UV Flatbed Printer: Maintaining Optimal Humidity Levels for Printing
UV Flatbed Printer: Maintaining Optimal Humidity Levels for Printing
In the realm of digital printing, UV flatbed printers have revolutionized the way we approach printing on a variety of substrates, from rigid materials like glass and metal to flexible ones such as vinyl and fabric. These versatile machines utilize ultraviolet light to cure inks instantly, providing high-quality, durable prints that are resistant to fading and environmental factors. However, one often-overlooked aspect of operating a UV flatbed printer efficiently is the importance of maintaining optimal humidity levels within the printing environment. Humidity can significantly impact print quality, ink adhesion, and overall equipment performance. This article delves into the intricacies of humidity control in UV flatbed printing, exploring why it matters, how it affects the printing process, and practical strategies to ensure ideal conditions for consistent, high-quality output.
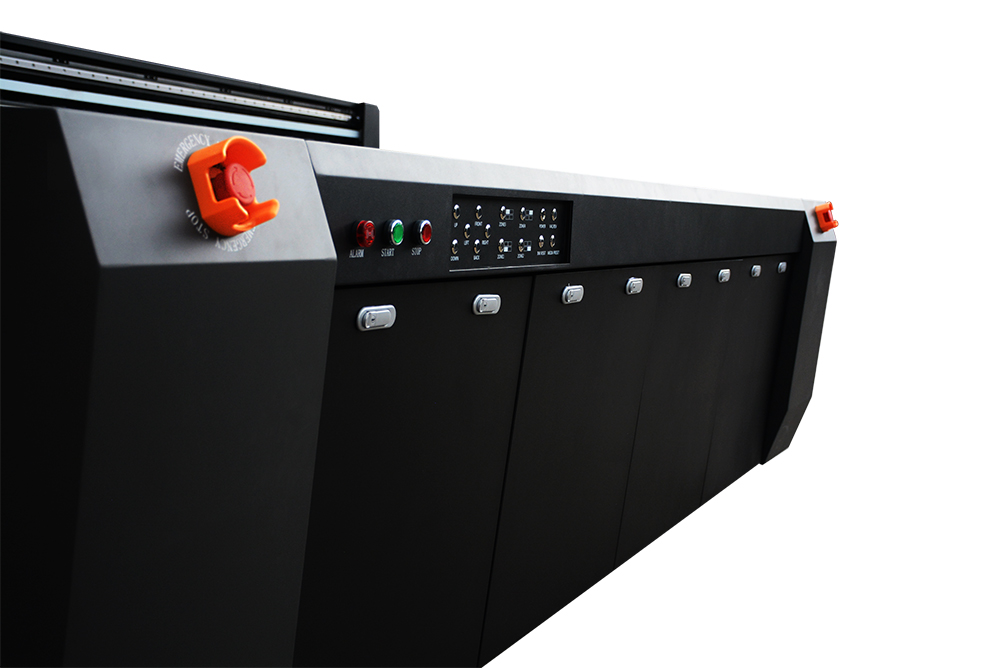
The Science Behind Humidity and Printing
Humidity refers to the amount of moisture present in the air, typically measured as relative humidity (RH), which is the ratio of the actual water vapor pressure to the saturation vapor pressure at a given temperature, expressed as a percentage. In the context of UV flatbed printing, humidity plays a crucial role in several aspects of the printing process, including ink viscosity, substrate moisture content, and the curing process itself.
Ink Viscosity and Flow
UV inks are designed to have a specific viscosity to ensure proper flow through the printer’s nozzles and even distribution on the substrate. High humidity can cause the ink to absorb moisture, leading to increased viscosity and potential clogging of nozzles. Conversely, low humidity can result in the ink evaporating too quickly, causing it to thicken and potentially leading to poor print quality, such as uneven color distribution or banding.
Substrate Moisture Content
The moisture content of the substrate can also be influenced by ambient humidity. For instance, wooden or paper-based materials can absorb or release moisture depending on the surrounding humidity, causing them to expand or contract. This dimensional change can lead to print distortions, such as warping or cracking of the ink film after curing. Similarly, metal substrates may develop condensation in high humidity, which can interfere with ink adhesion and result in a less durable print.
Curing Efficiency
The UV curing process relies on a chemical reaction between the ink and the ultraviolet light to solidify the ink instantly. Humidity can affect this reaction in two ways. Firstly, high humidity can create a barrier on the substrate’s surface, preventing the UV light from penetrating fully and thus slowing down or inhibiting the curing process. Secondly, excess moisture can cause the ink to remain in a tacky state, leading to smudging or adhesion issues. On the other hand, very low humidity can cause the ink to cure too quickly, potentially leading to shrinkage or cracking of the ink film.
The Ideal Humidity Range for UV Flatbed Printing
Given the above considerations, maintaining an optimal humidity level is vital for achieving consistent print quality and maximizing the lifespan of both the printer and the prints. Most UV flatbed printer manufacturers recommend an ideal humidity range of between 40% to 60% RH for optimal performance. Within this range, the ink viscosity remains stable, substrate moisture content is balanced, and the UV curing process occurs efficiently without compromising print quality.
Strategies for Humidity Control
Achieving and maintaining the ideal humidity level in a printing environment requires a combination of proactive measures and the use of specialized equipment. Here are some practical strategies to ensure optimal humidity levels for UV flatbed printing:
1. Humidity Monitoring
The first step in controlling humidity is to monitor it continuously. Invest in a high-quality hygrometer that provides accurate readings of both temperature and humidity. Place the hygrometer in the printing area to get real-time data and make adjustments as necessary.
2. Climate Control Systems
Install a climate control system, such as a humidifier or dehumidifier, to regulate the humidity levels in the printing environment. These systems can be set to maintain the desired humidity range automatically, ensuring a consistent printing environment regardless of external weather conditions.
Humidifiers: In dry climates or during winter months when indoor heating reduces humidity, a humidifier can add moisture to the air, bringing it up to the optimal range.
Dehumidifiers: In humid climates or during rainy seasons, a dehumidifier can remove excess moisture from the air, preventing it from interfering with the printing process.
3. Isolation and Sealing
To minimize the impact of external humidity fluctuations, isolate the printing area from the surrounding environment. Seal windows, doors, and any other gaps that could allow outside air to enter. This helps to create a controlled microclimate within the printing space.
4. Proper Ventilation
While sealing the printing area is important, ensuring adequate ventilation is also crucial. Good ventilation helps to remove any volatile organic compounds (VOCs) emitted by the UV inks during the curing process, which can contribute to both air quality and humidity control. Install an exhaust system that draws air from the printing area and replaces it with filtered, conditioned air.
5. Substrate Storage
Store substrates in a controlled environment with similar humidity levels to the printing area. This helps to ensure that the materials do not absorb or release moisture before printing, reducing the risk of print distortions. Use desiccant packets or humidity-controlled storage containers for sensitive materials.
6. Regular Maintenance
Perform regular maintenance on the printer and its components to ensure they are functioning correctly and not contributing to humidity-related issues. Clean the printer heads regularly to prevent clogging, and check for any leaks or malfunctions that could affect ink viscosity or curing efficiency.
7. Employee Training
Educate your staff on the importance of humidity control in the printing process and train them on how to monitor and adjust the humidity levels correctly. Encourage them to report any issues related to humidity fluctuations promptly so that corrective measures can be taken.
Maintaining optimal humidity levels in a UV flatbed printing environment is a critical yet often overlooked aspect of ensuring high-quality prints and prolonging the lifespan of both the equipment and the printed materials. By understanding the science behind humidity’s impact on ink viscosity, substrate moisture content, and the curing process, and implementing proactive strategies for humidity control, printers can achieve consistent, reliable results. Investing in the right equipment, such as climate control systems, hygrometers, and proper ventilation, combined with regular maintenance and employee training, will help to create a controlled environment where UV flatbed printers can operate at their full potential, delivering exceptional print quality every time.