UV Flatbed Printer: A Guide to Printing on Plastics and Vinyl
In the realm of digital printing, UV flatbed printers have emerged as a game-changer, particularly when it comes to printing on plastics and vinyl. These versatile machines offer unparalleled precision, vibrant colors, and durability, making them ideal for a wide range of applications. From signage and vehicle wraps to promotional materials and personalized products, UV flatbed printers have revolutionized the way we print on non-traditional substrates. In this comprehensive guide, we will delve into the intricacies of UV flatbed printing, focusing specifically on its application to plastics and vinyl.
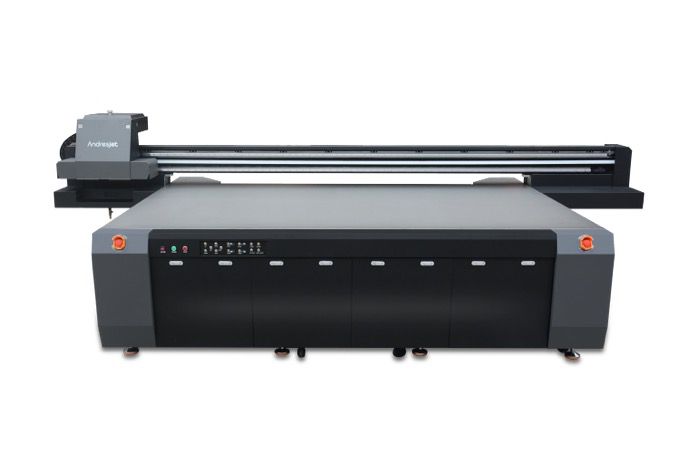
Understanding UV Flatbed Printers
At its core, a UV flatbed printer is a digital printing device that utilizes ultraviolet (UV) light to cure or dry ink instantly after it is applied to a substrate. This technology allows for precise control over the ink, resulting in sharp images and vibrant colors. Unlike traditional printing methods, UV flatbed printers do not require the use of solvents or heat to dry the ink, which significantly reduces drying times and environmental impact.
The flatbed design of these printers enables them to handle a variety of substrates, including rigid materials like plastics and flexible materials like vinyl. This versatility makes UV flatbed printers a popular choice for print shops, sign makers, and manufacturers looking to expand their product offerings.
Plastics and UV Flatbed Printing
Plastics are a diverse group of synthetic materials that are widely used in various industries due to their durability, flexibility, and cost-effectiveness. When it comes to UV flatbed printing on plastics, there are several key considerations to ensure optimal print quality and adhesion:
1. Substrate Compatibility
Not all plastics are created equal, and their compatibility with UV inks can vary. Common plastics used in UV flatbed printing include acrylic, polycarbonate, polyethylene (PE), polypropylene (PP), and polyvinyl chloride (PVC). Each type of plastic has unique properties that can affect ink adhesion and print quality. For instance, some plastics may require a pretreatment or the use of a specific type of UV ink to ensure proper adhesion.
2. Surface Preparation
The surface of the plastic substrate plays a crucial role in the printing process. It must be clean, dry, and free of any contaminants that could interfere with ink adhesion. In some cases, it may be necessary to use a surface cleaner or primer to prepare the plastic for printing. Additionally, the texture of the plastic can affect the final appearance of the print. Smooth surfaces will yield the best results, while textured surfaces may require special handling to achieve optimal print quality.
3. Ink Selection
The choice of UV ink is critical when printing on plastics. Different inks are formulated to adhere to specific types of plastics and to provide the desired level of durability and color saturation. It is important to consult with the printer manufacturer or ink supplier to select the appropriate ink for the chosen substrate.
4. Curing Process
The UV curing process is what sets UV flatbed printing apart from other printing methods. After the ink is applied to the substrate, it is exposed to UV light, which causes the ink to harden and adhere to the plastic. Proper curing is essential for achieving good print quality and durability. Over-curing can cause the ink to crack or discolor, while under-curing can result in poor adhesion and ink smudging.
Vinyl and UV Flatbed Printing
Vinyl is another popular substrate for UV flatbed printing, particularly in the signage and vehicle wrap industries. Its flexibility, durability, and ability to conform to various surfaces make it an ideal choice for many applications. However, printing on vinyl presents its own set of challenges:
1. Vinyl Types
There are two main types of vinyl used in UV flatbed printing: calendared and cast. Calendared vinyl is more rigid and less expensive, making it suitable for short-term applications like event signage. Cast vinyl, on the other hand, is more flexible and durable, making it ideal for long-term applications like vehicle wraps.
2. Adhesive Properties
The adhesive used on the back of the vinyl is another important consideration. Some adhesives are designed for temporary applications, while others are meant to be permanent. The choice of adhesive will depend on the intended use of the printed vinyl.
3. Stretchability
Vinyl has a certain degree of stretchability, which can affect the print quality if not properly accounted for. When printing on vinyl, it is important to ensure that the printer’s settings are adjusted to accommodate the material’s stretchiness. This may involve adjusting the tension settings or using a specialized printing profile.
4. Weather Resistance
One of the key advantages of UV flatbed printing on vinyl is the ability to produce prints that are highly resistant to weathering. UV inks are formulated to withstand the elements, ensuring that the prints remain vibrant and legible even when exposed to sunlight, rain, and other environmental factors.
Best Practices for UV Flatbed Printing on Plastics and Vinyl
To achieve the best results when printing on plastics and vinyl, consider the following best practices:
Test Prints: Always perform test prints on the chosen substrate before starting a production run. This will allow you to identify any potential issues with ink adhesion, color accuracy, or print quality.
Calibration: Regularly calibrate your printer to ensure accurate color matching and consistent print quality. This includes calibrating the printer’s color profiles, ink delivery systems, and UV curing lamps.
Maintenance: Proper maintenance of your UV flatbed printer is essential for achieving optimal performance and longevity. This includes regular cleaning of the print heads, ink systems, and UV lamps, as well as periodic inspections of the printer’s mechanics.
Substrate Handling: Handle substrates with care to avoid scratches, fingerprints, and other contaminants that could affect print quality. Use appropriate handling tools and techniques, such as gloves and substrate lifters, to minimize contact with the printing surface.
Post-Processing: Depending on the application, you may need to apply a protective layer or laminate to the printed surface to enhance durability and resistance to wear and tear. This can be particularly beneficial for outdoor applications or prints that will be subjected to heavy use.
UV flatbed printers have opened up new possibilities for printing on plastics and vinyl, offering unmatched precision, color vibrancy, and durability. By understanding the unique properties of these substrates and following best practices for printing, you can achieve outstanding results that meet the needs of your customers and stand up to the test of time. Whether you’re a seasoned professional or just starting out in the world of UV flatbed printing, this guide will serve as a valuable resource for mastering the art of printing on plastics and vinyl.