UV Flatbed Printer: Factors Affecting Print Speed and Efficiency
UV Flatbed Printer: Factors Affecting Print Speed and Efficiency
UV flatbed printers have revolutionized the printing industry with their capability to print on a wide range of substrates including rigid materials like wood, glass, metal, and plastics. These versatile machines utilize UV-curable inks that are instantly cured by UV lights, enabling fast turnaround times and high-quality prints. However, the print speed and overall efficiency of UV flatbed printers can be influenced by several factors. Understanding these factors is crucial for optimizing printer performance and achieving the best possible outcomes. In this article, we will explore the various elements that affect the print speed and efficiency of UV flatbed printers.
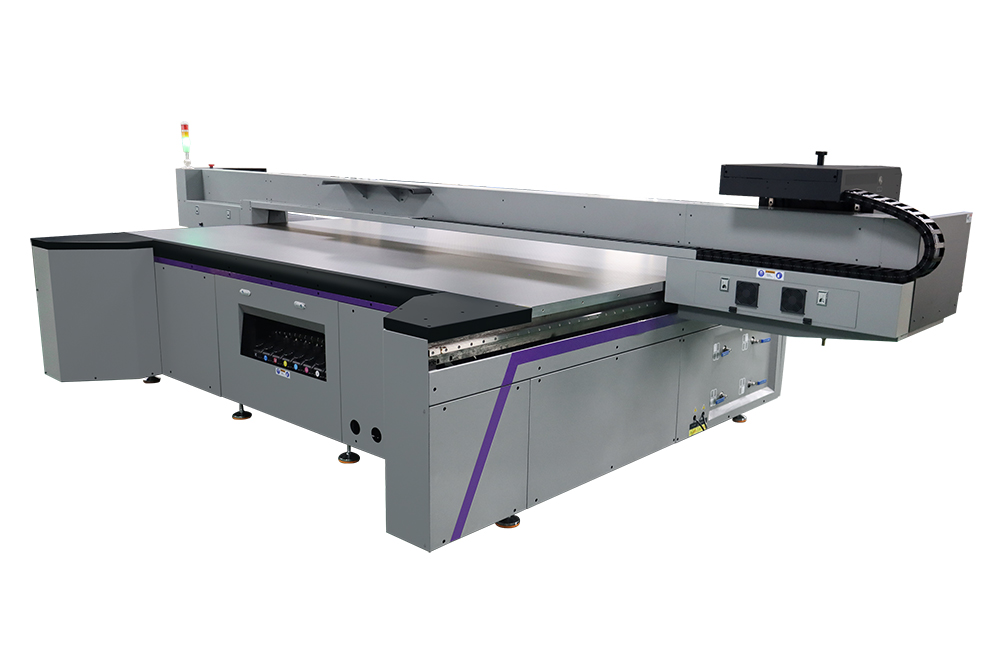
1. Printer Model and Specifications
The first and foremost factor impacting the print speed and efficiency of a UV flatbed printer is the printer model and its specifications. Different models come with varying print speeds, resolution capabilities, and ink systems. High-end models typically offer faster print speeds and more advanced features such as automatic bed cleaning systems, which can significantly enhance efficiency.
1.1 Print Speed Specifications
Manufacturers usually specify the maximum print speed of their machines in square meters per hour (m²/h) or square feet per hour (ft²/h). However, it’s important to note that these specifications are often achieved under optimal conditions and may vary in real-world scenarios due to factors such as ink coverage, media type, and image complexity.
1.2 Ink System
The type of ink system employed by the printer also plays a crucial role. Some UV flatbed printers use a continuous ink supply system (CISS), while others may utilize cartridges. CISS systems are generally more efficient as they reduce the frequency of ink replenishment, minimizing downtime.
2. Ink Characteristics and Curing Process
The properties of UV-curable inks and the curing process directly affect both the speed and quality of prints.
2.1 Viscosity and Flow Rate
The viscosity of the ink can impact how quickly it is dispensed onto the substrate. Inks with lower viscosity tend to flow more easily, potentially allowing for faster print speeds. However, the ink must also have the right flow rate to ensure proper coverage and avoid issues like over-inking or ink starvation.
2.2 Curing Time
UV-curable inks require exposure to UV light to solidify on the substrate. The curing time can vary depending on the ink type, the intensity of the UV lamps, and the thickness of the ink layer. Faster curing times can dramatically increase overall print speed, but insufficient curing can lead to poor print quality and adhesion issues.
2.3 Lamp Power and Configuration
The power and configuration of the UV lamps are critical. Higher power lamps can cure inks more quickly, but they also generate more heat, which must be managed effectively to avoid warping or damaging the substrate. Additionally, the arrangement of the lamps can affect the uniformity of the cure, impacting both speed and quality.
3. Substrate Properties
The type and properties of the substrate being printed on significantly influence the printer’s performance.
3.1 Material Composition
Different materials absorb UV light at varying rates. For example, darker or more absorbent materials may require longer curing times to ensure the ink is fully set. Materials with reflective surfaces, such as metals, can also pose challenges by reflecting the UV light away from the ink.
3.2 Substrate Thickness and Flatness
Thicker or uneven substrates may require adjustments in the print settings, such as increased curing times or modified bed leveling, to ensure proper ink application and curing. This can affect both the speed and the quality of the print.
3.3 Pretreatment Requirements
Some substrates may need pretreatment, such as cleaning or the application of a primer, to ensure proper ink adhesion. These additional steps can add time to the overall printing process but are essential for achieving high-quality results.
4. Print Job Complexity
The complexity of the print job, including factors like ink coverage, color usage, and image resolution, can greatly impact the print speed and efficiency.
4.1 Ink Coverage
Print jobs with high ink coverage generally take longer to print and cure than those with lower coverage. This is because more ink needs to be dispensed and cured, which can increase both the printing and the curing times.
4.2 Color Usage and Layering
The use of multiple colors and layering of inks can also slow down the printing process. Each additional color or layer requires separate passes, increasing the total print time.
4.3 Resolution
While higher resolution prints may offer superior image quality, they also require more data processing and more precise ink placement, which can reduce print speed.
5. Operator Skill and Workflow Management
The expertise of the operator and the efficiency of the workflow can also play a significant role in the overall productivity of the UV flatbed printer.
5.1 Operator Skill
A skilled operator can optimize print settings, manage ink and substrate handling efficiently, and troubleshoot issues promptly, all of which contribute to faster turnaround times.
5.2 Workflow Management
Efficient workflow management, including proper job scheduling, timely ink and substrate replenishment, and regular maintenance, can minimize downtime and keep the printer operating at optimal capacity.
5.3 Software Proficiency
Proficiency with the printer’s software, including RIP (Raster Image Processor) software, can also enhance efficiency. Proper use of RIP software ensures that print jobs are processed quickly and accurately, reducing the likelihood of errors that could lead to reprints.
6. Maintenance and Upkeep
Regular maintenance and upkeep of the UV flatbed printer are essential for maintaining its speed and efficiency over time.
6.1 Cleaning
Regular cleaning of the print heads, UV lamps, and other components ensures that the printer operates smoothly and reduces the risk of clogging or other issues that could slow down the printing process.
6.2 Calibration
Periodic calibration of the printer ensures that it maintains accurate ink deposition and color matching, which not only improves print quality but also reduces waste due to reprints.
6.3 Upgrades and Repairs
Timely repairs and upgrades can prevent minor issues from escalating into major problems that could cause significant downtime. Manufacturers often release software updates that can improve printer performance or add new features.
In conclusion, the print speed and efficiency of a UV flatbed printer are influenced by a variety of factors, ranging from the printer’s model and specifications to the properties of the substrate and the operator’s skill. By understanding and optimizing these factors, print shops can enhance the performance of their UV flatbed printers, leading to faster turnaround times, higher quality prints, and increased overall productivity. Regular maintenance, efficient workflow management, and operator training are key to achieving and maintaining optimal printer performance. As technology continues to advance, it is essential to stay updated with the latest developments in UV flatbed printing to leverage new innovations and further improve efficiency.