UV Flatbed Printer: Factors Affecting Ink Adhesion on Different Materials
UV Flatbed Printer: Factors Affecting Ink Adhesion on Different Materials
In the realm of digital printing, UV flatbed printers have revolutionized the way images and text are applied to a wide variety of substrates. These versatile machines utilize ultraviolet (UV) light to cure inks instantly, offering numerous advantages such as quick drying, enhanced durability, and the ability to print on diverse materials. However, achieving optimal ink adhesion on different surfaces is a complex process influenced by multiple factors. This article delves into the intricacies of ink adhesion in UV flatbed printing, exploring the key variables that determine the success of a print job across various materials.
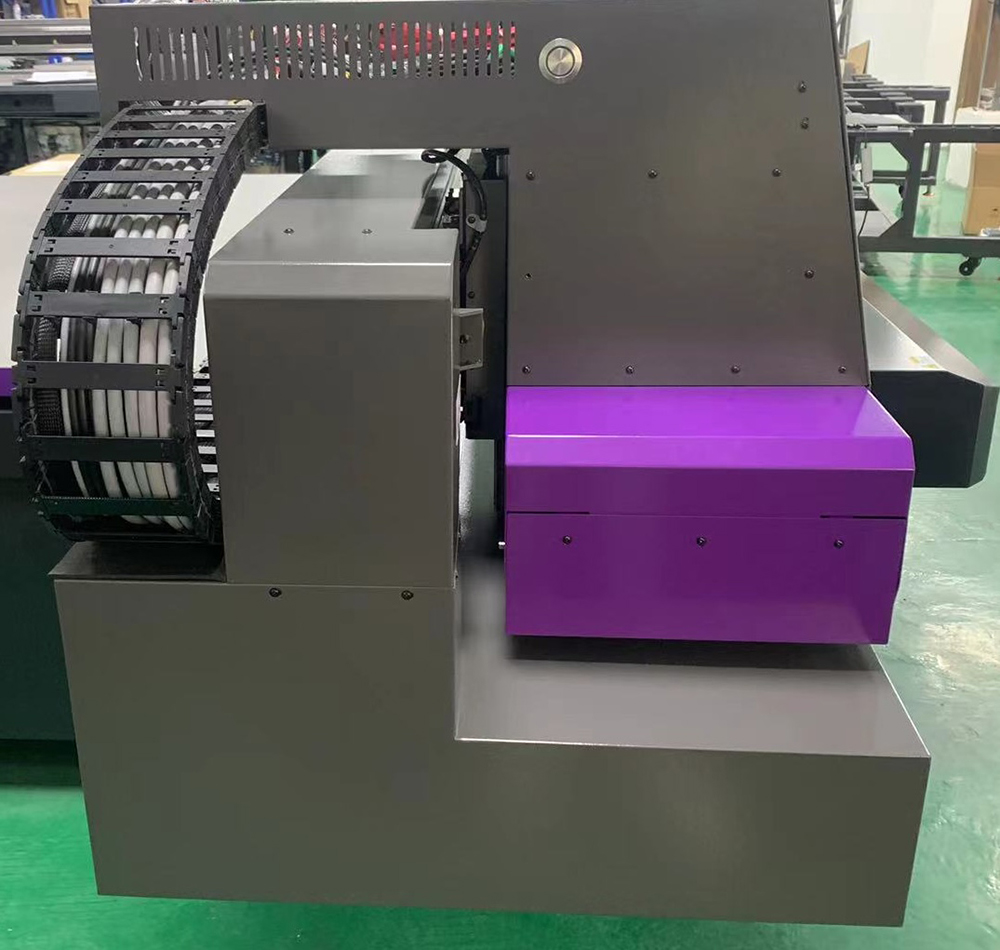
Understanding Ink Adhesion
Ink adhesion refers to the ability of the ink to bond securely to the surface of the material being printed. It is crucial for ensuring the longevity and quality of the print, as poor adhesion can lead to issues such as fading, cracking, or even complete detachment of the ink from the substrate. The process of ink adhesion involves both physical and chemical interactions between the ink, the substrate, and the printing conditions.
Factors Affecting Ink Adhesion
1. Substrate Composition and Properties
The composition of the material plays a pivotal role in ink adhesion. Materials can be broadly classified into absorbent and non-absorbent categories.
- Absorbent Materials: These include papers, fabrics, and some types of plastics that allow the ink to penetrate slightly into the surface. Absorbent materials often provide better ink adhesion due to mechanical bonding and absorption of the ink into the substrate’s pores.
- Non-Absorbent Materials: Materials like metals, glass, and certain plastics do not absorb ink. Achieving good adhesion on these surfaces requires a different approach, typically involving chemical bonding or the use of specialty inks and primers that create a compatible layer for the ink to adhere to.
The surface energy of the substrate is another critical factor. High surface energy materials, such as metals and glasses, generally provide better adhesion as they attract and hold the ink more effectively. Conversely, low surface energy materials like some plastics may require pre-treatment to increase their surface energy.
2. Ink Chemistry and Composition
The chemistry of the UV ink significantly impacts its adhesion properties. UV inks are formulated with specific resins, pigments, and additives that influence their curing behavior and adhesion characteristics.
- Resin Type: The resin component of the ink acts as the binder, adhering the pigment particles to the substrate. Different resins have varying levels of flexibility, hardness, and adhesion strength. Epoxy-based resins, for example, offer excellent adhesion to metals, while polyurethane-based resins might be better suited for flexible materials.
- Pigment Dispersion: The quality of pigment dispersion affects the ink’s ability to form a uniform film on the substrate. Well-dispersed pigments ensure even coverage and better adhesion.
- Additives: Additives such as flow agents, wetting agents, and adhesion promoters are included in ink formulations to enhance specific properties. These can adjust the ink’s viscosity, improve wetting of the substrate, and increase adhesion strength.
3. Printing Parameters
The settings and conditions during the printing process also play a crucial role in ink adhesion.
- Ink Layer Thickness: The thickness of the ink layer can affect adhesion. Too thin a layer may not provide enough material to form a strong bond, while too thick a layer can lead to incomplete curing and reduced adhesion.
- Curing Conditions: UV inks require proper exposure to UV light to cure correctly. Insufficient curing can result in weak adhesion, while overexposure can cause the ink to become too brittle and potentially crack. Factors such as the intensity of the UV light, the duration of exposure, and the distance between the UV lamp and the substrate must be carefully controlled.
- Temperature and Humidity: The ambient temperature and humidity during printing can influence ink adhesion. High humidity can cause condensation on the substrate, affecting ink spreading and adhesion. Temperature fluctuations can alter the viscosity of the ink and the curing process.
4. Surface Preparation and Pre-Treatment
Proper surface preparation is often necessary to ensure optimal ink adhesion, especially for non-absorbent materials.
- Cleaning: The substrate must be thoroughly cleaned to remove any contaminants such as oils, dust, or grease that could interfere with ink adhesion.
- Priming: Applying a primer to the surface can create a more compatible layer for the ink to adhere to. Primers are particularly useful for low surface energy materials, providing a higher energy surface for better ink wetting and adhesion.
- Texturing: In some cases, altering the surface texture of the substrate can improve ink adhesion. Roughening the surface slightly can increase the surface area available for the ink to bond to.
5. Post-Printing Handling and Care
The way the printed material is handled after printing can also impact ink adhesion.
- Drying and Curing: Ensuring the ink is fully cured and dried before further handling is essential. Incomplete curing can lead to smudging or poor adhesion.
- Protection: Applying a protective layer, such as a clear coat or laminate, can enhance the durability of the print and protect the ink from environmental factors that could degrade adhesion over time.
- Storage Conditions: Storing printed materials in appropriate conditions (e.g., avoiding extreme temperatures and humidity) can help maintain good ink adhesion and print quality.
Achieving optimal ink adhesion in UV flatbed printing is a multifaceted challenge that requires careful consideration of the substrate properties, ink chemistry, printing parameters, surface preparation, and post-printing care. Each of these factors interacts in complex ways to influence the final outcome of the print. By understanding and controlling these variables, printers can ensure high-quality, durable prints on a wide range of materials.
The success of a UV flatbed printing project ultimately hinges on the ability to tailor the printing process to the specific requirements of the substrate and the desired print characteristics. Whether working with absorbent or non-absorbent materials, the key is to create the right conditions for the ink to bond securely and remain adhered over time. As technology continues to advance, so too will the methods and materials available to improve ink adhesion, opening up even more possibilities for creative and effective digital printing.