UV Flatbed Printer: A Guide to Printing on Wood
UV Flatbed Printer: A Guide to Printing on Wood
In the realm of digital printing, UV flatbed printers have emerged as a game-changer, particularly when it comes to printing on unconventional surfaces like wood. These versatile machines offer unparalleled precision, speed, and versatility, making them an ideal choice for businesses seeking to expand their printing capabilities beyond traditional paper and plastic substrates. This comprehensive guide delves into the intricacies of UV flatbed printing on wood, exploring its benefits, the process, considerations, and tips for achieving optimal results.
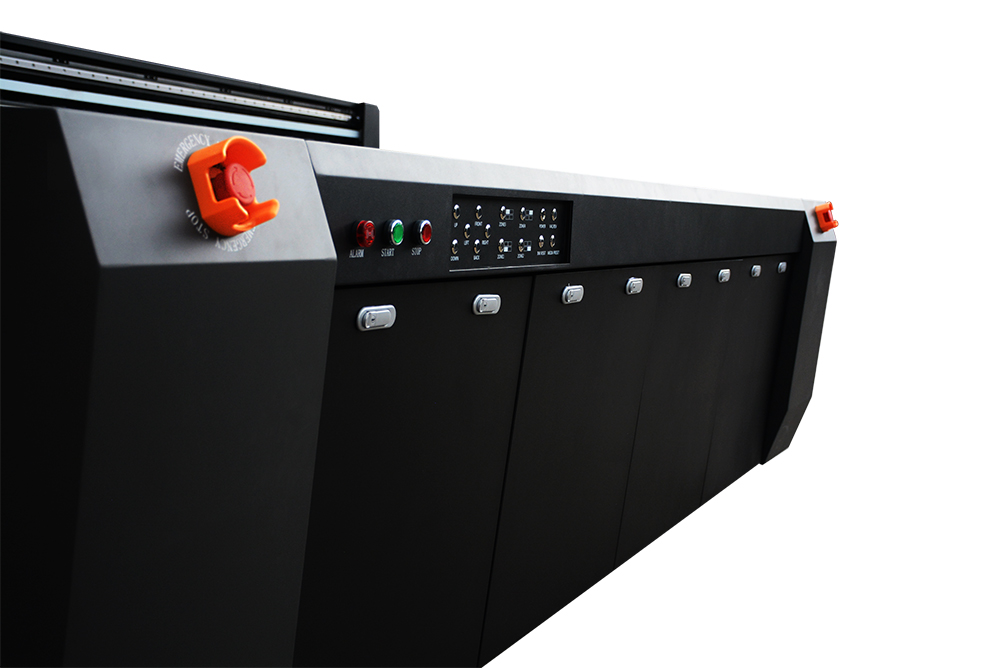
Understanding UV Flatbed Printing
UV flatbed printing, also known as UV-LED printing, is a cutting-edge technology that utilizes ultraviolet (UV) light to instantly cure or dry ink as it is applied to a surface. This method differs significantly from traditional solvent-based or aqueous printing systems, which require time for inks to evaporate or be absorbed. The UV curing process ensures that inks are instantly dried, resulting in vibrant, durable prints that are resistant to fading, scratching, and environmental factors.
Flatbed printers are designed to accommodate a wide range of materials and objects, thanks to their flat, open printing beds. This feature allows for direct printing onto substrates of various thicknesses and shapes, including wood, glass, metal, plastic, and more. When printing on wood, UV flatbed printers offer unique advantages that enhance the aesthetic and functional qualities of the printed pieces.
Benefits of UV Flatbed Printing on Wood
Exceptional Durability: UV-cured inks create a hard, protective layer on the wood surface, enhancing its resistance to wear and tear, moisture, and UV rays. This durability ensures that printed designs retain their vividness and integrity over time.
Versatility in Design: With UV flatbed printing, intricate designs, fine details, and a broad color gamut can be achieved, allowing for highly customized and visually appealing prints on wood.
Eco-Friendliness: UV-LED printing is more environmentally friendly than traditional solvent-based systems. It emits low levels of volatile organic compounds (VOCs) and consumes less energy, making it a sustainable choice for printing on wood.
Cost-Effective: The ability to print directly onto wood eliminates the need for additional materials like adhesive films or transfer papers, reducing overall production costs.
Rapid Production: UV inks cure instantly under UV light, significantly reducing print time and enabling faster turnaround for projects.
The Process of UV Flatbed Printing on Wood
Preparation: Start by selecting the appropriate wood type based on the project requirements. Ensure the wood is clean, dry, and free from dust, dirt, or oils. Sanding may be necessary to create a smooth surface for printing.
Design Creation: Develop or select the digital design that will be printed onto the wood. High-resolution images or vector graphics are recommended for the best print quality.
Printing: Load the wood onto the flatbed printer, ensuring it is securely positioned and aligned correctly. Adjust the printer settings according to the wood type and desired print outcome. Begin the printing process, which involves depositing UV-curable ink onto the wood surface and immediately curing it with UV light.
Post-Processing: Depending on the project, additional steps such as cutting, sanding, or applying a protective coating may be necessary. For some applications, a clear UV varnish can be applied to enhance gloss and durability.
Quality Control: Inspect the printed wood for any defects or inconsistencies. Make necessary adjustments to the printer settings or preparation process to ensure consistent quality in subsequent prints.
Considerations for UV Flatbed Printing on Wood
Wood Type and Grain: Different wood types have varying densities, textures, and moisture content, which can affect ink absorption and adhesion. Consider these factors when selecting wood for printing.
Ink Compatibility: Ensure that the UV inks used are compatible with wood and provide the desired color saturation, opacity, and durability.
Print Resolution: Adjust the printer’s resolution settings to achieve the desired level of detail and sharpness in the printed design.
Curing Temperature: UV curing requires precise temperature control to ensure proper ink drying. Monitor and adjust the UV lamp’s intensity and exposure time as needed.
Warping and Expansion: Wood is susceptible to warping and expansion due to changes in temperature and humidity. Account for these potential issues during the design and preparation stages.
Tips for Successful UV Flatbed Printing on Wood
Conduct thorough testing with different wood types and ink formulations to determine the best combination for your specific project requirements.
Use a primer or pre-treatment solution to improve ink adhesion and enhance print quality, especially on porous or oily wood surfaces.
Regularly clean and maintain your UV flatbed printer to ensure consistent print quality and prevent ink buildup or clogging.
Consider using fixtures or clamps to secure the wood in place during printing, preventing movement and ensuring precise alignment.
Experiment with different print modes and curing settings to achieve the desired balance between print speed and quality.
Conclusion
UV flatbed printing on wood offers a wealth of opportunities for businesses seeking to create unique, high-quality products. By understanding the process, considering key factors, and implementing best practices, it is possible to achieve exceptional results that showcase the beauty and versatility of wood as a printing substrate. As technology continues to advance, the potential applications for UV flatbed printing on wood are bound to expand, further pushing the boundaries of creative expression and product innovation.