UV Flatbed Printer: Common Mistakes to Avoid During Operation
UV Flatbed Printer: Common Mistakes to Avoid During Operation
UV flatbed printers have revolutionized the printing industry by offering versatility, precision, and speed in producing high-quality prints on a wide range of materials. From signage and displays to decorative and functional items, these printers have become indispensable tools in many workshops and manufacturing facilities. However, like any sophisticated machinery, operating a UV flatbed printer requires attention to detail and adherence to best practices to avoid common mistakes that can compromise print quality, extend production times, or even cause damage to the printer itself. In this article, we will explore some of the most common mistakes to avoid during the operation of a UV flatbed printer and provide tips on how to prevent them.
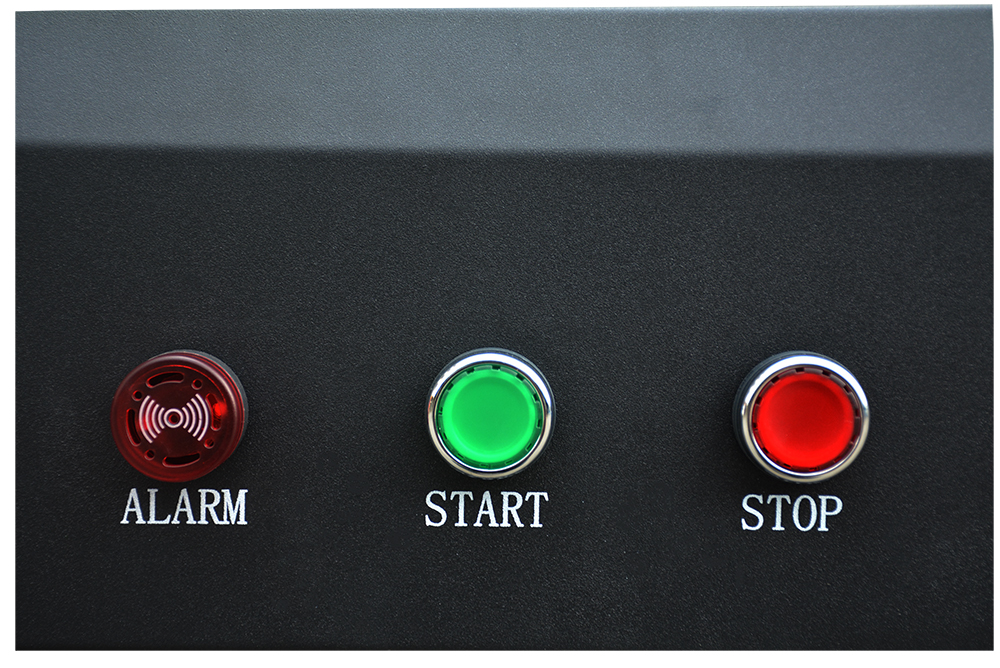
1. Improper Material Handling
Mistake: Neglecting the preparation and handling of print materials.
Impact: Poorly prepared or improperly handled materials can lead to misalignments, jams, and suboptimal print quality.
Prevention Tips:
Proper Cleaning: Ensure that the print surface is clean, free of dust, debris, and grease. Use appropriate cleaning solutions and techniques designed for the specific material you are printing on.
Accurate Measurement: Always measure and cut materials to the exact size required for your print job. Inaccurate dimensions can lead to wasted material and misalignments on the printer bed.
Correct Material Loading: Follow the manufacturer’s instructions for loading materials onto the printer bed. Incorrect loading can cause warping, bubbling, or uneven printing.
2. Incorrect Printer Settings
Mistake: Failing to configure printer settings accurately.
Impact: Incorrect settings can result in print quality issues such as over- or under-exposure, incorrect color output, and layer separation.
Prevention Tips:
Calibration: Regularly calibrate your printer to ensure that it is operating within the manufacturer’s specifications. This includes checking and adjusting the print head height, ensuring the bed is level, and verifying color accuracy.
Software Settings: Carefully review and adjust all relevant settings in your print software, including resolution, layer thickness, exposure time, and color profiles. Always consult the printer’s manual or technical support for guidance on optimal settings for different materials and applications.
Test Prints: Perform test prints using a small portion of your material before committing to a full-scale production run. This allows you to assess print quality and make any necessary adjustments to your settings.
3. Ineffective Print Head Maintenance
Mistake: Neglecting regular print head maintenance.
Impact: Buildup of debris, dried ink, or nozzle clogs can severely impact print quality and printer performance.
Prevention Tips:
Nozzle Cleaning: Regularly perform nozzle cleaning cycles as recommended by the printer manufacturer. This helps to remove any dried ink or debris that may be blocking the nozzles.
Head Wiping: Use appropriate wipes and solutions to clean the print head surface. Avoid using abrasive materials or harsh chemicals that could damage the print head.
Priming and Purging: Perform priming and purging procedures to ensure that ink flow is consistent and free of air bubbles. This is particularly important when switching between different inks or materials.
4. Suboptimal Ink Management
Mistake: Improper handling and storage of ink cartridges and reservoirs.
Impact: Incorrect ink management can lead to premature ink failure, print quality issues, and costly replacements.
Prevention Tips:
Storage Conditions: Store ink cartridges and reservoirs in a cool, dark place to prevent premature degradation. Avoid exposing them to extreme temperatures or direct sunlight.
Regular Rotation: Use ink cartridges and reservoirs on a regular rotation to prevent them from sitting idle for too long. Stagnant ink can develop sediments or dry out, affecting print quality.
Compatible Inks: Always use inks that are compatible with your printer model and the materials you are printing on. Using incompatible inks can damage the print head and void your printer’s warranty.
5. Overlooking Software Updates
Mistake: Failing to install software and firmware updates.
Impact: Missing out on critical bug fixes, performance improvements, and new features can negatively impact your printer’s efficiency and reliability.
Prevention Tips:
Regular Checks: Periodically check for software and firmware updates from the printer manufacturer. This can often be done through the printer’s interface or by visiting the manufacturer’s website.
Installation: Install updates as soon as they are available, following the manufacturer’s instructions carefully. Backup any critical settings or files before performing updates to avoid losing them.
Compatibility: Ensure that the updates are compatible with your printer model and the operating system you are using.
6. Ignoring Safety Protocols
Mistake: Failing to adhere to safety protocols during printer operation.
Impact: Ignoring safety guidelines can lead to accidents, injuries, and printer damage.
Prevention Tips:
Training: Ensure that all operators are trained on the safe use of the UV flatbed printer, including understanding the printer’s components, emergency shutdown procedures, and potential hazards.
Protective Gear: Wear appropriate protective gear, such as gloves, safety glasses, and masks, when handling ink, cleaning the printer, or performing maintenance tasks.
Ventilation: Ensure that the workspace is well-ventilated to minimize exposure to UV radiation and harmful vapors emitted during printing.
7. Inadequate Monitoring and Troubleshooting
Mistake: Failing to monitor printer performance and troubleshoot issues promptly.
Impact: Delays in identifying and addressing printer issues can lead to extensive downtime, wasted materials, and increased costs.
Prevention Tips:
Real-Time Monitoring: Use the printer’s built-in monitoring tools to keep track of performance metrics such as ink levels, print head temperature, and print bed adhesion.
Proactive Troubleshooting: Familiarize yourself with common printer issues and their solutions. This will allow you to troubleshoot and resolve problems quickly without needing to consult technical support every time.
Maintenance Logs: Keep detailed maintenance logs to track the printer’s service history, including any replacements, repairs, or adjustments made. This information can be invaluable when diagnosing recurring issues.
Conclusion
Operating a UV flatbed printer efficiently and effectively requires a combination of careful planning, attention to detail, and adherence to best practices. By avoiding common mistakes such as improper material handling, incorrect printer settings, ineffective print head maintenance, suboptimal ink management, overlooking software updates, ignoring safety protocols, and inadequate monitoring and troubleshooting, you can optimize your printer’s performance, maximize uptime, and produce high-quality prints consistently. Remember, the key to successful UV flatbed printing lies in a commitment to excellence in every aspect of the process. With the right approach, your UV flatbed printer can be a powerful tool for creativity and productivity.