UV Flatbed Printer: How to Achieve the Best Print Quality?
UV Flatbed Printer: How to Achieve the Best Print Quality?
In the realm of digital printing, UV flatbed printers have revolutionized the way we approach surface decoration and customization. These versatile machines offer unparalleled precision, speed, and versatility, making them ideal for a wide range of applications, from signage and advertising to industrial manufacturing and artistic endeavors. However, achieving the best print quality with a UV flatbed printer requires a combination of technical understanding, proper maintenance, and attention to detail. This article delves into the key factors that contribute to optimal print quality and provides practical tips on how to harness the full potential of your UV flatbed printer.
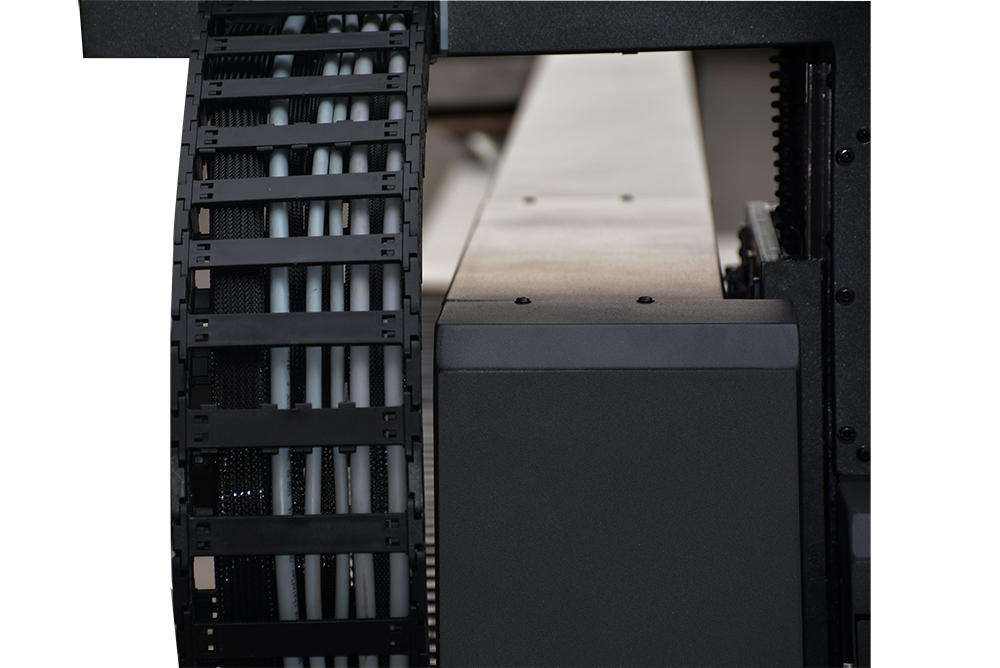
Understanding UV Flatbed Printer Technology
UV flatbed printers utilize ultraviolet (UV) light to instantly cure ink as it is deposited onto the substrate. This process enables the printer to produce high-resolution images with vibrant colors and excellent durability. The UV curing mechanism also allows for printing on a variety of materials, including plastics, glass, metal, wood, and even some textiles, without the need for pre-treatment or post-processing steps like drying or fixing.
Key Factors Influencing Print Quality
Printer Settings and Calibration
Resolution: Higher DPI (dots per inch) settings result in finer detail and smoother transitions between colors. For most applications, a resolution of 300 DPI is sufficient, but for fine art or intricate designs, increasing the DPI can yield even better results.
Color Management: Proper color calibration ensures accurate color reproduction. Use ICC profiles specific to your printer and substrate for consistent color output.
Ink Quality and Selection
UV inks are formulated to cure rapidly under UV light, but the quality of inks can vary significantly. Opt for inks from reputable manufacturers that offer good adhesion, resistance to fading, and environmental stability.
Consider the specific properties required for your application, such as flexibility, chemical resistance, or outdoor durability.
Substrate Preparation
Cleanliness is crucial. Ensure the substrate is dust-free, oil-free, and dry before printing.
Depending on the material, pre-treatment might be necessary to enhance ink adhesion. This can include the use of primers or adhesion promoters.
Print Bed and Media Handling
Leveling and securing the substrate on the print bed prevent movement during printing, which can lead to blurred images or misalignment.
Use the appropriate media clamps or vacuum systems designed for your printer to ensure stability.
Environmental Factors
Temperature and humidity can affect ink curing and adhesion. Maintain a controlled environment with recommended temperature and humidity levels as specified by the printer manufacturer.
Avoid exposing printed materials to direct sunlight or extreme temperatures immediately after printing to prevent ink from overheating or curing unevenly.
Achieving the Best Print Quality: Practical Tips
Regular Maintenance
Keep your printer clean and dust-free. Regularly inspect and replace worn parts such as printheads and wiper blades.
Follow the manufacturer’s recommended maintenance schedule for ink system flushes and UV lamp replacements.
Testing and Sampling
Before commencing a large print job, perform test prints on the actual substrate to evaluate ink adhesion, color accuracy, and overall print quality.
Adjust printer settings accordingly based on the test results.
Software Optimization
Use high-quality image files with sufficient resolution. Avoid compressing images, as this can degrade print quality.
Utilize raster image processors (RIPs) that are optimized for UV printing to manage color, resolution, and print speed efficiently.
Ink Curing Techniques
Experiment with different curing settings to find the optimal balance between cure speed and ink layer thickness. Overcuring can lead to ink cracking, while undercuring may result in poor adhesion.
For multi-layer prints, allow each layer to cure partially before applying the next to avoid overheating and ink bleeding.
Operator Training
Ensure operators are trained in printer operation, ink handling, and safety protocols.
Encourage a culture of continuous learning and experimentation to stay updated with new techniques and materials.
Conclusion
Achieving the best print quality with a UV flatbed printer is a multifaceted endeavor that involves attention to detail at every stage of the printing process. From selecting the right inks and substrates to calibrating printer settings and maintaining the equipment, each step plays a crucial role in producing outstanding prints. By following the tips outlined in this article and adopting a proactive approach to printer maintenance and quality control, users can unlock the full potential of their UV flatbed printers, delivering exceptional results that meet or exceed client expectations. As technology continues to advance, staying informed about the latest developments in UV printing technology will further enhance the ability to achieve and maintain superior print quality.