UV Flatbed Printer: An Introduction to UV Curing Technology
UV Flatbed Printer: An Introduction to UV Curing Technology
Introduction
The advent of technology has revolutionized various industries, with the printing sector being no exception. Among the numerous advancements, UV flatbed printers have emerged as a game-changer, particularly due to their integration of UV curing technology. This article aims to provide a comprehensive understanding of UV flatbed printers and delve into the intricacies of UV curing technology, highlighting its significance, working principles, applications, and the future prospects it holds.
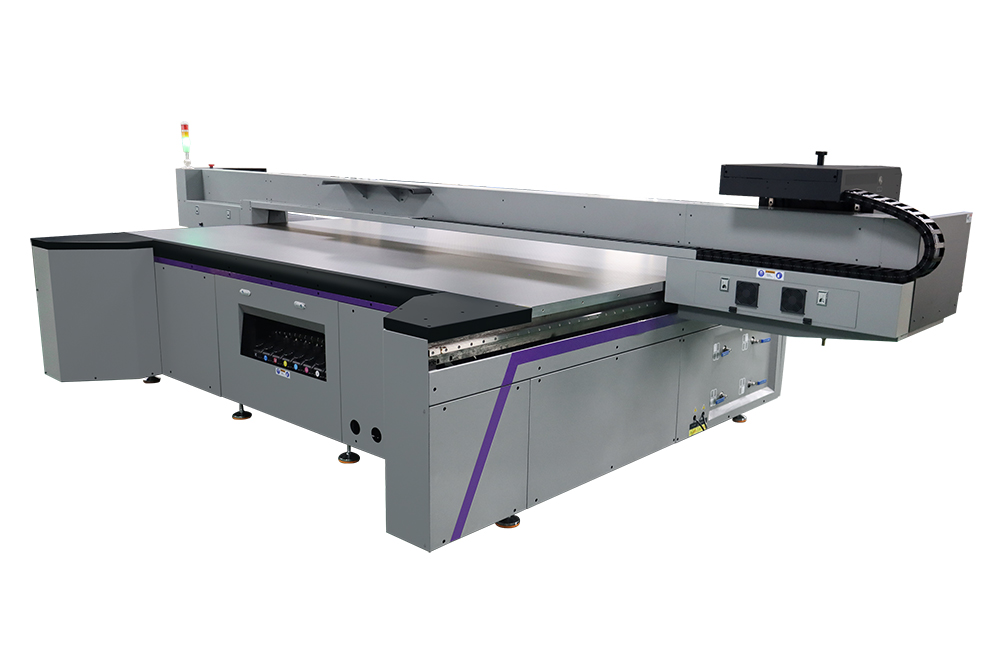
Understanding UV Flatbed Printers
UV flatbed printers are sophisticated digital printing machines that utilize UV (Ultraviolet) curing technology to print directly onto a wide range of substrates. Unlike traditional printing methods that require pre-printing preparation such as plate making, UV flatbed printers can produce high-quality images on demand, making them ideal for short-run and customized printing jobs. These printers are capable of handling diverse materials, including but not limited to, glass, metal, wood, plastic, ceramic, and even textiles, expanding their applicability across multiple industries.
The Core: UV Curing Technology
UV curing technology forms the backbone of UV flatbed printers. It is a process where ultraviolet light is used to instantly cure or dry ink, adhesives, or coatings applied to a substrate. This technology leverages the photochemical reaction between UV light and special UV-curable inks, which contain photoinitiators. When exposed to UV radiation, these photoinitiators absorb the energy and trigger a chain reaction, converting the liquid ink into a solid film in a fraction of a second.
Working Principles of UV Curing in Flatbed Printers
Ink Application: The UV flatbed printer deposits UV-curable ink onto the substrate through precision nozzles or jets. These inks are formulated to be highly responsive to UV light.
UV Exposure: Immediately after ink deposition, the printed area is exposed to high-intensity UV light, typically emitted by UV LEDs or lamps. The UV light penetrates the ink layer, activating the photoinitiators.
Curing Process: The activated photoinitiators initiate a polymerization reaction, causing the ink molecules to cross-link and form a durable, solid film. This process occurs rapidly, often within milliseconds, ensuring high productivity.
Post-Curing (Optional): In some cases, a secondary UV curing step may be employed to further enhance the ink’s adhesion, durability, and resistance to fading or chemicals.
Advantages of UV Curing Technology
1. Speed and Efficiency: UV curing significantly reduces the time required for ink drying compared to conventional methods, such as heat or air drying. This results in faster turnaround times and increased production efficiency.
2. Enhanced Durability: UV-cured inks exhibit exceptional resistance to fading, scratching, and chemicals, ensuring long-lasting prints that can withstand harsh environments.
3. Versatility: The ability to cure inks on a wide variety of substrates makes UV flatbed printers suitable for diverse applications, from promotional signage to industrial product labeling.
4. Environmental Friendliness: UV curing is a solvent-free process, minimizing volatile organic compound (VOC) emissions and reducing the environmental impact associated with traditional printing methods.
5. Cost-Effectiveness: Although UV flatbed printers and UV-curable inks may have higher initial costs, the elimination of plates, reduced waste, and increased production speed contribute to long-term cost savings.
Applications of UV Flatbed Printers
1. Advertising and Signage: UV flatbed printers are extensively used in the production of outdoor and indoor signs, banners, posters, and billboards. The durability of UV-cured inks ensures that these prints remain vibrant and legible even under harsh weather conditions.
2. Decorative Printing: From custom wall coverings to artistic glass panels, UV flatbed printers enable the creation of unique and personalized decorative items for homes, offices, and public spaces.
3. Industrial Manufacturing: In industries such as automotive, aerospace, and electronics, UV flatbed printers are utilized for printing product labels, serial numbers, barcodes, and even functional coatings directly onto components, enhancing traceability and efficiency.
4. Packaging and Labeling: The versatility of UV flatbed printers allows for the direct printing of high-resolution graphics, text, and variable data onto packaging materials, reducing the need for additional labeling steps.
5. Art and Photography: Artists and photographers can reproduce their works on various media, such as canvas, metal, or acrylic, with UV flatbed printers, achieving professional-grade results with excellent color accuracy and detail.
Challenges and Limitations
While UV flatbed printers offer numerous advantages, they also present some challenges:
Initial Investment: The cost of acquiring a UV flatbed printer and the associated UV-curable inks can be substantial, posing a barrier for small businesses.
Substrate Compatibility: Although versatile, not all substrates are suitable for UV printing, and proper surface preparation is often required.
Maintenance: UV lamps and LEDs need periodic replacement, and the printer’s nozzles must be regularly cleaned to maintain optimal performance.
Curing Uniformity: Ensuring uniform UV exposure across the entire print area can be challenging, particularly for large or irregularly shaped objects.
Future Prospects
The continuous evolution of UV curing technology and advancements in printer design are expanding the capabilities and applications of UV flatbed printers. Some future trends to anticipate include:
1. Increased Automation: Integration with automated systems for material handling, ink management, and quality control will further enhance productivity and reduce labor costs.
2. Enhanced Customization: Advances in software and ink formulations will enable even greater levels of personalization, allowing for the creation of unique, one-off prints.
3. New Substrate Compatibility: Ongoing research will lead to the development of UV-curable inks that can be used on previously incompatible materials, broadening the scope of UV printing.
4. Environmental Innovations: Efforts to reduce the environmental footprint of UV printing will continue, with a focus on developing more eco-friendly ink formulations and energy-efficient UV curing systems.
Conclusion
UV flatbed printers, powered by UV curing technology, represent a significant leap forward in the printing industry. They offer unparalleled versatility, efficiency, and durability, enabling the production of high-quality prints on a wide range of substrates. As technology continues to evolve, UV flatbed printers will become even more integral to various industries, driving innovation and enhancing product customization. Despite the initial investment and maintenance considerations, the long-term benefits of UV curing technology make it a compelling choice for businesses seeking to stay at the forefront of printing technology.