UV Flatbed Printer: Common Printing Mistakes and How to Avoid Them
UV flatbed printers have revolutionized the way businesses approach custom printing projects. Whether you’re creating vibrant signage, eye-catching displays, or personalized merchandise, these machines offer unparalleled versatility and efficiency. However, like any technology, they’re not immune to user errors. Missteps during setup, operation, or maintenance can lead to subpar results, wasted materials, and even machine damage. In this blog, we’ll explore the most common UV flatbed printing mistakes and provide actionable tips to help you avoid them.
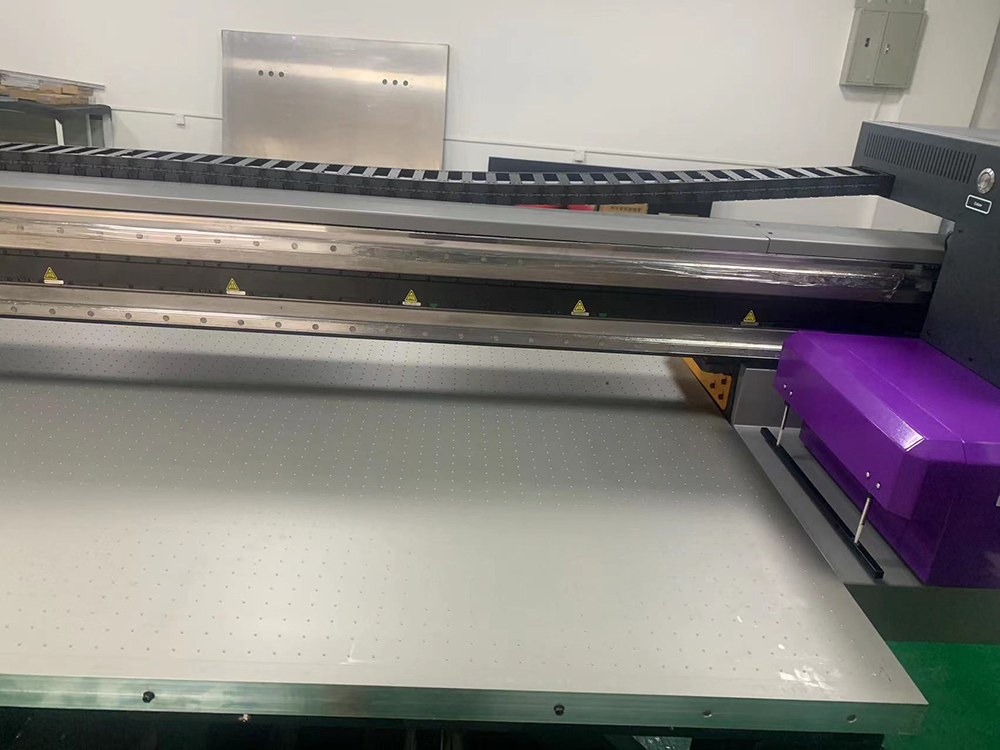
Neglecting Proper Maintenance
One of the biggest pitfalls for UV flatbed printer users is skipping routine maintenance. These machines rely on precise components, such as print heads, UV lamps, and conveyor systems, to function optimally. Neglecting cleaning, calibration, or part replacements can cause clogs, misalignments, or inconsistent ink flow.
To prevent this, establish a regular maintenance schedule. Clean print heads daily using manufacturer-recommended solutions, and check ink levels and viscosity regularly. Replace UV lamps every 1.000–2.000 hours (or as advised) to ensure proper curing. Lastly, inspect conveyor belts and vacuum tables for debris that could disrupt material placement.
Ignoring Material Preparation Guidelines
UV flatbed printers excel at printing on diverse substrates—acrylic, wood, glass, metal, and more. However, each material has unique properties that affect ink adhesion and drying times. Ignoring these guidelines can lead to peeling, smudging, or uneven prints.
Always pre-treat materials as needed. For example, porous surfaces like wood may require a primer to enhance ink absorption, while glossy acrylic might benefit from a surface wipe to remove oils or contaminants. Check the manufacturer’s manual for recommended temperatures, humidity levels, and material thickness limits. Testing a small sample before a full print run can save time and materials.
Overlooking Color Management Settings
Color accuracy is critical in commercial printing, yet many users overlook the importance of color management. Misconfigured settings can result in dull, oversaturated, or mismatched hues, especially when printing on reflective or transparent substrates.
Start by calibrating your monitor and printer using a colorimeter or spectrophotometer. Use ICC profiles tailored to your specific material and ink type. If printing spot colors (e.g., Pantone), verify their compatibility with your UV ink set. Finally, conduct a color test print to compare digital proofs with physical results, adjusting settings as needed.
Underestimating Curing Time and Temperature
UV curing is the process by which ink hardens under ultraviolet light. While it’s tempting to rush this step for faster production, insufficient curing can lead to fragile prints that scratch easily or fade over time. Conversely, over-curing can cause brittleness or warping, especially on heat-sensitive materials.
Follow the ink manufacturer’s recommendations for curing time and intensity. Use a UV power meter to ensure your lamps emit the correct wavelength and intensity. If printing on thick or heat-sensitive substrates, consider using low-heat lamps or implementing a cooling system. Always allow prints to cool completely before handling.
Overloading the Print Bed
UV flatbed printers are designed for efficiency, but overloading the print bed with too many items can backfire. Crowded workspaces increase the risk of collisions between the print head and materials, leading to costly damage. Additionally, uneven spacing can cause inconsistent ink distribution or curing.
Organize your print bed strategically. Leave adequate gaps between items to allow the print head to move freely. Use jigs or registration pins to align materials precisely. If printing multiple items, consider batching them by size or shape to minimize head movement.
Skipping Test Prints
In the rush to meet deadlines, many users skip test prints, assuming their design will translate perfectly to the final product. This risky approach often results in wasted materials and missed opportunities for adjustments.
Always run a test print before a full production run. Check for registration accuracy, color balance, and ink adhesion. If printing large-format graphics, use a smaller section of the design to verify alignment and scaling. Document any changes made during testing to streamline future projects.
Conclusion
UV flatbed printers are powerful tools for unlocking creative possibilities, but they require careful attention to detail. By avoiding common mistakes—such as neglecting maintenance, ignoring material guidelines, or skipping test prints—you can maximize efficiency, reduce waste, and achieve stunning results. Remember, prevention is key: invest time in setup, calibration, and training, and don’t hesitate to consult your manufacturer’s resources or support team when in doubt.