UV Flatbed Printer: Handling Media with Different Surface Textures
UV Flatbed Printer: Handling Media with Different Surface Textures
In the realm of digital printing, UV flatbed printers have emerged as a versatile and powerful tool, capable of producing high-quality prints on a wide variety of substrates. Unlike traditional printing methods that may be limited to specific materials, UV flatbed printers utilize ultraviolet curing technology to instantly dry ink, allowing for precise and vibrant prints on surfaces with diverse textures. This adaptability makes them ideal for a plethora of applications, ranging from signage and packaging to personalized gifts and artistic creations. However, handling media with different surface textures requires a nuanced understanding of both the printer’s capabilities and the unique characteristics of each substrate. In this article, we will explore the intricacies of UV flatbed printing on various textures, discussing preparation techniques, printing parameters, and troubleshooting tips to achieve optimal results.
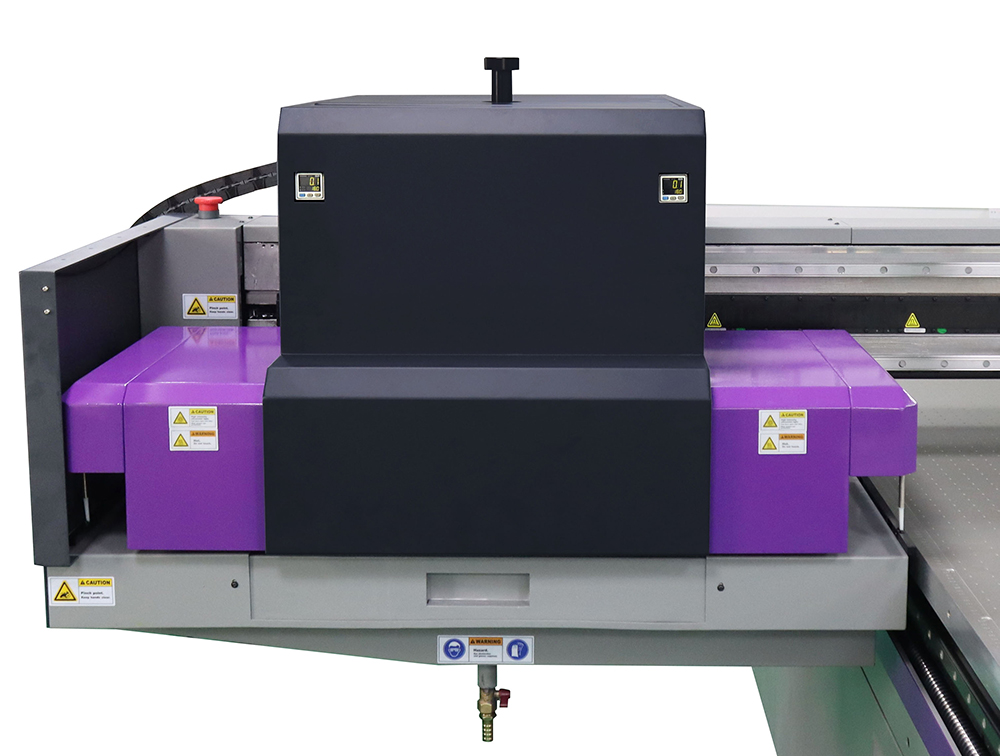
Understanding UV Flatbed Printer Technology
Before diving into the specifics of handling different media, it is essential to grasp the fundamentals of UV flatbed printing. These printers are equipped with a flat printing bed that can accommodate substrates of varying thicknesses and sizes. The ink used in UV printing contains photoinitiators that react when exposed to ultraviolet light, causing the ink to cure instantly. This process eliminates the need for drying time and enables the printer to produce sharp, durable images with vibrant colors and excellent adhesion.
The versatility of UV flatbed printers lies in their ability to print on rigid and semi-rigid materials, including but not limited to acrylic, glass, wood, metal, leather, and various types of plastics. The printer’s print heads can deposit ink with high precision, making it possible to achieve detailed prints even on uneven or textured surfaces.
Preparing Media for UV Flatbed Printing
Successful UV flatbed printing begins with proper media preparation. Different surface textures require tailored approaches to ensure optimal ink adhesion and print quality. Here are some general guidelines and techniques for preparing various types of media:
1. Cleaning and Degreasing
Purpose: Remove dust, oils, and contaminants that could interfere with ink adhesion.
Method: Use a mild cleaner or solvent specific to the substrate type. For example, isopropyl alcohol is often effective for plastics and metals, while a gentle detergent may be suitable for fabrics. Avoid using abrasives that could scratch the surface.
2. Surface Treatment
Purpose: Enhance ink adhesion and ensure even coverage.
Method: Depending on the substrate, this may involve applying a primer, coating, or adhesive promoter. For example, porous materials like wood may benefit from a sealing coat to prevent ink absorption, while non-porous materials like glass might require a special adhesive to ensure the ink bonds properly.
3. Handling Static and Dust
Purpose: Prevent static electricity and dust particles from interfering with the print process.
Method: Use anti-static sprays or wipes, and work in a clean, dust-free environment. Handling the media with clean gloves can also minimize contamination.
Printing on Different Surface Textures
Smooth Surfaces (e.g., Glass, Acrylic)
Challenges: Ensuring ink adhesion and avoiding runs or smudges.
Techniques:
Use a high-resolution setting to maintain image clarity.
Apply a thin, even layer of UV-curable adhesive or primer to improve ink bonding.
Adjust the printer’s settings to use a lower ink flow rate and multiple passes to build up the image gradually.
Textured Surfaces (e.g., Wood, Leather)
Challenges: Achieving even ink coverage and detail in textured areas.
Techniques:
Pre-treat the surface to fill in pores and create a more uniform printing surface. This might involve sanding wood to a fine finish or applying a texture-filling primer.
Use a higher ink flow rate and possibly a thicker ink formulation to ensure penetration into the texture.
Test print with varying levels of pressure to find the optimal setting that maintains detail without causing excessive ink spreading.
Uneven Surfaces (e.g., Stone, Brick)
Challenges: Adapting to irregularities and maintaining print quality.
Techniques:
Create a digital model of the surface using 3D scanning technology to compensate for unevenness in the printing process.
Employ a specialized ink with higher viscosity to prevent dripping and ensure the ink stays where it’s placed.
Use a multi-pass printing strategy with careful curing between passes to build up the image layer by layer.
Flexible Materials (e.g., Vinyl, Fabric)
Challenges: Managing the material’s flexibility and ensuring it remains flat during printing.
Techniques:
Secure the material firmly to the print bed using adhesive or mechanical clamps to prevent movement.
If the material is too flexible, consider mounting it onto a rigid backing, such as cardboard or plastic, for stability.
Use inks designed for flexibility to ensure the print remains intact when the material is bent or stretched.
Adjusting Printing Parameters
The key to successful UV flatbed printing on diverse textures lies in fine-tuning the printer’s settings. Here are some parameters to consider:
Ink Flow Rate: Adjust based on the substrate’s absorbency and texture. A higher flow rate may be needed for porous or textured surfaces.
Print Resolution: Increase resolution for smoother surfaces to capture fine details; lower resolution might be acceptable for more textured surfaces where detail is less critical.
Print Speed: Slowing down the print speed can improve ink adhesion and detail on textured surfaces.
Curing Time and Intensity: Optimize the UV curing process to ensure complete ink curing without overheating the substrate. Different substrates may require different curing times and intensities.
Troubleshooting Common Issues
Even with careful preparation and optimized settings, challenges can arise during UV flatbed printing. Here are some common issues and their solutions:
Ink Adhesion Problems: If ink is not adhering properly, check for contamination on the surface, ensure the correct primer or adhesive is used, and adjust the curing settings.
Bleeding or Smudging: Reduce ink flow rate, increase the number of print passes, or adjust the printer’s pressure settings.
Uneven Print Quality: Use a 3D surface model to compensate for irregularities, or adjust the printer’s Z-axis to maintain consistent print head distance from the surface.
Cracking or Peeling: This can be due to over-curing or incompatible inks. Adjust the curing settings and ensure the ink is suitable for the substrate.
UV flatbed printers offer unparalleled versatility in handling media with different surface textures, making them a valuable asset for a wide range of printing applications. Achieving optimal results, however, requires a deep understanding of both the printer’s capabilities and the unique characteristics of each substrate. By meticulously preparing the media, fine-tuning printing parameters, and troubleshooting common issues, one can unlock the full potential of UV flatbed printing, producing stunning, durable prints on even the most challenging surfaces. Whether you’re a professional printer, a designer, or an artist, mastering the art of UV flatbed printing will open up new creative possibilities and elevate your work to new heights.