UV Flatbed Printer: Factors Affecting Ink Adhesion and Durability
UV Flatbed Printer: Factors Affecting Ink Adhesion and Durability
UV flatbed printers have revolutionized the printing industry, offering versatile and high-quality prints on a wide range of substrates. These printers utilize ultraviolet (UV) light to cure the inks almost instantly, providing fast turnaround times and durable prints. However, achieving optimal ink adhesion and durability can be challenging and is influenced by several factors. This article delves into the critical aspects that affect ink adhesion and durability in UV flatbed printers, exploring substrate properties, ink characteristics, printing parameters, and post-printing practices.
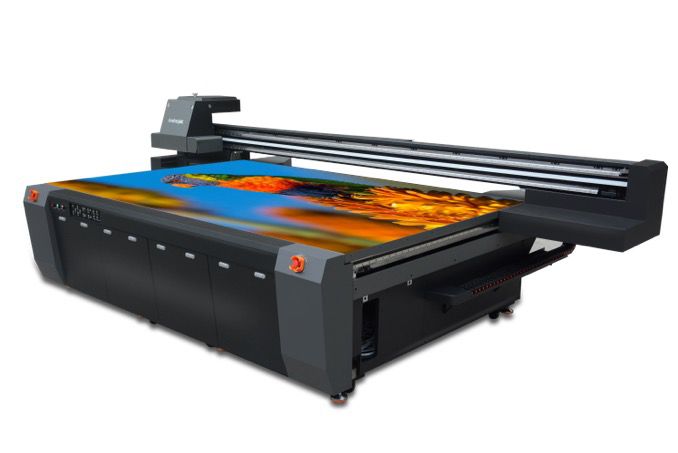
1. Substrate Properties
The choice of substrate plays a pivotal role in determining ink adhesion and durability. Different materials have unique surface properties that can significantly influence how well the UV ink adheres and how long it lasts.
1.1 Surface Energy
Surface energy, or surface tension, is a critical factor. For effective ink adhesion, the surface energy of the substrate should be higher than that of the ink. If the substrate’s surface energy is too low, the ink may not wet out properly, leading to poor adhesion and potential delamination. Substrates like metals and glass typically have high surface energies, favoring good ink adhesion. In contrast, plastics and some coated papers may require pre-treatment to increase their surface energy.
1.2 Porosity and Absorbency
Porosity and absorbency of the substrate also impact ink adhesion. Porous materials, such as uncoated papers or textiles, allow the ink to penetrate deeper, which can enhance adhesion but may reduce surface durability. Non-porous substrates, like plastics or metals, do not absorb ink, requiring proper adhesion through chemical bonding or mechanical means.
1.3 Substrate Cleanliness
Contaminants such as dust, oil, or moisture on the substrate surface can act as barriers between the ink and the material, leading to poor adhesion. Therefore, ensuring the substrate is clean and free from any contaminants is crucial for achieving optimal ink adhesion.
1.4 Substrate Compatibility
Not all UV inks are compatible with every substrate. For instance, some inks may not cure properly on certain plastics due to chemical incompatibility. It is essential to choose inks specifically formulated for the type of substrate being printed to ensure both adhesion and durability.
2. Ink Characteristics
The properties of the UV ink itself are also significant factors affecting adhesion and durability.
2.1 Ink Viscosity
Viscosity refers to the ink’s thickness or flow characteristics. An ink with too high a viscosity may not spread evenly on the substrate, leading to poor adhesion. Conversely, an ink with too low a viscosity may run or bleed, causing loss of detail and reduced durability. Adjusting the ink’s viscosity to the optimal range for the specific substrate and printing conditions is crucial.
2.2 Pigment and Binder Quality
The quality of pigments and binders in the ink affects both color vibrancy and adhesion. High-quality pigments ensure better lightfastness and color stability over time. Binders are responsible for adhering the pigments to the substrate. A well-formulated ink with high-quality binders will exhibit better adhesion and durability.
2.3 Cure Characteristics
UV inks are formulated to cure rapidly under UV light. However, the cure speed and efficiency can vary. Inks that cure too quickly may not allow sufficient time for proper adhesion, while inks that cure too slowly can remain tacky and susceptible to damage. Ensuring the ink’s cure characteristics match the printing conditions and substrate is vital.
3. Printing Parameters
The settings and conditions during the printing process also play a critical role in ink adhesion and durability.
3.1 Ink Deposit Thickness
The thickness of the ink deposit affects both the cure and the adhesion. A thicker ink deposit may require longer exposure to UV light for complete curing. It can also lead to increased shrinkage and potential cracking of the ink film. Controlling the ink deposit thickness through proper printer settings is essential for achieving a balance between coverage and durability.
3.2 UV Cure Intensity and Duration
The intensity and duration of UV light exposure are crucial for proper ink curing. Insufficient UV exposure can result in incomplete curing, leading to poor adhesion and reduced durability. On the other hand, excessive UV exposure can cause over-curing, which may lead to ink brittleness and cracking. Optimizing the UV cure parameters for each ink and substrate combination is necessary.
3.3 Printing Speed and Resolution
The printing speed and resolution can indirectly affect ink adhesion. Higher printing speeds may limit the time available for the ink to wet out and adhere properly to the substrate. Higher resolutions typically require thinner ink layers, which may cure more effectively but could also impact adhesion if not managed correctly.
3.4 Print Head Distance
The distance between the print head and the substrate influences ink deposition. If the print head is too far, the ink droplets may scatter, reducing precision and adhesion. If it’s too close, the ink may be deposited in excess, causing cure issues. Maintaining an optimal print head distance ensures precise ink deposition and good adhesion.
4. Post-Printing Practices
The steps taken after printing can also impact the final adhesion and durability of the ink.
4.1 Post-Cure Treatment
In some cases, an additional post-cure treatment with UV light can enhance ink durability. This step ensures complete curing and cross-linking of the ink, improving its resistance to chemicals, abrasion, and environmental factors.
4.2 Handling and Storage
Proper handling and storage of the printed materials are crucial. Immediately after printing, the inks may still be sensitive to physical disturbances. Care should be taken to avoid scratching, rubbing, or exposing the prints to extreme temperatures or chemicals until the inks are fully stabilized.
4.3 Lamination and Coating
Applying a protective lamination or coating can significantly enhance the durability of the prints. Laminates can provide a barrier against UV light, moisture, and abrasion, extending the lifespan of the prints.
4.4 Cleaning and Maintenance
Regular cleaning and maintenance of the UV flatbed printer ensure consistent print quality and ink adhesion. Build-up of ink residues or contaminants on the print heads or curing lamps can affect performance and durability.
Conclusion
Achieving optimal ink adhesion and durability in UV flatbed printing involves a careful balance of substrate properties, ink characteristics, printing parameters, and post-printing practices. Each factor plays a critical role and must be considered and optimized to ensure high-quality, long-lasting prints.
By understanding and controlling these variables, printers can produce vibrant, durable prints on a wide range of substrates, meeting the diverse needs of the market and ensuring customer satisfaction. Continuous research and development in UV ink formulations, printing technologies, and post-printing treatments will further enhance the capabilities and durability of UV flatbed prints in the future.