UV Flatbed Printer: Common Printing Challenges and Solutions
UV Flatbed Printer: Common Printing Challenges and Solutions
UV flatbed printers have revolutionized the printing industry, offering versatility, precision, and high-quality outputs on various materials. These printers utilize UV-curable inks that cure instantly when exposed to ultraviolet light, enabling fast and efficient printing processes. However, like any technology, UV flatbed printers also face common challenges that can affect print quality, productivity, and overall performance. This article explores these challenges and provides practical solutions to overcome them.
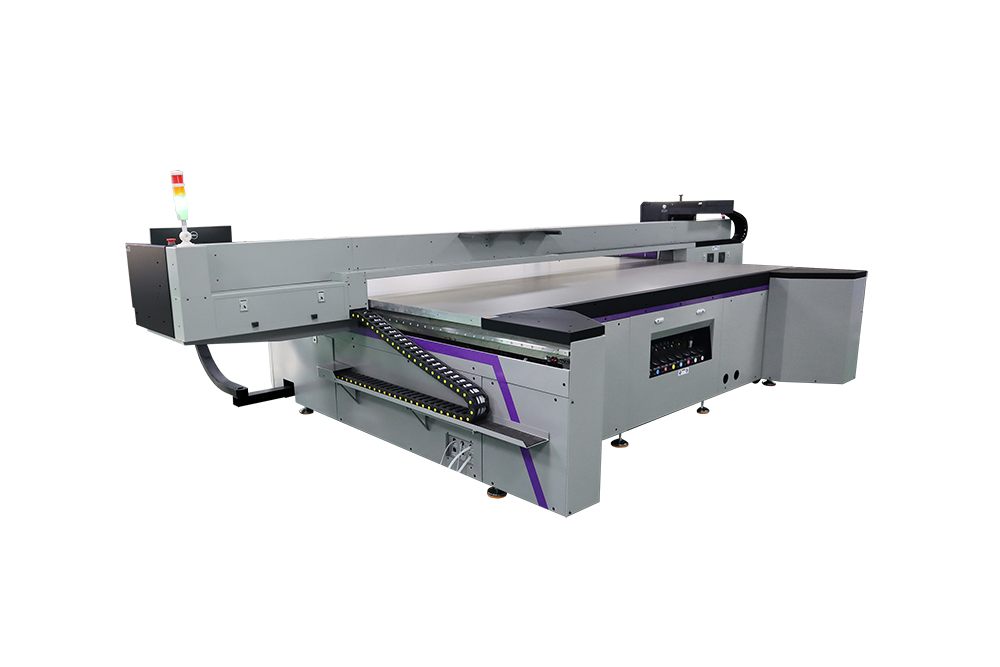
1. Ink Adhesion Issues
One of the primary challenges with UV flatbed printers is ink adhesion, particularly on certain substrates. Insufficient adhesion can lead to poor print quality, smudging, or even complete ink failure. This issue often arises due to incompatible ink formulations, incorrect curing settings, or substrate surface properties.
Solution:
Choose Compatible Inks: Ensure that the inks used are specifically designed for the substrate being printed. Manufacturers often provide guides or test prints to determine ink compatibility.
Adjust Curing Settings: Incorrect curing can result in under- or over-curing, both of which can affect adhesion. Conduct test prints to find the optimal curing time and intensity for each substrate.
Surface Preparation: Properly prepare the substrate surface by cleaning it thoroughly to remove any contaminants that could hinder ink adhesion. Additionally, consider using adhesion promoters for difficult-to-print materials.
2. Print Quality Inconsistencies
Maintaining consistent print quality across large print runs can be challenging, especially when dealing with intricate designs or fine details. Factors such as ink viscosity, printer calibration, and substrate flatness can all contribute to quality inconsistencies.
Solution:
Regular Maintenance: Perform routine maintenance checks, including cleaning printheads and ensuring proper ink flow, to maintain optimal print quality.
Calibration and Profiling: Regularly calibrate the printer and create or update ICC profiles for each substrate to ensure accurate color reproduction and detail retention.
Use of Quality Substrates: Opt for flat and stable substrates to minimize print distortions. For flexible or uneven surfaces, consider using vacuum tables or other flattening devices.
3. Ink Curing Problems
Proper curing is crucial for achieving durable prints, but it can also be a source of challenges. Over-curing can lead to ink cracking or yellowing, while under-curing can result in ink that remains tacky or fails to adhere properly.
Solution:
Curing Tests: Perform curing tests to determine the ideal curing time and intensity for each ink and substrate combination. This ensures that inks are fully cured without causing damage.
Temperature Control: Maintain a consistent temperature in the printing environment, as temperature fluctuations can affect curing efficiency.
UV Lamp Maintenance: Regularly inspect and replace UV lamps as needed to ensure consistent and effective curing.
4. Print Speed and Efficiency
While UV flatbed printers offer fast printing speeds compared to traditional methods, maximizing efficiency can still be a challenge. Slow print speeds, long curing times, and frequent maintenance can all impact productivity.
Solution:
Upgrade Hardware: Consider upgrading to printers with faster print speeds and more efficient curing systems to reduce production time.
Workflow Optimization: Streamline the printing process by organizing print jobs efficiently, minimizing downtime between prints, and automating tasks where possible.
Training and Skill Development: Train operators on best practices for maximizing printer efficiency, including proper ink management, substrate handling, and curing techniques.
5. Environmental Considerations
UV flatbed printers, like any industrial equipment, have environmental implications. The use of UV-curable inks and the energy consumption of the curing process can contribute to waste and carbon emissions.
Solution:
Eco-Friendly Inks: Opt for inks that are formulated to be environmentally friendly, with low VOCs (volatile organic compounds) and minimal hazardous components.
Energy Efficiency: Choose printers with energy-efficient features, such as LED curing systems, and implement energy-saving practices in the printing process.
Proper Waste Disposal: Follow local regulations for the disposal of ink waste, cleaning solutions, and other consumables to minimize environmental impact.
6. Cost Management
The initial investment in a UV flatbed printer, along with ongoing costs for inks, maintenance, and upgrades, can be substantial. Managing these costs while maintaining print quality and productivity is a common challenge.
Solution:
Long-Term Investment: Consider the long-term benefits of UV flatbed printing, including increased versatility, faster production times, and the ability to print on a wide range of substrates.
Cost Analysis: Perform a cost-benefit analysis to determine the most cost-effective ink and substrate combinations for your specific printing needs.
Maintenance Planning: Develop a maintenance schedule to minimize unexpected downtime and repair costs. Regular maintenance can also extend the printer’s lifespan.
In conclusion, UV flatbed printers offer numerous advantages in the printing industry, but they also present challenges that must be addressed to ensure optimal performance. By understanding these challenges and implementing the proposed solutions, printers can overcome obstacles, maintain high print quality, and maximize productivity. As technology continues to advance, it is essential for printers to stay updated on the latest innovations and best practices to fully leverage the capabilities of UV flatbed printing.