UV Flatbed Printer: How to Achieve High-Gloss Finish on Prints?
UV Flatbed Printer: How to Achieve High-Gloss Finish on Prints?
In the realm of digital printing, achieving a high-gloss finish on prints is a sought-after goal for many businesses and individuals. A glossy finish not only enhances the visual appeal of printed materials but also adds durability and protection against wear and tear. One of the most effective ways to achieve this glossy effect is by using a UV flatbed printer. This article delves into the intricacies of UV flatbed printing and provides insights on how to attain a high-gloss finish on your prints.
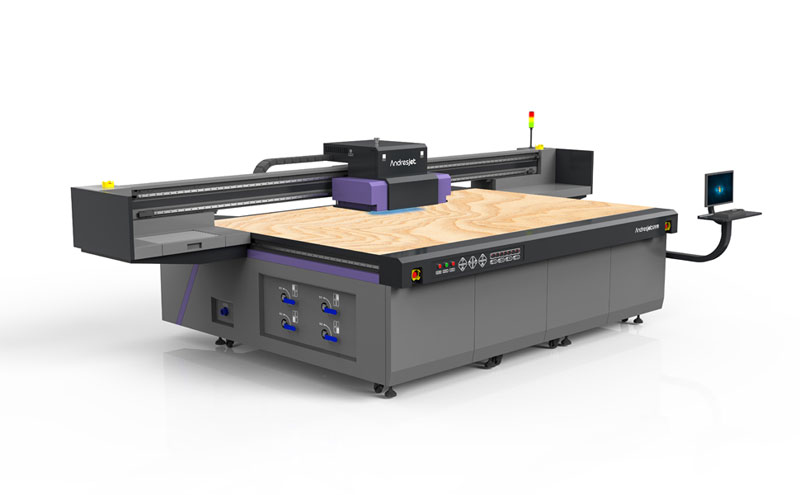
Understanding UV Flatbed Printers
UV flatbed printers are a type of digital printing technology that utilizes ultraviolet (UV) light to cure or dry ink as it is applied to a substrate. This process allows for instant drying, resulting in prints that are ready for handling or further processing immediately after printing. The term “flatbed” refers to the printer’s flat surface, which can accommodate various materials of different thicknesses and sizes, making it versatile for a wide range of applications.
UV flatbed printers are particularly suited for achieving high-gloss finishes due to the nature of UV-curable inks. These inks, when exposed to UV light, form a hard, glossy surface that is resistant to fading, scratching, and chemical degradation. This makes UV flatbed printing an ideal choice for applications that require both aesthetic appeal and durability.
Key Factors for Achieving High-Gloss Finish
Ink Selection: The choice of ink plays a pivotal role in achieving a high-gloss finish. UV-curable inks are specifically designed to cure under UV light, forming a smooth, glossy surface. Look for inks that are specifically marketed for their gloss capabilities. Some ink manufacturers offer gloss-optimized formulations that can enhance the final appearance of your prints.
Printer Settings: Proper printer settings are crucial for achieving the desired gloss effect. This includes adjusting the ink layer thickness, print speed, and UV light intensity. Thicker ink layers can result in a higher gloss, but they also require longer curing times and may increase the risk of ink bleeding or pooling. Finding the right balance between ink thickness and curing speed is essential.
Substrate Selection: The material you choose to print on can significantly impact the final gloss level. Smooth, non-porous surfaces tend to reflect light better, resulting in a higher gloss appearance. Materials such as glass, acrylic, and certain types of plastics are ideal for achieving a glossy finish. Conversely, porous or textured surfaces may absorb more ink, reducing the gloss effect.
Post-Print Curing: After the initial print and cure process, an additional post-print curing step can further enhance the gloss and durability of the print. This involves exposing the printed material to UV light for an extended period, ensuring that all ink layers are fully cured and hardened. Post-print curing can also help to reduce the risk of ink adhesion issues and increase the overall longevity of the print.
Surface Preparation: Proper surface preparation is often overlooked but is crucial for achieving a high-gloss finish. Ensure that the substrate is clean, dry, and free from any contaminants that could interfere with ink adhesion. For some materials, applying a primer or pretreatment may be necessary to improve ink adhesion and gloss levels.
Environmental Conditions: The ambient temperature and humidity can affect the curing process and ultimately the gloss of the print. UV inks cure more efficiently in controlled environments with moderate temperatures and low humidity. High humidity can cause ink to cure too slowly, leading to a dull appearance, while extreme temperatures can cause ink to cure unevenly.
Tips for Optimizing Gloss Finish
Experiment with different ink formulations to find the one that provides the best gloss effect for your specific application.
Use a gloss meter to measure the gloss level of your prints. This will help you quantify the effectiveness of different printing parameters and make adjustments accordingly.
Consider investing in a UV flatbed printer with adjustable UV light intensity. This will allow you to fine-tune the curing process for optimal gloss results.
When printing on substrates with varying textures or porosities, test the ink adhesion and gloss levels before proceeding with large-scale production.
Regularly clean and maintain your UV flatbed printer to ensure consistent print quality and gloss levels.
Applications of High-Gloss UV Flatbed Printing
The ability to achieve a high-gloss finish with UV flatbed printing makes it suitable for a wide range of applications, including:
Point-of-sale displays and signage
Product packaging and labeling
Fine art reproduction and photography
Architectural and decorative panels
Automotive and transportation graphics
Promotional items and merchandise
Conclusion
Achieving a high-gloss finish on prints with a UV flatbed printer is a multifaceted process that requires careful consideration of ink selection, printer settings, substrate choice, and environmental conditions. By understanding the intricacies of UV flatbed printing and implementing best practices, it is possible to produce prints with a stunning, durable gloss finish that meets or exceeds your expectations. Whether you’re a professional printer or a hobbyist, mastering the art of high-gloss UV flatbed printing can open up new creative possibilities and enhance the visual impact of your work.