UV Flatbed Printer: How to Achieve a Matte or Glossy Finish
UV Flatbed Printer: How to Achieve a Matte or Glossy Finish
In the realm of digital printing, UV flatbed printers have emerged as versatile and powerful tools, capable of producing high-quality prints on a diverse range of materials. One of the key aspects of UV flatbed printing is the ability to achieve different finishes, such as matte and glossy. This article delves into the nuances of achieving these finishes using UV flatbed printers, exploring the technicalities, benefits, and considerations for each.
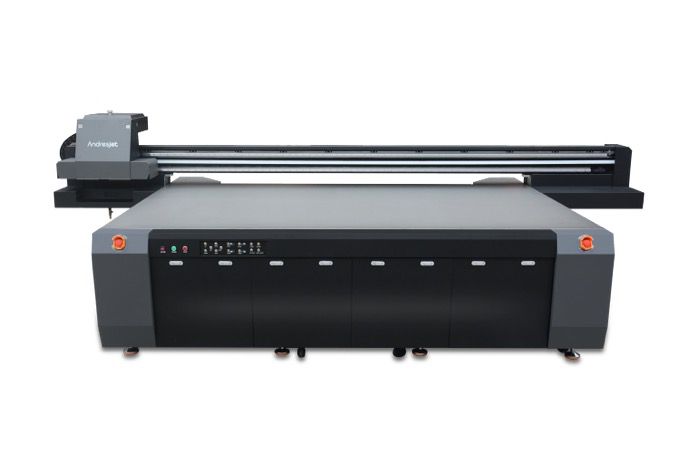
Understanding UV Flatbed Printers
UV flatbed printers utilize ultraviolet (UV) light to cure ink instantly upon application, allowing for high-speed, high-resolution printing on various substrates. These printers are renowned for their precision, versatility, and eco-friendliness, making them ideal for applications across multiple industries, including signage, packaging, and decorative arts.
The key to achieving different finishes lies in the ink formulation, printing process, and post-processing techniques. Let’s delve into the specifics of how to achieve matte and glossy finishes using UV flatbed printers.
Achieving a Matte Finish
A matte finish is non-reflective and somewhat rough to the touch, giving prints a soft, velvety appearance. It is often preferred for its subtlety and ability to reduce glare, making it ideal for applications where a low-key look is desired.
Ink Formulation
The first step in achieving a matte finish is to use a matte UV ink. These inks are formulated to have a lower level of gloss, which results in the non-reflective surface. When selecting a matte UV ink, it’s important to consider factors such as ink viscosity, curing speed, and compatibility with the printer’s printheads.
Printing Process
The printing process for a matte finish involves using the UV flatbed printer to apply the matte UV ink in the desired pattern. It’s crucial to calibrate the printer settings correctly to ensure even ink distribution and consistent results. This may include adjusting the printhead height, ink flow rate, and curing intensity.
Post-Processing
Post-processing techniques for a matte finish are minimal, as the matte UV ink cures to a flat, non-reflective surface. However, it’s essential to ensure that the print is fully cured to prevent smudging or scratching. This can be achieved by adjusting the UV curing time and intensity based on the specific ink and substrate used.
Achieving a Glossy Finish
A glossy finish, on the other hand, is shiny and smooth, giving prints a polished, high-end look. It is often preferred for its ability to enhance colors and create a more visually striking effect.
Ink Formulation
To achieve a glossy finish, it’s essential to use a glossy UV ink. These inks are formulated to have a higher level of gloss, which results in the reflective surface. Like matte inks, it’s important to consider factors such as ink viscosity, curing speed, and compatibility with the printer’s printheads when selecting a glossy UV ink.
Printing Process
The printing process for a glossy finish is similar to that of a matte finish, with the primary difference being the ink formulation. It’s crucial to calibrate the printer settings correctly to ensure even ink distribution and consistent results. This may include adjusting the printhead height, ink flow rate, and curing intensity to suit the specific glossy UV ink used.
Post-Processing
While glossy UV inks cure to a reflective surface, post-processing techniques can be used to enhance the gloss level further. One common method is to apply a UV varnish over the printed surface. This not only increases the gloss level but also adds an extra layer of protection against scratching and fading. It’s essential to ensure that the varnish is compatible with the underlying ink and substrate, and to apply it evenly to avoid streaking or pooling.
Considerations for Achieving Different Finishes
When aiming to achieve different finishes using UV flatbed printers, there are several factors to consider:
Substrate Compatibility
Not all substrates are suitable for both matte and glossy finishes. Some materials may have a natural texture or porosity that affects the final appearance. It’s important to test the ink and substrate combination to ensure compatibility and achieve the desired finish.
Ink Selection
Choosing the right ink is crucial for achieving the desired finish. Different inks have varying levels of gloss, viscosity, and curing speed, which can affect the final appearance and durability of the print. It’s essential to consult with the ink manufacturer or printer supplier to select the most appropriate ink for the specific application.
Printer Calibration
Printer calibration is key to achieving consistent results. It’s important to regularly calibrate the printer settings, including printhead height, ink flow rate, and curing intensity, to ensure even ink distribution and optimal curing.
Curing Process
The curing process plays a significant role in the final appearance of the print. UV flatbed printers use UV light to cure the ink instantly upon application. It’s essential to adjust the UV curing time and intensity based on the specific ink and substrate used to achieve the desired finish.
Cost and Efficiency
Achieving different finishes can have implications on cost and efficiency. For example, glossy finishes may require additional post-processing steps, such as applying a UV varnish, which can increase the overall production time and cost. It’s important to consider these factors when deciding on the most appropriate finish for a particular application.
Benefits of UV Flatbed Printing
In addition to the ability to achieve different finishes, UV flatbed printers offer several other benefits that make them an attractive choice for various printing applications:
High Resolution and Precision
UV flatbed printers are capable of producing prints with high resolution and precision, making them ideal for applications that require intricate details and sharp edges.
Versatility
UV flatbed printers can print on a wide range of substrates, including glass, wood, metal, and plastics. This versatility makes them suitable for a variety of applications across multiple industries.
Eco-Friendliness
UV flatbed printers use UV light to cure the ink instantly upon application, eliminating the need for solvents or water-based inks. This reduces the environmental impact of the printing process and makes UV flatbed printing a more sustainable choice.
Cost-Effectiveness
UV flatbed printers offer fast printing speeds and reduced downtime, which can contribute to overall cost savings. Additionally, the ability to print on a wide range of substrates without the need for special pre-treatment or coatings can further reduce production costs.
Conclusion
In conclusion, UV flatbed printers offer a versatile and powerful solution for achieving both matte and glossy finishes. By selecting the right ink, calibrating the printer settings correctly, and considering post-processing techniques, it’s possible to achieve a wide range of finishes that suit various applications and preferences. Whether aiming for a subtle matte finish or a polished glossy look, UV flatbed printers provide the tools and flexibility to create high-quality prints that meet specific needs.