UV Flatbed Printer: Optimizing Performance and Productivity
UV Flatbed Printer: Optimizing Performance and Productivity
In the realm of digital printing, the UV flatbed printer has emerged as a game-changer, revolutionizing the way businesses approach high-quality, large-format printing. This versatile technology allows for the precise deposition of ink onto a wide range of substrates, from rigid materials like glass, metal, and wood to flexible media such as vinyl and textiles. By harnessing the power of ultraviolet (UV) light to cure the ink instantly, UV flatbed printers deliver exceptional durability, vibrant colors, and sharp details. To fully leverage the potential of these advanced machines, it is crucial to understand the key factors that influence their performance and productivity, as well as the strategies for optimizing these aspects.
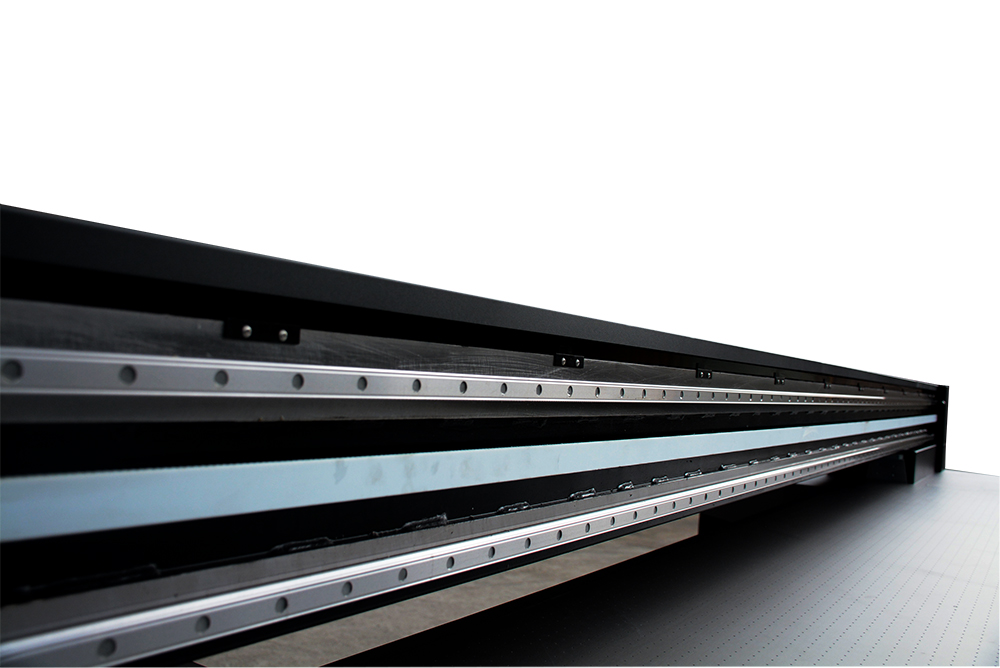
Understanding the Basics of UV Flatbed Printers
UV flatbed printers utilize a process called UV-curing, where ink is exposed to UV light immediately after being deposited onto the substrate. This rapid curing eliminates the need for drying time, enabling faster production speeds and reducing the risk of smudging or bleeding. The ink used in UV flatbed printers is specially formulated to be responsive to UV light, ensuring a robust bond with the material and exceptional resistance to fading, scratching, and chemicals.
These printers typically feature a flat, stationary bed onto which the substrate is placed. The print head, equipped with an array of UV-LEDs or lamps, moves over the surface, depositing ink in a controlled manner according to the digital design. The combination of precise ink placement and instant curing results in prints that are not only visually stunning but also highly durable.
Key Factors Affecting Performance and Productivity
1. Ink Quality and Management
The quality of the ink used in a UV flatbed printer plays a pivotal role in determining the final output. High-quality inks offer better color saturation, improved adhesion, and greater resistance to environmental factors. It is essential to use inks specifically designed for UV-curing to ensure optimal performance.
Ink management is another critical aspect. Regularly cleaning and maintaining the ink system, including print heads and ink lines, prevents clogs and ensures consistent ink flow. Additionally, monitoring ink levels and replacing cartridges or reservoirs when necessary avoids downtime due to ink depletion.
2. Substrate Compatibility and Preparation
UV flatbed printers can accommodate a diverse array of substrates, but not all materials are created equal. The choice of substrate significantly impacts the print quality, adhesion, and overall durability of the output. For instance, porous materials like wood may require a primer to ensure proper ink adhesion, while smooth surfaces like glass might need a special coating to enhance ink reception.
Proper substrate preparation is vital. This includes cleaning the surface to remove dust, oils, and contaminants that could interfere with ink adhesion. In some cases, pretreating the material with a primer or adhesive promoter may be necessary to optimize print quality.
3. Print Resolution and Speed
The resolution of a UV flatbed printer, measured in dots per inch (DPI), directly affects the clarity and detail of the print. Higher resolutions yield sharper images and smoother transitions between colors. However, increasing resolution often comes at the cost of print speed.
Finding the right balance between resolution and speed is crucial for optimizing productivity. For applications where speed is paramount, such as large-scale advertising graphics, a slightly lower resolution may be acceptable to maximize throughput. Conversely, for high-end art reproductions or fine detail work, a higher resolution is essential.
4. UV Curing System
The effectiveness of the UV curing system is integral to the printer’s performance. A well-designed UV system ensures thorough and uniform curing of the ink, leading to durable prints that resist fading and wear. Factors such as the intensity and uniformity of the UV light, as well as the curing time, must be carefully calibrated to match the ink and substrate being used.
5. Software and Workflow Optimization
The software driving the UV flatbed printer is the brain of the operation. Efficient workflow management, including file preparation, color management, and job queuing, can significantly enhance productivity. Look for printers that offer intuitive, user-friendly software interfaces and robust color management tools to streamline the printing process.
Automated features, such as nesting (arranging multiple designs on a single sheet to minimize waste) and job scheduling, can further improve efficiency by reducing manual intervention and minimizing downtime.
Strategies for Optimizing Performance and Productivity
1. Regular Maintenance and Calibration
Like any complex machinery, UV flatbed printers require regular maintenance to perform at their best. Establish a routine for cleaning print heads, checking ink lines, and inspecting the UV curing system. Regular calibration of the printer ensures accurate color reproduction and consistent print quality.
2. Ink and Substrate Testing
Before committing to a large-scale production run, conduct thorough testing with the chosen ink and substrate combination. This allows you to identify any potential issues with adhesion, color accuracy, or durability and make adjustments accordingly.
3. Workflow Automation
Automate as many aspects of the printing process as possible. Utilize software features that allow for batch processing, automatic nesting, and job scheduling. This not only saves time but also reduces the risk of errors associated with manual intervention.
4. Operator Training
Well-trained operators are essential for maximizing the performance and productivity of a UV flatbed printer. Provide comprehensive training on printer operation, ink management, software usage, and troubleshooting. Encourage ongoing education to keep operators up-to-date with new features and best practices.
5. Continuous Improvement
Regularly review your printing processes and look for opportunities to improve. This might involve upgrading software, investing in new tools or accessories, or adopting new workflow strategies. Stay informed about advancements in UV printing technology and be prepared to adapt as needed.
6. Quality Control
Implement a robust quality control system to ensure consistent print quality. This includes regular inspections of prints for defects, color accuracy, and adhesion. Use standardized test protocols and maintain detailed records to track performance over time.
Conclusion
The UV flatbed printer offers unparalleled versatility and capability in the realm of large-format digital printing. By understanding the key factors that influence its performance and productivity, and implementing strategies to optimize these aspects, businesses can harness the full potential of this powerful technology. From ink management and substrate preparation to workflow automation and continuous improvement, a comprehensive approach to UV flatbed printer optimization ensures high-quality output, increased efficiency, and a competitive edge in the market. With the right tools, training, and mindset, businesses can elevate their printing capabilities and drive growth in today’s fast-paced digital landscape.