UV Flatbed Printer: A Guide to Printing on Rubber and Silicone Materials
UV Flatbed Printer: A Guide to Printing on Rubber and Silicone Materials
In the realm of digital printing, the UV flatbed printer has emerged as a versatile and powerful tool, capable of producing high-quality prints on a wide array of materials. Among these, rubber and silicone materials present unique challenges and opportunities for printers seeking to expand their capabilities. This comprehensive guide delves into the intricacies of using a UV flatbed printer for printing on rubber and silicone, exploring the technical aspects, material considerations, preparation steps, printing techniques, and post-processing requirements.
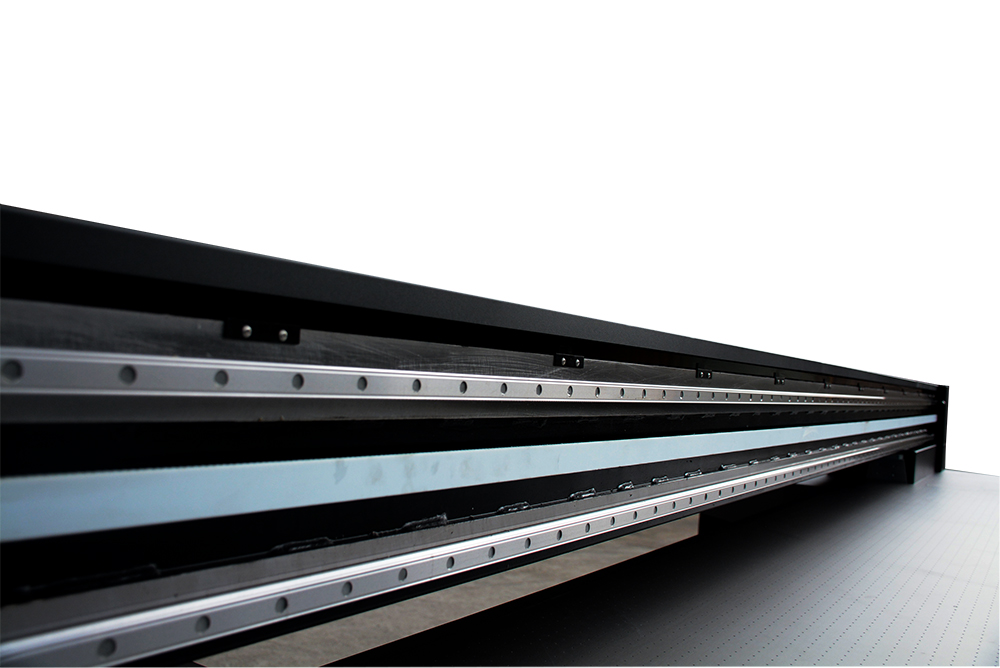
Understanding UV Flatbed Printers
UV flatbed printers utilize ultraviolet (UV) light to cure ink instantly onto the surface of the material. This process, known as UV curing, eliminates the need for heat drying, making it suitable for materials that might be damaged by high temperatures. The printer’s flatbed design accommodates rigid and flexible substrates of various sizes and shapes, offering unparalleled versatility.
Rubber and Silicone Materials: An Overview
Rubber and silicone are elastomeric materials known for their flexibility, durability, and resistance to extreme temperatures and chemicals. These properties make them ideal for a wide range of applications, including automotive parts, medical devices, gaskets, seals, and consumer products.
Rubber: Derived from natural or synthetic sources, rubber materials exhibit excellent elasticity and can withstand significant mechanical stress. They are often used in applications requiring high friction resistance and shock absorbency.
Silicone: A synthetic polymer, silicone is known for its superior heat resistance, electrical insulation, and chemical stability. It is frequently used in applications where high-temperature resistance and low chemical reactivity are crucial.
Challenges and Opportunities
Printing on rubber and silicone materials presents several challenges due to their inherent properties:
Adhesion: Ensuring that the ink adheres properly to the elastomeric surface without cracking, peeling, or fading over time.
Elasticity: Accommodating the material’s stretch and flexibility without compromising print quality.
Surface Preparation: Properly preparing the surface to accept ink and ensure a uniform print.
Despite these challenges, the rewards are significant. Successful printing on these materials can open up new markets and applications, particularly in industries where customization and branding are essential.
Material Preparation
Before printing, it is crucial to prepare the rubber or silicone material adequately:
Cleaning: Thoroughly clean the surface to remove any dirt, oils, or contaminants that may affect ink adhesion. Use a mild detergent or alcohol-based cleaner and ensure the surface is completely dry before proceeding.
Priming: Apply a primer designed specifically for elastomeric materials. This step improves ink adhesion and enhances the durability of the print. Ensure the primer is compatible with the UV ink and follow the manufacturer’s instructions for application.
Leveling: For uneven or textured surfaces, consider using a leveling agent to create a smooth, uniform base for the ink. This step is particularly important for ensuring consistent print quality.
Printing Techniques
When printing on rubber and silicone materials, several techniques can help optimize the outcome:
Test Prints: Always perform test prints on a small area of the material to ensure proper adhesion, color accuracy, and overall print quality. Adjust settings as necessary based on the test results.
Ink Selection: Choose UV inks specifically formulated for elastomeric materials. These inks are designed to adhere better to flexible surfaces and withstand the material’s stretching and bending.
Layering: To improve ink adhesion and durability, consider using a multi-layer printing process. This involves printing multiple thin layers of ink, allowing each layer to cure before applying the next.
Curing: Ensure the UV light is properly calibrated and set to the appropriate intensity and duration for the specific ink and material. Inadequate curing can lead to poor adhesion and reduced print durability.
Resolution and Detail: Adjust the printer’s resolution and print settings to achieve the desired level of detail and clarity. Higher resolutions may be necessary for intricate designs or small text.
Post-Processing
After printing, proper post-processing is essential to ensure the longevity and quality of the print:
Curing: Allow the printed material to cure fully according to the ink manufacturer’s recommendations. This may involve additional exposure to UV light or a specific curing process.
Handling and Storage: Handle the printed material with care to avoid damaging the print. Store it in a cool, dry place away from direct sunlight and harsh chemicals.
Protection: Consider applying a protective coating or laminate to further enhance the durability of the print, especially if the material will be exposed to harsh environments or frequent handling.
Applications and Industries
The ability to print on rubber and silicone materials opens up a wide range of applications and industries:
Automotive: Customize rubber gaskets, seals, and hoses with branding, part numbers, or safety instructions.
Medical Devices: Print on silicone tubing, stoppers, and other components for clear identification, instructions, or branding.
Consumer Products: Personalize silicone phone cases, watch bands, and other accessories with unique designs or logos.
Industrial: Mark rubber mats, belts, and other industrial components with safety warnings, part numbers, or company logos.
Sports and Fitness: Customize rubber and silicone grips, handles, and other components for sports equipment with team logos, sponsorships, or personalization.
Conclusion
Printing on rubber and silicone materials using a UV flatbed printer presents unique challenges, but with proper preparation, ink selection, and printing techniques, it is possible to achieve high-quality, durable prints. By understanding the material properties, adhering to best practices, and leveraging the versatility of UV flatbed printers, printers can tap into new markets and applications, offering customers customized, branded, and functional products that meet their specific needs.
As technology continues to evolve, the capabilities of UV flatbed printers will expand, further enhancing the potential for printing on elastomeric materials. By staying informed and adapting to new advancements, printers can continue to push the boundaries of what is possible, creating innovative and valuable products for their customers.