UV Flatbed Printer: Common Printing Defects and How to Fix Them
UV Flatbed Printer: Common Printing Defects and How to Fix Them
UV flatbed printers have revolutionized the printing industry by offering versatile and high-quality printing on a wide range of substrates. From rigid materials like glass and metal to flexible ones like vinyl and fabric, these printers have become a staple in many print shops and manufacturing facilities. However, like any other technology, UV flatbed printers are not immune to issues that can affect print quality. In this article, we will discuss some of the most common printing defects encountered with UV flatbed printers and provide practical solutions to fix them.
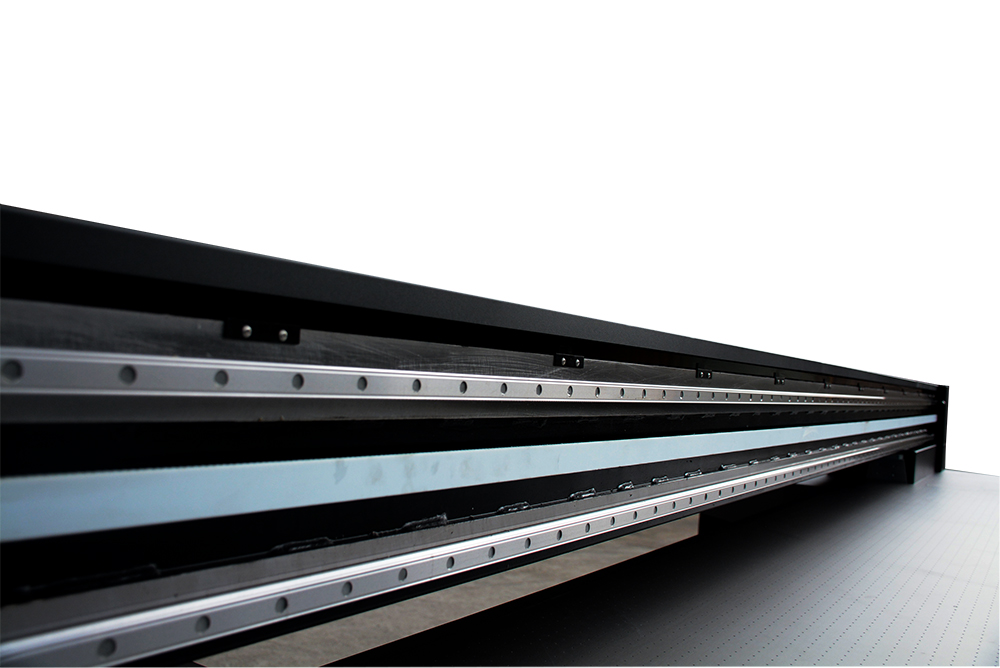
1. Banding
Description:
Banding refers to visible lines or stripes running across the print, perpendicular to the direction of the print head movement. It often occurs due to inconsistent ink deposition or misalignment between print head passes.
Causes:
Inkjet nozzle clogging or malfunction.
Inconsistent ink flow.
Misalignment of the print heads.
Variations in the substrate’s surface.
Solutions:
Nozzle Check and Cleaning: Regularly perform nozzle checks and clean the print heads using the printer’s built-in cleaning functions or manual cleaning methods.
Calibration: Ensure the print heads are properly calibrated. Most UV flatbed printers have automatic calibration features, but manual adjustments may be necessary.
Ink Flow Adjustment: Check the ink supply system for any obstructions or air bubbles. Adjust the ink pressure and flow rates as recommended by the printer manufacturer.
Substrate Preparation: Ensure the substrate is clean, dust-free, and free of any contaminants that could affect ink adhesion.
2. Blurring or Smearing
Description:
Blurring or smearing occurs when the ink bleeds or spreads uncontrollably on the substrate, resulting in a loss of detail and sharpness.
Causes:
Excessive ink application.
Ink not drying properly due to insufficient UV curing.
Incorrect print head height or angle.
Substrate absorbing too much ink.
Solutions:
Adjust Ink Settings: Reduce the ink density or volume in the printer settings.
UV Curing: Ensure the UV lamps are functioning correctly and are providing adequate curing. Adjust the curing time and intensity as needed.
Print Head Adjustment: Adjust the print head height and angle to ensure proper ink deposition without causing excessive spreading.
Substrate Selection: Choose substrates that are compatible with the ink type and have the right absorbency properties.
3. Color Inconsistency
Description:
Color inconsistency refers to variations in color across the print or between different prints.
Causes:
Ink mixing issues.
Inconsistent ink supply.
Variations in UV curing.
Color profile mismatches.
Solutions:
Ink Mixing: Ensure inks are properly mixed and stored according to the manufacturer’s guidelines. Avoid using expired or improperly stored inks.
Ink Supply: Check for any obstructions or inconsistencies in the ink supply system. Replace any faulty ink cartridges or tanks.
Color Calibration: Regularly calibrate the printer’s color settings using color targets and profiling software.
UV Curing Consistency: Ensure the UV lamps are evenly distributed and providing consistent curing across the entire print area.
4. Print Head Strikes
Description:
Print head strikes occur when the print head physically touches the substrate or other parts of the printer, causing damage to the print head or the substrate.
Causes:
Incorrect print head height adjustment.
Misalignment of the substrate or printer components.
Obstacles in the print path.
Solutions:
Height Adjustment: Carefully adjust the print head height to ensure it does not touch the substrate. Use the printer’s automatic or manual adjustment features.
Alignment Checks: Regularly check the alignment of the substrate, print bed, and other printer components.
Clear Print Path: Ensure the print path is clear of any obstacles, such as clips, tape, or debris.
5. Adhesion Issues
Description:
Adhesion issues refer to the ink not properly adhering to the substrate, resulting in peeling, flaking, or complete detachment.
Causes:
Incompatible ink-substrate combination.
Insufficient UV curing.
Contaminated or improperly prepared substrate.
Solutions:
Ink-Substrate Compatibility: Check the ink manufacturer’s recommendations for compatible substrates. Use adhesion promoters or primers if necessary.
UV Curing: Ensure the UV curing process is adequate for the ink and substrate combination. Adjust the curing time and intensity as needed.
Substrate Preparation: Properly clean and prepare the substrate to remove any contaminants that could affect adhesion. Follow the substrate manufacturer’s guidelines for preparation and handling.
6. Orange Peel Effect
Description:
The orange peel effect refers to a textured surface finish that resembles the skin of an orange. It is caused by uneven ink deposition and curing.
Causes:
Incorrect ink viscosity.
Inconsistent UV curing.
Substrate surface irregularities.
Solutions:
Ink Viscosity: Adjust the ink viscosity to ensure proper flow and deposition. Consult the ink manufacturer for the recommended viscosity range.
UV Curing: Optimize the UV curing process to ensure even curing across the print. Use multiple UV lamps or adjust the lamp intensity and position.
Substrate Surface: Ensure the substrate surface is smooth and even. Use sanding or polishing techniques if necessary to achieve a smooth finish.
7. Ghosting
Description:
Ghosting refers to a faint, double image or shadow appearing on the print, typically offset from the main image.
Causes:
Misalignment of the print heads.
Ink bleeding or spreading during the printing process.
Mechanical issues with the printer’s movement system.
Solutions:
Print Head Alignment: Perform a thorough print head alignment to ensure proper positioning.
Ink Bleeding: Adjust the ink settings to reduce bleeding or spreading. Increase the drying or curing time between print head passes.
Mechanical Checks: Inspect the printer’s movement system for any worn or damaged parts. Replace or repair as necessary to ensure smooth and accurate movement.
UV flatbed printers offer a wide range of benefits and capabilities, but they are not without their challenges. By understanding the common printing defects and their causes, you can take proactive steps to prevent and fix these issues. Regular maintenance, proper ink and substrate selection, and careful adjustment of printer settings are key to achieving high-quality prints. Remember to consult your printer’s manual and the ink manufacturer’s guidelines for specific recommendations and troubleshooting steps. With the right knowledge and tools, you can optimize your UV flatbed printer’s performance and produce outstanding prints every time.