UV Flatbed Printer: How to Achieve High-Gloss Finishes
UV Flatbed Printer: How to Achieve High-Gloss Finishes
The UV flatbed printer has emerged as a game-changer in the field of digital printing, particularly when it comes to achieving high-gloss finishes on a variety of materials. With its ability to print directly onto a wide range of surfaces, from glass to metals, and from plastics to ceramics, the UV flatbed printer has revolutionized the way we approach printing tasks. This article delves into the intricacies of achieving high-gloss finishes using UV flatbed printers, exploring the technology behind them, the materials they can print on, and the steps involved in ensuring a flawless, high-gloss outcome.
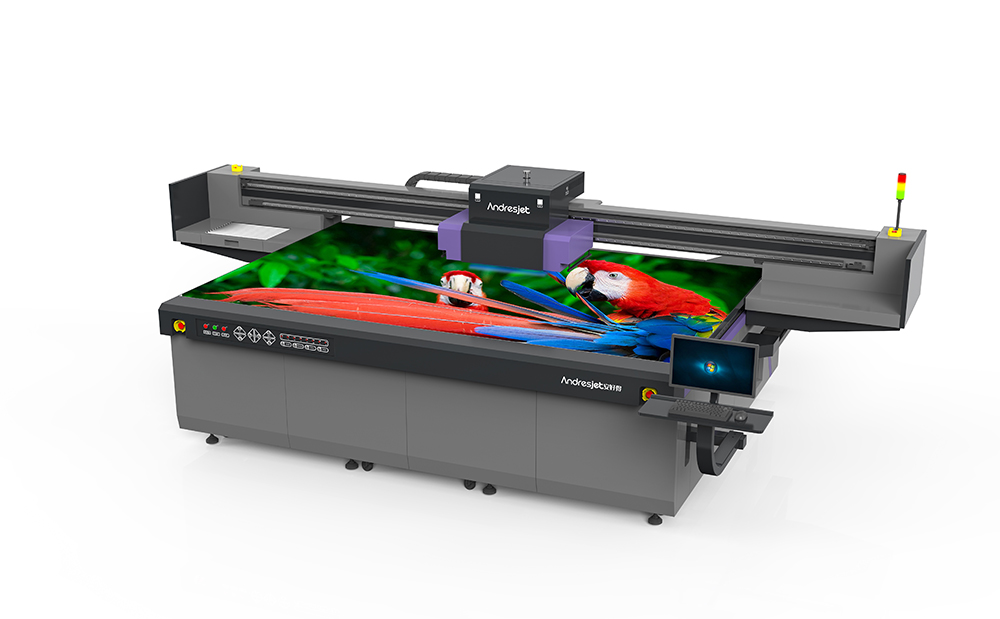
The Technology Behind UV Flatbed Printers
UV flatbed printers utilize UV-curing inkjet technology, which allows for the instant curing of ink upon exposure to ultraviolet light. This process ensures high-quality prints with exceptional gloss levels, durability, and color vibrancy. Unlike traditional solvent-based inks, UV inks do not require long drying times, reducing production cycles and enhancing overall efficiency.
Key Features of UV Flatbed Printers
High Precision: UV flatbed printers employ high-resolution printheads, often with a variable droplet size, enabling them to print fine details and sharp images. This precision is crucial for achieving high-gloss finishes, as it ensures that ink droplets are evenly distributed across the surface, creating a smooth and reflective surface.
Wide Material Compatibility: UV flatbed printers can print on virtually any flat surface, including glass, metal, plastics, ceramics, and more. This versatility makes them ideal for a wide range of applications, from signage and advertising to product prototyping and decorative arts.
Instant Curing: UV inks cure almost instantly upon exposure to UV light, eliminating the need for long drying times. This not only speeds up the production process but also ensures that the printed surface remains smooth and free of imperfections, contributing to the overall glossiness of the print.
Environmental Friendliness: UV inks are generally more environmentally friendly than solvent-based inks, as they emit fewer volatile organic compounds (VOCs). This makes UV flatbed printers a greener choice for businesses looking to reduce their environmental impact.
Achieving High-Gloss Finishes
Achieving high-gloss finishes with a UV flatbed printer requires a combination of the right materials, proper printer settings, and post-processing steps. Here’s a detailed look at each aspect:
Materials
The choice of material is crucial for achieving high-gloss finishes. Materials with a smooth and non-porous surface, such as glass, metals, and certain plastics, are ideal for high-gloss prints. These surfaces allow the ink to spread evenly and cure without absorbing into the substrate, resulting in a smooth and reflective surface.
Examples of Ideal Materials:
Glass: Glass is a popular choice for high-gloss prints due to its smooth and non-porous surface. It can be easily cleaned and prepared for printing, ensuring a flawless finish.
Metals: Metals such as stainless steel and aluminum offer a durable and reflective surface that enhances the glossiness of UV prints. They require proper surface preparation to ensure optimal adhesion of the ink.
Plastics: Certain plastics, such as acrylics and polycarbonates, can also achieve high-gloss finishes when printed with UV inks. The key is to choose plastics with a smooth and non-porous surface.
Printer Settings
Achieving high-gloss finishes also involves fine-tuning the printer settings to ensure optimal ink laydown and curing.
Key Printer Settings:
Ink Type: Choose a UV ink formulated for high-gloss finishes. Some inks are specifically designed to produce a high-gloss surface when cured.
Print Resolution: High-resolution settings ensure that ink droplets are evenly distributed across the surface, creating a smooth and reflective surface. Generally, resolutions of 1200 dpi or higher are recommended for high-gloss finishes.
Ink Laydown: Adjust the ink laydown settings to ensure that the correct amount of ink is deposited on the surface. Too little ink can result in a dull finish, while too much can cause ink pooling and imperfections.
Curing Intensity: The intensity and duration of UV light exposure are critical for proper curing of the ink. Ensure that the UV lamp is powerful enough to cure the ink evenly and completely.
Post-Processing
Achieving high-gloss finishes often requires additional post-processing steps to enhance the smoothness and reflectivity of the printed surface.
Common Post-Processing Steps:
Cleaning: Thoroughly clean the printed surface to remove any dust, fingerprints, or other contaminants that could affect the glossiness. Use a lint-free cloth and a suitable cleaning solution.
Polishing: For certain materials, such as metals, a light polishing step can enhance the glossiness of the print. Use a polishing compound and a soft cloth to buff the surface until it reaches the desired level of gloss.
Coating: Applying a clear UV-curing coating can further enhance the glossiness of the print. This coating can also provide additional protection against scratches and UV damage.
Lamination: For applications requiring extra durability, lamination can be used to protect the printed surface while maintaining its glossiness. Choose a high-gloss laminate that is compatible with UV inks.
Case Studies and Applications
To better understand how UV flatbed printers achieve high-gloss finishes, let’s explore a few case studies and applications.
Case Study 1: High-Gloss Signs and Graphics
UV flatbed printers are widely used in the signage and graphics industry to produce high-quality prints with exceptional gloss levels. One such example is the production of high-gloss acrylic signs.
Process:
Preparation: Clean the acrylic sheet and ensure it is free of dust, fingerprints, and other contaminants.
Printing: Use a UV flatbed printer to print the desired design onto the acrylic sheet. Choose a high-gloss UV ink and adjust the printer settings for optimal ink laydown and curing.
Curing: Expose the printed surface to UV light to cure the ink. Ensure that the UV lamp is powerful enough to cure the ink evenly and completely.
Post-Processing: Optionally, apply a clear UV-curing coating to enhance the glossiness and durability of the print.
Result: A high-gloss acrylic sign with vibrant colors and a smooth, reflective surface.
Case Study 2: High-Gloss Metal Prints
UV flatbed printers can also be used to produce high-gloss prints on metal surfaces, such as stainless steel and aluminum.
Process:
Preparation: Clean the metal surface and remove any grease, oil, or other contaminants. Use a suitable cleaning solution and a lint-free cloth.
Surface Treatment: Apply a primer or adhesion promoter to the metal surface to ensure optimal adhesion of the ink.
Printing: Use a UV flatbed printer to print the desired design onto the metal surface. Choose a high-gloss UV ink and adjust the printer settings for optimal ink laydown and curing.
Curing: Expose the printed surface to UV light to cure the ink. Ensure that the UV lamp is powerful enough to cure the ink evenly and completely.
Post-Processing: Optionally, polish the printed surface to enhance the glossiness. Use a polishing compound and a soft cloth to buff the surface until it reaches the desired level of gloss.
Result: A high-gloss metal print with vibrant colors and a smooth, reflective surface.
Applications
UV flatbed printers with high-gloss capabilities have a wide range of applications, including:
Signage and Advertising: High-gloss signs and graphics attract attention and enhance the visual appeal of any environment.
Product Prototyping: Create high-gloss prototypes for product design and development, providing a realistic representation of the final product.
Decorative Arts: Produce high-gloss prints for decorative arts, such as wall art, murals, and custom gifts.
Packaging: Enhance the appearance of packaging with high-gloss finishes, making products stand out on store shelves.
Conclusion
UV flatbed printers offer a powerful and versatile solution for achieving high-gloss finishes on a variety of materials. By combining the right materials, proper printer settings, and post-processing steps, businesses can produce prints with exceptional gloss levels, vibrant colors, and smooth, reflective surfaces. As technology continues to advance, UV flatbed printers will undoubtedly play a crucial role in the future of digital printing, enabling businesses to create stunning prints that captivate and impress.