UV Flatbed Printer: How to Achieve High-Definition Printing
In the realm of digital printing, the UV flatbed printer has emerged as a game-changer, particularly for those seeking high-definition prints on a wide array of substrates. This versatile printing technology utilizes ultraviolet light to cure inks instantly, allowing for precise and vibrant images on materials ranging from rigid plastics to flexible fabrics. Achieving high-definition printing with a UV flatbed printer involves a combination of advanced hardware, meticulous preparation, and skilled operation. In this article, we delve into the key factors that contribute to the outstanding print quality produced by UV flatbed printers.
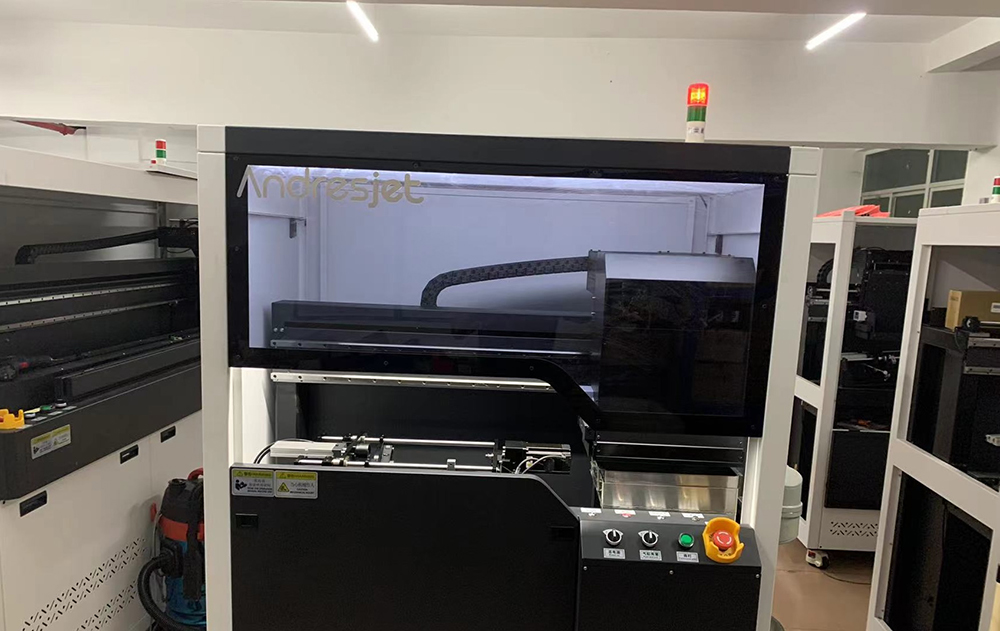
1. Understanding UV Flatbed Printer Technology
At the heart of a UV flatbed printer lies its innovative inkjet system. Unlike traditional solvent or aqueous inks, UV-curable inks are formulated to solidify almost instantaneously when exposed to UV light. This rapid curing process not only speeds up production but also enables the ink to adhere to a broader range of surfaces without the need for primers or coatings. The result is a durable, scratch-resistant, and water-proof print that maintains its vibrancy over time.
The printer’s flatbed design accommodates various object shapes and sizes, making it ideal for printing on three-dimensional items such as phone cases, tiles, and even wooden panels. The precision of the print heads, often equipped with multiple nozzles, ensures that ink droplets are deposited with pinpoint accuracy, contributing to the overall sharpness and detail of the final output.
2. The Role of High-Quality Inks
One of the cornerstone elements in achieving high-definition printing is the use of premium UV-curable inks. These inks are engineered to deliver exceptional color saturation, clarity, and resistance to fading. They contain pigments that are finely dispersed, ensuring smooth and even ink flow through the print heads. Moreover, the chemical composition of UV inks allows for superior adhesion to different materials, reducing the risk of ink bleeding or smudging during the curing process.
Investing in high-quality inks might incur higher costs initially, but the benefits in terms of print quality and durability far outweigh the expense. Cheaper alternatives may compromise on color accuracy, fade more quickly, or fail to adhere properly to the substrate, ultimately leading to dissatisfied customers and potential rework.
3. Optimizing Print Resolution
Print resolution is a critical factor in determining the level of detail in a print. UV flatbed printers typically offer resolutions ranging from 720×720 dpi to an impressive 2880×1440 dpi or even higher. The higher the resolution, the finer the details and the smoother the transitions between colors. For high-definition printing, it’s essential to select the appropriate resolution setting based on the specific requirements of the job.
However, it’s worth noting that opting for the highest resolution isn’t always necessary or cost-effective. The choice of resolution should balance the desired print quality with production efficiency and ink consumption. For instance, intricate artwork or photographic prints may demand the highest resolution, while simpler graphics or text-based designs can often achieve satisfactory results at lower settings.
4. Substrate Preparation
The condition and type of substrate play a significant role in the outcome of UV printing. Properly preparing the surface ensures optimal ink adhesion and reduces the likelihood of issues such as banding, cracking, or poor color uniformity. Substrates should be clean, dry, and free of dust, oils, or any contaminants that could interfere with the ink’s ability to adhere.
For certain materials, such as metals or glasses, a pre-treatment process might be necessary to enhance ink adhesion. This could involve using a special primer or subjecting the surface to a plasma or corona treatment. On the other hand, some plastics and coated papers may require no additional preparation, making them ideal for quick turnaround projects.
5. Calibrating the Printer
Regular calibration of the UV flatbed printer is vital for maintaining high-definition print quality. Calibration involves adjusting the print heads, ensuring they are aligned correctly and depositing ink uniformly. It also entails verifying the color accuracy by comparing printed samples to standard color charts.
Automated calibration tools have made this process more straightforward, but manual checks and adjustments are still necessary to fine-tune the printer’s performance. Operators should perform calibration routines at the start of each printing session, especially after changing ink cartridges or performing maintenance tasks.
6. Controlling UV Curing
The UV curing process is as crucial as the ink deposition itself. The intensity and duration of UV exposure must be carefully controlled to ensure complete curing without overexposure, which could lead to ink brittleness or substrate damage. Modern UV flatbed printers are equipped with advanced curing systems that use LED or mercury vapor lamps to emit precise amounts of UV light.
The curing parameters, such as lamp power, exposure time, and the distance between the lamp and the printed surface, should be tailored to the specific ink and substrate being used. Manufacturers often provide guidelines for optimal curing settings, but experienced operators may need to make minor adjustments based on real-world conditions and the desired print characteristics.
7. Post-Processing Techniques
The final step in achieving high-definition prints involves post-processing. This may include trimming excess material, applying a protective coating, or performing quality control inspections. For some applications, a clear varnish or laminate can be added to enhance the print’s durability and provide a glossy or matte finish.
Post-processing also offers an opportunity to address any minor imperfections that may have occurred during printing or curing. For example, using a fine sandpaper or polishing cloth can smooth out rough edges or remove small bits of cured ink that have adhered inadvertently to the substrate.
Achieving high-definition printing with a UV flatbed printer is a multifaceted endeavor that requires attention to detail at every stage of the process. From selecting high-quality inks and optimizing print resolution to preparing substrates and controlling UV curing, each step contributes to the overall excellence of the final print. Regular calibration and meticulous post-processing further enhance the print quality, ensuring that the output meets or exceeds customer expectations.
As technology continues to advance, UV flatbed printers will undoubtedly become even more capable, offering higher resolutions, faster curing times, and broader substrate compatibility. However, the fundamental principles outlined in this article will remain relevant, serving as a guide for printers striving to achieve the highest standards in UV printing. By focusing on these key areas, businesses can leverage the full potential of UV flatbed printers to produce stunning, high-definition prints that stand out in a competitive market.