primer or adhesion promoter to improve ink adhesion.
Design and File Preparation
Create your design using graphic design software.
Convert the design into a suitable file format, such as PDF, TIFF, or JPEG, ensuring it meets the printer’s resolution requirements.
Printer Setup
Load the plastic material onto the flatbed printer.
Adjust the printer settings, including ink type, resolution, and cure time.
Printing
Initiate the printing process. The UV flatbed printer will deposit ink onto the plastic surface in a controlled manner.
UV lights will immediately cure the ink, creating a durable print.
Post-Processing
Remove the printed material from the printer.
If required, perform any additional finishing steps, such as cutting, trimming, or laminating.
Tips for Optimal Results
Proper Surface Preparation: Clean the plastic surface thoroughly and apply any necessary primers or adhesion promoters.
Test Prints: Conduct test prints on a sample piece of plastic to ensure proper ink adhesion and color accuracy.
Resolution Settings: Use high-resolution settings for intricate designs to ensure sharp details and vibrant colors.
Curing Time: Follow the manufacturer’s guidelines for ink curing times to ensure complete polymerization of the ink.
Maintenance: Regularly clean and maintain the printer to ensure consistent print quality and prevent clogging of ink nozzles.
Applications of UV Flatbed Printing on Plastics
Signage and Displays
UV flatbed printing allows for the creation of eye-catching signs and displays on plastic materials, ideal for businesses, events, and exhibitions.
Packaging
Customized packaging with high-quality graphics can be achieved through UV flatbed printing, enhancing product appeal and brand recognition.
Automotive and Electronics
UV printing on plastics is used in the automotive and electronics industries for creating durable labels, control panels, and decorative elements.
Artistic and Decorative Items
Artists and designers can utilize UV flatbed printers to create unique and intricate designs on plastic materials for artistic purposes or home decor.
Prototyping
UV flatbed printing enables quick and cost-effective prototyping of plastic components with detailed graphics and markings.
Conclusion
UV flatbed printers have transformed the way we print on plastic materials, offering a versatile, efficient, and cost-effective alternative to traditional printing methods. By understanding the capabilities of UV flatbed printers, the types of plastics suitable for printing, and the step-by-step printing process, businesses can unlock endless possibilities for creative and durable prints.
Whether you’re a business owner looking to enhance your product packaging, an artist exploring new mediums, or a manufacturer in need of durable labels, UV flatbed printing on plastics can provide the solution you’ve been searching for. With proper surface preparation, attention to detail, and regular maintenance, you can achieve outstanding results that meet your specific needs and exceed your expectations.