UV Flatbed Printer: How to Print on Corrugated Materials?
UV Flatbed Printer: How to Print on Corrugated Materials?
The UV flatbed printer has revolutionized the printing industry by offering unparalleled versatility, precision, and efficiency. Its ability to print directly onto a wide range of materials, including corrugated materials, has made it a game-changer for packaging and signage applications. In this article, we will explore the intricacies of using UV flatbed printers for printing on corrugated materials, including the technology behind it, the advantages it offers, and the steps involved in the process.
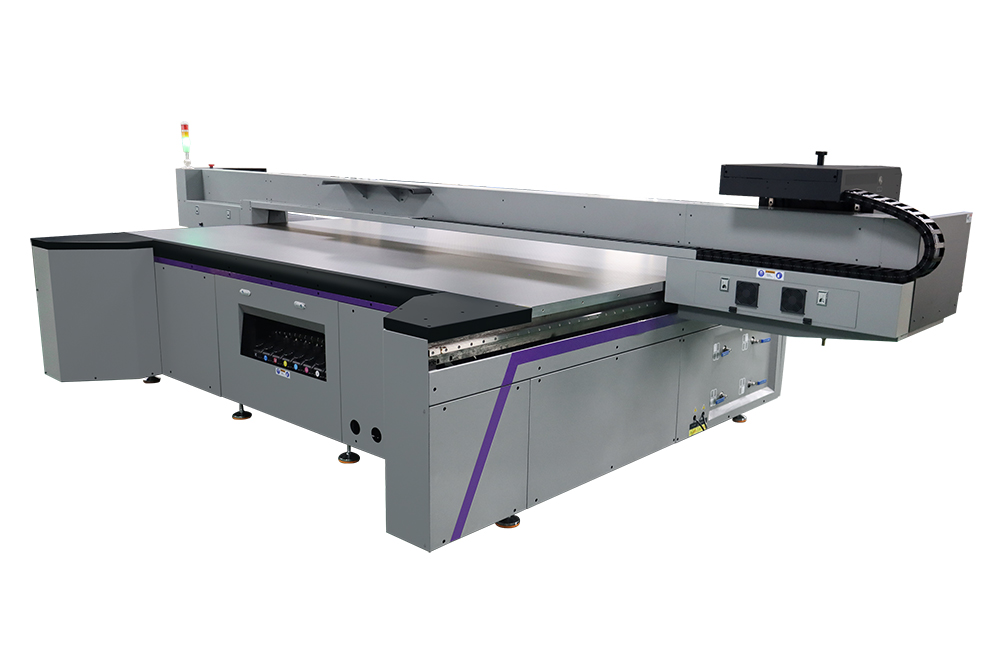
Introduction to UV Flatbed Printers
UV flatbed printers employ ultraviolet (UV) curing inkjet technology, allowing for high-quality printing on a variety of substrates without the need for pre-treatment or lamination. These printers feature a fixed platform that holds the material in place while the printhead moves across, depositing ink that is instantly cured by UV light. This technology enables precise, fast, and cost-effective printing on materials ranging from flexible fabrics to rigid metals.
Key Advantages for Corrugated Materials
Printing on corrugated materials, such as corrugated cardboard, poses unique challenges due to their uneven surfaces and varying thickness. However, UV flatbed printers excel in these applications due to several key advantages:
Versatility: UV flatbed printers can handle a wide range of corrugated materials, from thin flutes to thicker double-wall constructions. This versatility makes them suitable for various packaging and display applications.
Precision: The fixed printhead and precise positioning systems ensure that even the most intricate designs are reproduced accurately on corrugated surfaces. This is crucial for branding and marketing materials where image quality matters.
Durability: UV inks cure instantly upon exposure to UV light, creating a scratch-resistant and water-resistant finish. This durability is essential for corrugated materials that may be exposed to rough handling during transportation or storage.
Cost-effectiveness: Traditional printing methods for corrugated materials often require expensive dies or plates, increasing setup costs and lead times. UV flatbed printers, on the other hand, offer true digital printing capabilities, eliminating the need for these upfront costs and enabling short-run and variable data printing.
Printing Process on Corrugated Materials
The process of printing on corrugated materials using a UV flatbed printer involves several steps, each crucial to achieving high-quality results.
1. Material Preparation
Before printing, corrugated materials must be properly prepared. This includes:
Cutting: Corrugated sheets are cut to the desired size, ensuring that they fit perfectly on the printer’s platform.
Cleaning: Surfaces are cleaned to remove dust, dirt, or any other contaminants that could affect ink adhesion.
Flattening: In some cases, corrugated sheets may need to be slightly flattened to ensure even contact with the printhead. However, care must be taken not to crush the flutes.
2. Printing Setup
The UV flatbed printer is then set up for printing:
Ink Loading: The appropriate UV inks are loaded into the printer’s ink cartridges. UV inks come in various colors, including cyan, magenta, yellow, black, and sometimes white or varnish for added effects.
Printhead Alignment: The printheads are precisely aligned to ensure accurate placement of ink droplets.
Software Configuration: The printer’s software is configured with the desired print settings, including resolution, color mode, and print speed.
3. Printing
Once the printer is ready, the corrugated material is loaded onto the platform and secured in place. The printing process begins:
Ink Deposition: The printhead moves across the material, depositing UV ink in precise patterns.
UV Curing: As the ink is deposited, UV lights cure the ink instantly, turning it from a liquid into a solid film.
Repeat Passes: Depending on the desired print quality, the printer may make multiple passes over the material, depositing additional layers of ink and curing each layer as it goes.
4. Post-Processing
After printing, the corrugated material undergoes post-processing steps:
Drying: While UV curing ensures that the ink is mostly dry, some additional drying time may be required to ensure complete cure.
Cutting and Trimming: The printed sheet may need to be cut or trimmed to the final desired dimensions.
Inspection: A thorough inspection is conducted to ensure that the print quality meets the required standards.
Applications of UV Flatbed Printing on Corrugated Materials
UV flatbed printing on corrugated materials has numerous applications across various industries:
Packaging: High-quality printing on corrugated boxes enhances product presentation and branding. It allows for eye-catching designs that differentiate products on store shelves.
Point-of-Sale Displays: UV flatbed printers enable the creation of custom point-of-sale displays made from corrugated materials. These displays can feature vibrant graphics, making them more effective in attracting customers’ attention.
Signage: Corrugated materials are often used for temporary signage, such as event banners or construction site signs. UV flatbed printing allows for quick and cost-effective production of these signs with high-resolution graphics.
Prototypes and Mockups: Designers and manufacturers often use corrugated materials for prototypes and mockups due to their low cost and ease of modification. UV flatbed printing enables the creation of realistic prototypes with detailed graphics and text.
Conclusion
UV flatbed printers have transformed the way we print on corrugated materials, offering unprecedented versatility, precision, and cost-effectiveness. By leveraging the power of UV curing inkjet technology, these printers enable the production of high-quality graphics on a wide range of corrugated substrates. Whether for packaging, signage, or prototypes, UV flatbed printing on corrugated materials is a game-changer that continues to drive innovation and growth in the printing industry.