UV Flatbed Printer: Factors Affecting Print Speed
UV flatbed printers have revolutionized the printing industry by offering high-quality, durable prints on a wide range of materials. These printers use ultraviolet light to cure ink instantly, allowing for fast production and versatile applications. However, achieving optimal print speed while maintaining quality is a challenge. Several factors influence the print speed of UV flatbed printers, and understanding these can help businesses maximize efficiency and productivity.
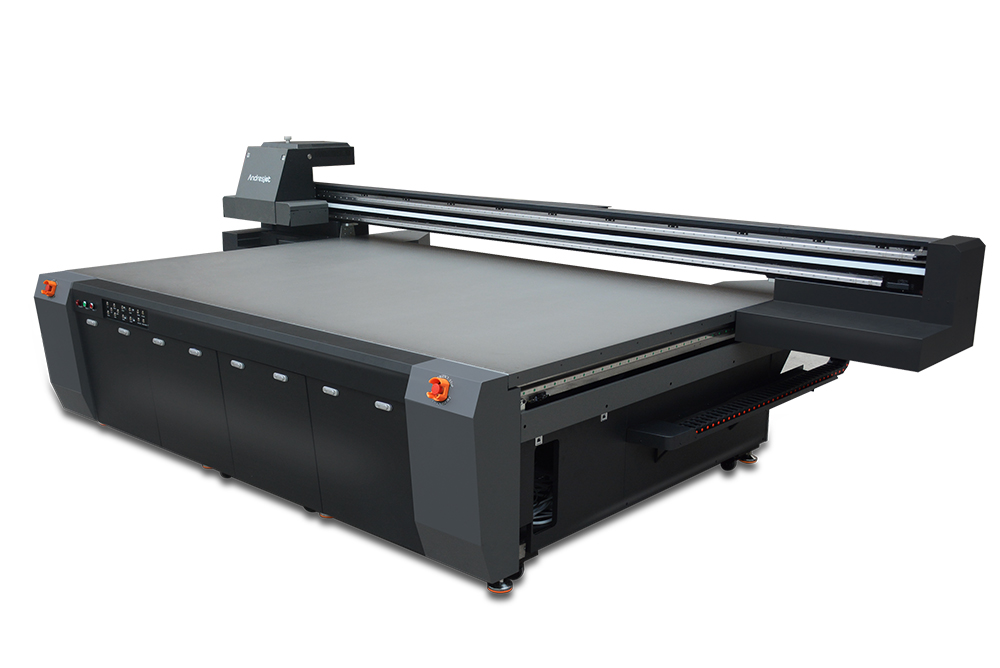
Ink Type and Viscosity
The choice of ink plays a crucial role in determining print speed. UV inks come in various formulations, each designed for specific applications. The viscosity of the ink—its thickness or resistance to flow—directly affects how quickly it can be applied to the substrate. Higher viscosity inks may require more time to settle and cure, slowing down the overall printing process. Conversely, low-viscosity inks can flow more easily, enabling faster print speeds but potentially compromising opacity or durability. Manufacturers often balance these factors by offering inks tailored to different print speeds and material types. Users should select inks that align with their desired output quality and production goals.
Printhead Configuration and Technology
The printhead is the heart of any UV flatbed printer, responsible for depositing ink onto the substrate. Modern printheads utilize advanced technologies such as piezoelectric or thermal mechanisms to control ink ejection. The number of printheads, their arrangement, and nozzle density all impact print speed. A printer with multiple printheads can cover larger areas in a single pass, significantly boosting speed. However, increased printhead complexity may also require more precise calibration and maintenance to prevent issues like clogging or misalignment. Innovations in printhead technology, such as variable droplet size and faster firing rates, continue to push the boundaries of print speed without sacrificing quality.
Resolution and Image Complexity
Print resolution—measured in dots per inch (DPI)—determines the level of detail in the final print. Higher resolutions produce sharper images but require more ink and time to print. For instance, a 600 DPI print will take longer than a 300 DPI print due to the increased number of ink droplets deposited. Image complexity also affects speed. Simple designs with large solid areas print faster than intricate patterns with fine lines or gradients. Balancing resolution and complexity with production needs is essential. Businesses may choose lower resolutions for less critical applications or use multi-pass printing for high-detail jobs, optimizing speed and quality as required.
Substrate Material and Surface Texture
The material being printed on—known as the substrate—plays a significant role in print speed. UV flatbed printers can handle diverse substrates, including wood, glass, metal, and plastics. However, the surface texture and absorbency of these materials vary widely. Rough or porous substrates may require more ink to achieve uniform coverage, slowing down the printing process. Conversely, smooth, non-porous surfaces like glass or metal allow for faster printing with less ink usage. Pre-treating substrates with primers or coatings can improve ink adhesion and reduce drying time, further enhancing speed. Understanding the properties of different substrates and their impact on print speed is vital for efficient production.
Machine Maintenance and Cleanliness
Regular maintenance is critical for ensuring optimal print speed and quality. UV flatbed printers are complex machines with numerous moving parts and sensitive components. Dust, debris, or dried ink can accumulate in printheads, nozzles, or other critical areas, causing clogs, misfires, or reduced speed. Routine cleaning of printheads, curing lamps, and conveyor systems prevents these issues and extends the lifespan of the printer. Additionally, checking and replacing worn-out parts, such as belts, rollers, or dampers, ensures smooth operation. Scheduled maintenance schedules provided by manufacturers should be followed to keep the printer in peak condition.
Software and RIP Optimization
The software used to control the printer—often referred to as a Raster Image Processor (RIP)—plays a pivotal role in print speed. RIP software translates digital files into print-ready data, optimizing ink usage, color management, and print paths. Advanced RIPs offer features like variable data printing, nesting (arranging multiple images efficiently on a sheet), and automated color calibration, all of which can streamline the printing process. Upgrading to the latest RIP versions or customizing settings for specific job types can lead to significant speed improvements without compromising quality.
Conclusion: Balancing Speed and Quality
Achieving the ideal print speed in UV flatbed printers requires a holistic approach that considers ink type, printhead technology, resolution, substrate properties, maintenance, and software optimization. While faster speeds are desirable, they must not come at the expense of print quality or machine reliability. Businesses should evaluate their specific needs—whether it’s high-volume production, premium quality, or a mix of both—and select a printer and workflow that aligns with these goals. Regular monitoring, calibration, and adjustments ensure that the printer operates efficiently, delivering consistent results over time.
In conclusion, UV flatbed printers offer unparalleled versatility and quality, but maximizing print speed demands careful consideration of various factors. By understanding and optimizing these elements, users can unlock the full potential of their printers, achieving faster production cycles and greater profitability in a competitive market.