UV Flatbed Printer: Maintaining Optimal Temperature Conditions for Printing
In the realm of digital printing, UV flatbed printers have emerged as a versatile and powerful tool, capable of producing high-quality prints on a wide range of substrates. These printers utilize ultraviolet (UV) light to cure inks instantly, offering numerous advantages such as faster printing speeds, enhanced durability, and the ability to print on diverse materials like wood, metal, glass, and plastics. However, to achieve optimal print quality and ensure the longevity of both the printer and its output, maintaining the right temperature conditions during the printing process is paramount. This article delves into the intricacies of temperature management in UV flatbed printing, exploring why it matters, how to monitor and control temperatures, and the steps to troubleshoot common temperature-related issues.
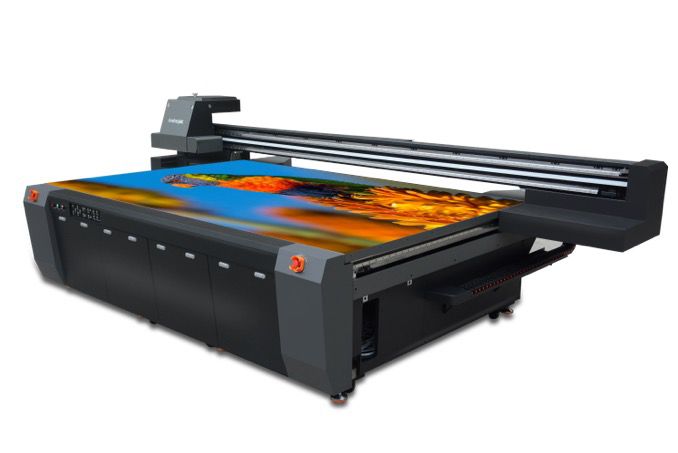
The Importance of Temperature Control in UV Flatbed Printing
Temperature plays a critical role in the performance of UV inks and the overall printing process. Here are several key reasons why maintaining optimal temperature conditions is essential:
Ink Viscosity and Flow: UV inks have a specific viscosity that is optimal for printing. Too high or too low temperatures can alter this viscosity, affecting ink flow and causing issues like clogging, poor adhesion, or uneven print quality.
Curing Efficiency: UV inks require a precise amount of UV energy to cure properly. Temperature fluctuations can impact the curing process, leading to undercured inks that remain tacky or overcured inks that become brittle and prone to cracking.
Substrate Stability: Different substrates react differently to temperature changes. For instance, some materials may expand or contract, causing distortion in the final print. Maintaining a stable temperature helps ensure the substrate remains dimensionally stable throughout the printing process.
Printer Performance: The mechanical components of a UV flatbed printer, including the printheads and motors, operate most efficiently within a specific temperature range. Excessive heat can cause premature wear and tear, while cold temperatures can lead to sluggish performance and potential printhead clogging.
Operator Safety: Safe operating temperatures are crucial for the well-being of printer operators. Excessive heat can create an uncomfortable working environment and pose health risks, while too low temperatures can make the workspace uncomfortably cold and potentially affect the handling of certain materials.
Monitoring and Controlling Temperature in UV Flatbed Printing
To maintain optimal temperature conditions, a comprehensive approach involving both monitoring and control measures is necessary. Here’s how to effectively manage temperature in a UV flatbed printing environment:
Temperature Sensors: Install temperature sensors at strategic locations within the printing area, including near the printheads, ink supply, and substrate. These sensors should provide real-time data, allowing for immediate adjustments if temperatures deviate from the desired range.
Climate Control Systems: Utilize heating, ventilation, and air conditioning (HVAC) systems to regulate the ambient temperature in the printing room. Aim for a consistent temperature that falls within the recommended range for your specific printer model and ink type, typically between 20°C to 25°C (68°F to 77°F).
Insulation: Proper insulation of the printing room can help maintain a stable temperature, reducing the impact of external weather conditions. This includes sealing windows, doors, and any gaps that could let in cold or hot air.
Ink Temperature Regulation: Some UV printers are equipped with ink temperature control systems that maintain the ink at a constant temperature. If your printer does not have this feature, consider using ink heaters or coolers to keep the ink within the optimal range.
Substrate Preconditioning: Before printing, ensure that the substrate is at the same temperature as the printing environment. This can be achieved by storing substrates in the printing room for a sufficient period or using substrate heaters/coolers.
Regular Maintenance: Perform regular maintenance on the printer, including cleaning the printheads and checking for any obstructions or malfunctions that could affect temperature regulation. A well-maintained printer is more likely to operate efficiently and within the desired temperature range.
Troubleshooting Temperature-Related Issues
Despite the best efforts to control temperature, issues can still arise. Here are some common temperature-related problems in UV flatbed printing and how to address them:
Ink Clogging: If the ink is too cold, it may thicken and clog the printheads. To resolve this, increase the ambient temperature or use ink heaters to warm the ink to the recommended temperature. Conversely, if the ink is too hot, it may become too thin, leading to poor print quality. In this case, reduce the temperature or use ink coolers.
Curing Issues: Undercured inks often indicate that the UV lamps are not providing enough energy due to low temperatures. Check the lamp intensity and ensure that the lamps are at the correct distance from the substrate. Overcured inks, on the other hand, can result from excessive heat. Adjust the lamp power or increase the distance between the lamps and the substrate.
Substrate Distortion: If the substrate is warping or distorting, it may be due to temperature fluctuations. Ensure that the substrate is properly preconditioned to the printing room temperature and consider using a vacuum table or other clamping mechanisms to keep it flat during printing.
Printer Overheating: If the printer is overheating, it could be due to a malfunctioning cooling system or excessive ambient temperature. Check the printer’s cooling fans and vents for any obstructions, and ensure that the HVAC system is functioning correctly. If necessary, reduce the workload or take breaks to allow the printer to cool down.
Operator Comfort: If operators are complaining about the temperature, it may affect their performance and safety. Regularly monitor the workspace temperature and adjust the HVAC system to maintain a comfortable environment. Provide appropriate clothing or personal protective equipment (PPE) to help operators manage temperature extremes.
Maintaining optimal temperature conditions in UV flatbed printing is a multifaceted challenge that requires attention to detail, proactive monitoring, and effective control measures. By understanding the importance of temperature control, implementing the right monitoring and regulation strategies, and being prepared to troubleshoot common issues, printer operators can ensure consistent print quality, prolong the lifespan of their equipment, and create a safe and comfortable working environment. Remember, the key to successful UV flatbed printing lies not just in the technology itself but also in the careful management of the printing environment, with temperature being a critical factor. With the right approach, you can unlock the full potential of your UV flatbed printer, delivering outstanding prints every time.