UV Flatbed Printer: Applications in the Automotive Industry
UV Flatbed Printer: Applications in the Automotive Industry
The automotive industry has long been a pioneer in adopting innovative technologies to enhance manufacturing processes, improve product quality, and streamline production lines. One such technology that has gained significant traction in recent years is the UV flatbed printer. This article explores the various applications of UV flatbed printers in the automotive industry, highlighting their versatility, efficiency, and the transformative impact they have had on automotive manufacturing and customization.
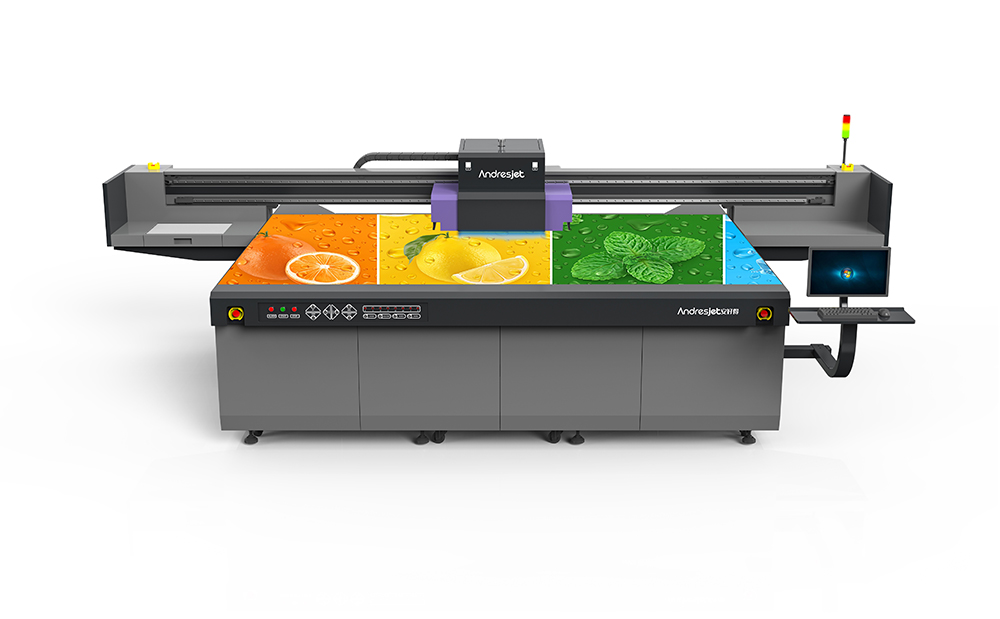
Understanding UV Flatbed Printers
UV flatbed printers are a type of digital printing technology that utilizes ultraviolet (UV) light to cure or dry ink instantly after it is applied to a substrate. This process allows for high-quality, durable prints on a wide range of materials, including plastics, metals, glass, and various composites commonly used in the automotive industry. The key advantages of UV flatbed printers lie in their ability to produce vibrant, detailed prints quickly and efficiently, making them an ideal choice for both prototyping and mass production.
Applications in Automotive Manufacturing
Interior Components Customization
UV flatbed printers have revolutionized the customization of automotive interior components. From dashboard panels to door trims, these printers enable manufacturers to apply intricate designs, logos, or even personalized messages directly onto the surfaces. This not only enhances the aesthetic appeal of the vehicle but also allows for greater flexibility in design iterations, reducing the need for expensive tooling changes associated with traditional manufacturing methods.
Exterior Panel Decoration
The exterior of a vehicle is where UV flatbed printers truly shine. They can print directly onto body panels, spoilers, and other exterior components, allowing for unique graphics, patterns, or even full-color wraps. This technology is particularly popular in the custom automotive sector, where owners seek to distinguish their vehicles through eye-catching visuals. Moreover, it enables automakers to offer limited-edition models with special exterior designs, thereby increasing product differentiation and market appeal.
Functional Printing for Components
Beyond aesthetics, UV flatbed printers are also used for functional printing on automotive components. For instance, they can print conductive inks for touch sensors or capacitive switches, eliminating the need for separate, costly manufacturing processes. Similarly, they can apply UV-resistant inks for components exposed to sunlight, ensuring long-lasting performance and durability.
Prototyping and Design Validation
In the early stages of automotive design, UV flatbed printers facilitate rapid prototyping. Designers can quickly print and test various designs, textures, and finishes on actual material substrates, allowing for real-time design validation and iteration. This accelerates the product development cycle, reduces costs associated with physical prototyping, and enhances the overall efficiency of the design process.
Safety and Regulatory Compliance
UV flatbed printers also play a role in ensuring safety and regulatory compliance in automotive manufacturing. For example, they can print warning labels, serial numbers, or regulatory markings directly onto components, ensuring permanence and legibility. This eliminates the need for adhesive labels, which can wear off or become damaged over time.
Environmental and Economic Benefits
The adoption of UV flatbed printers in the automotive industry also brings environmental and economic benefits. The ink curing process is more energy-efficient than traditional drying methods, reducing carbon emissions. Additionally, the ability to print on demand minimizes waste associated with overproduction and inventory management. From an economic perspective, the reduced setup times, minimal tooling requirements, and the elimination of intermediate steps in the production process contribute to significant cost savings.
Future Trends and Innovations
As technology continues to advance, UV flatbed printers in the automotive industry are poised for further innovation. Ongoing research focuses on developing new ink formulations that enhance durability, scratch resistance, and chemical resistance, making them even more suitable for automotive applications. Furthermore, integration with advanced software solutions, such as 3D printing and CAD design tools, will enable even greater design flexibility and precision.
Another exciting trend is the potential for UV flatbed printers to facilitate on-demand customization in automotive manufacturing. Imagine a future where customers can customize their vehicle’s appearance or interior features in real-time, with the printer seamlessly integrating these designs into the production process. This level of personalization could revolutionize the automotive market, offering consumers a truly unique and tailored driving experience.
Conclusion
UV flatbed printers have proven to be a versatile and transformative technology in the automotive industry. From enhancing aesthetics and functionality to facilitating rapid prototyping and ensuring regulatory compliance, their applications are vast and varied. As technology continues to evolve, the potential for UV flatbed printers to revolutionize automotive manufacturing and customization is boundless. With ongoing innovations in ink formulations, software integration, and manufacturing processes, the future of UV flatbed printing in the automotive industry looks promising, paving the way for more efficient, cost-effective, and sustainable manufacturing practices.