UV Flatbed Printer: How to Adjust Print Settings for Optimal Output
UV Flatbed Printer: How to Adjust Print Settings for Optimal Output
In the realm of digital printing, UV flatbed printers have revolutionized the industry by offering versatility, precision, and speed. These printers utilize ultraviolet (UV) light to instantly dry and cure inks onto a wide variety of substrates, from rigid materials like glass and metal to flexible ones such as textiles and plastics. However, achieving optimal print output on a UV flatbed printer requires a meticulous adjustment of print settings. This article delves into the key parameters that you should tweak to ensure your prints are of the highest quality.
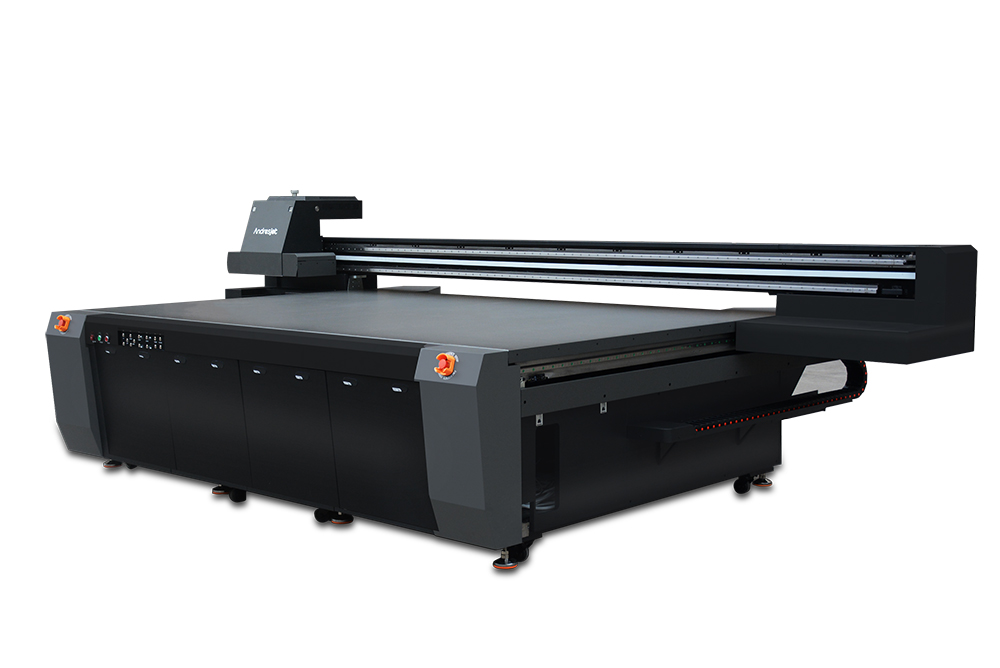
Understanding UV Inkjet Technology
Before diving into the specifics of adjusting print settings, it’s crucial to understand the basics of UV inkjet technology. UV inks contain pigments or dyes suspended in a carrier fluid that solidifies when exposed to UV light. The printer’s printheads eject tiny droplets of ink onto the substrate, and UV LED or arc lamps then cure the ink almost instantly, creating a durable and vibrant print.
Key Print Settings to Adjust
1. Resolution
Resolution refers to the number of dots per inch (DPI) that the printer can produce. Higher DPI values result in finer details and smoother transitions in images. However, increasing resolution also increases the print time and can consume more ink.
Optimal Setting: Typically, a resolution of 600-1200 DPI is sufficient for most applications. For high-end graphics, such as fine art prints or detailed photographs, you might opt for 1200-2400 DPI. Always test prints at different resolutions to find the balance between quality and efficiency.
2. Ink Density/Coverage
Ink density, also known as ink limit or coverage, affects the amount of ink deposited on the substrate. A higher ink density can increase color saturation and richness but can also lead to issues like ink pooling or drying problems.
Optimal Setting: Start with the printer’s default ink density settings and gradually adjust based on test prints. If colors appear washed out, incrementally increase the ink density. Conversely, if there’s noticeable ink bleeding or pooling, decrease the ink density.
3. Print Speed
Print speed is a critical factor influencing productivity but also affects print quality. Faster print speeds may reduce the time required to complete a job but can compromise the cure time of the UV ink, leading to incomplete drying or adhesion issues.
Optimal Setting: Balance print speed with quality requirements. For high-quality prints, reduce the speed to ensure proper ink curing. For production runs where speed is paramount, experiment with faster settings but always verify print quality.
4. Color Management
Color management is crucial for achieving accurate and consistent color reproduction. It involves calibrating the printer, monitor, and software to work harmoniously within a defined color space.
Optimal Setting: Use ICC (International Color Consortium) profiles specific to your printer, inks, and substrates. Regularly recalibrate your printer and monitor to maintain color accuracy. Utilize color management software to ensure that the colors you see on your screen are accurately reproduced on the printed material.
5. Curing Settings
Curing is the process of solidifying the UV ink through exposure to UV light. The intensity and duration of UV exposure directly impact the ink’s cure quality, which affects durability, scratch resistance, and overall appearance.
Optimal Setting: Follow the manufacturer’s guidelines for initial curing settings. Adjust based on substrate type and ink formulation. Over-curing can cause ink cracking, while under-curing can result in ink remaining tacky or smudging. Test prints with varying curing settings to find the optimal balance.
6. Nozzle Check and Head Cleaning
Maintaining the printheads is vital for consistent print quality. Regularly performing a nozzle check ensures that all nozzles are firing correctly, while head cleaning removes any blockages or residue.
Optimal Setting: Incorporate a nozzle check and head cleaning routine into your daily or weekly maintenance schedule. Follow the printer manufacturer’s instructions for specific procedures and frequencies.
Adjusting Settings Based on Substrate Type
Different substrates require unique print settings to achieve optimal results. Here are some considerations for common substrate types:
Rigid Substrates (Glass, Metal, Acrylic)
Resolution: Opt for higher resolutions (1200-2400 DPI) to capture intricate details.
Ink Density: Use moderate to high ink density to ensure vibrant colors.
Curing: Ensure thorough curing to achieve a durable, scratch-resistant finish.
Print Speed: Reduce speed if necessary to ensure proper ink curing.
Flexible Substrates (Textiles, Vinyl, Plastic Films)
Resolution: A balance between 600-1200 DPI usually suffices, depending on the graphic’s complexity.
Ink Density: Adjust ink density based on the substrate’s absorbency. Porous materials may require less ink.
Curing: Be cautious with flexible materials to avoid overheating, which can distort or melt the substrate.
Print Speed: May be increased slightly compared to rigid substrates, depending on the material’s handling properties.
Mixed Media (Composite Materials, Laminates)
Resolution: Choose settings that strike a balance between detail and efficiency.
Ink Density: Adjust based on the substrate’s surface texture and porosity.
Curing: Test for optimal cure settings to avoid damaging the substrate’s surface or layers.
Print Speed: Adjust speed to accommodate the material’s thermal properties and ink absorption rate.
Practical Tips for Achieving Optimal Print Settings
Start with Manufacturer Recommendations: Always begin with the settings recommended by the printer manufacturer. These are usually based on extensive testing and provide a solid starting point.
Perform Test Prints: Regularly print test patterns and samples using different settings combinations. Analyze the results under various lighting conditions to ensure color consistency and quality.
Use Print Profiles: Create and save print profiles for different substrates and applications. This allows for quick and consistent setup when printing similar jobs in the future.
Monitor Environmental Conditions: Humidity, temperature, and dust can all impact print quality. Maintain a controlled print environment to minimize variability.
Invest in Quality Substrates: High-quality substrates not only enhance the final appearance but also respond better to UV inks, leading to more consistent print results.
Stay Updated: Keep your printer software and firmware updated. Manufacturers often release updates that improve print quality, add new features, or resolve known issues.
Conclusion
Achieving optimal print output on a UV flatbed printer involves a combination of careful planning, meticulous settings adjustments, and ongoing maintenance. By understanding the key parameters and how they interact with different substrates, you can fine-tune your printer to produce high-quality prints efficiently. Regular testing, the use of quality substrates, and adhering to best practices will ensure that your UV flatbed printer consistently delivers stunning results. With the right settings and approach, you can unlock the full potential of UV flatbed printing technology.