UV Flatbed Printer: How to Achieve Consistent Color Output?
UV Flatbed Printer: How to Achieve Consistent Color Output?
In the realm of digital printing, achieving consistent color output is paramount to producing high-quality prints that meet customer expectations. UV flatbed printers, known for their versatility and ability to print on various materials, are no exception. These printers utilize ultraviolet (UV) light to cure ink instantly, resulting in durable and vibrant prints. However, ensuring color consistency across different print jobs and materials can be challenging. This article delves into the strategies and techniques for achieving consistent color output with UV flatbed printers.
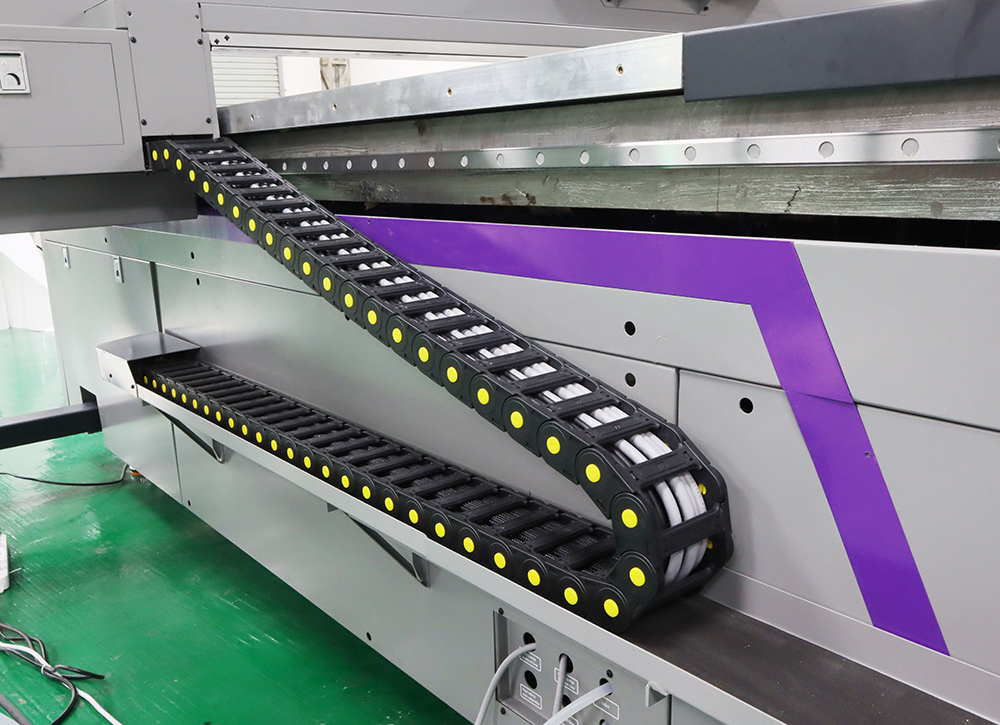
Understanding UV Flatbed Printer Technology
UV flatbed printers employ UV-curable inks that dry instantly when exposed to UV light. This technology allows for printing on a wide range of substrates, including glass, metal, plastic, wood, and more. The instant curing process enables the printer to produce high-resolution images with sharp details and vibrant colors. However, several factors can influence color consistency, including ink quality, printer calibration, material properties, and environmental conditions.
Key Factors Influencing Color Consistency
Ink Quality and Consistency: The quality of UV-curable inks significantly impacts color consistency. Inks must be formulated to provide consistent color output across different materials and print modes. Variations in ink viscosity, pigment concentration, or curing properties can lead to color inconsistencies.
Printer Calibration: Regular printer calibration is essential to maintain color accuracy. Calibration involves adjusting the printer’s settings to ensure that the colors produced match the intended colors in the digital file. Over time, printer components such as UV lamps and printheads can degrade, affecting color output.
Material Properties: Different materials absorb ink differently, leading to variations in color appearance. For instance, a glossy surface may reflect light differently than a matte surface, altering the perceived color. Understanding how ink interacts with specific materials is crucial for achieving consistent results.
Environmental Conditions: Temperature and humidity can affect ink curing and adhesion, ultimately influencing color consistency. UV inks cure more effectively within specific temperature and humidity ranges. Deviations from these ideal conditions can result in inconsistent curing and color appearance.
Strategies for Achieving Consistent Color Output
Use High-Quality UV Inks: Invest in UV inks that are specifically designed for flatbed printing and known for their color consistency. Look for inks that have been rigorously tested for color accuracy and curing properties.
Regular Printer Maintenance and Calibration: Establish a regular maintenance schedule for your UV flatbed printer. This includes cleaning printheads, checking UV lamp intensity, and replacing worn components. Calibrate the printer regularly using industry-standard color charts or software to ensure accurate color reproduction.
Material Testing and Profiling: Test different materials to understand how they interact with UV inks. Create material profiles that outline the optimal printer settings for each material to achieve consistent color output. This may involve adjusting ink density, curing speed, or print resolution.
Control Environmental Factors: Maintain a stable printing environment by controlling temperature and humidity levels. Invest in equipment that monitors and regulates these conditions to ensure they remain within the optimal range for UV ink curing.
Software and Workflow Optimization: Utilize color management software to ensure color consistency throughout the printing process. This software can help with color profiling, calibration, and ink limitation to achieve the desired color output. Additionally, standardize your printing workflow to minimize variables that could affect color consistency.
Operator Training and Expertise: Train your printing operators on best practices for achieving consistent color output. This includes understanding printer settings, ink properties, material characteristics, and how to recognize and address color inconsistencies.
Post-Print Inspection and Quality Control: Implement a rigorous quality control process that includes post-print inspection. Use color measurement tools to verify that prints meet specified color standards. Adjust printer settings or material profiles as needed based on inspection results.
Case Study: Achieving Consistent Color Output in UV Flatbed Printing
A company specializing in printing custom promotional materials for various industries faced challenges in achieving consistent color output across different materials. They invested in high-quality UV inks and implemented a regular printer maintenance and calibration schedule. Additionally, they conducted extensive material testing and profiling, creating specific printer settings for each material they used.
To further enhance color consistency, they installed equipment to control temperature and humidity in their printing environment. They also optimized their printing workflow and trained their operators on best practices for achieving consistent color output.
As a result of these efforts, the company significantly improved color consistency across different print jobs and materials. Customer satisfaction increased, and they gained a competitive edge in the market due to their ability to deliver high-quality, consistent prints.
Conclusion
Achieving consistent color output with UV flatbed printers requires a comprehensive approach that addresses ink quality, printer calibration, material properties, environmental conditions, and workflow optimization. By investing in high-quality inks, maintaining printers regularly, testing and profiling materials, controlling environmental factors, optimizing software and workflow, training operators, and implementing quality control measures, companies can ensure that their UV flatbed prints meet the highest standards of color consistency. This not only enhances customer satisfaction but also contributes to the overall success and competitiveness of the printing business.