UV Flatbed Printer: Settings for Optimal Print Quality
In the realm of digital printing, UV flatbed printers have revolutionized the way we approach printing on a variety of substrates. These versatile machines utilize ultraviolet light to cure inks instantly, resulting in vibrant, durable, and high-resolution prints. However, achieving optimal print quality is not solely dependent on the printer’s capabilities; it also hinges on a myriad of settings that must be finely tuned to match the specific requirements of each print job. This article delves into the essential settings that can help you maximize the print quality of your UV flatbed printer, ensuring stunning outcomes every time.
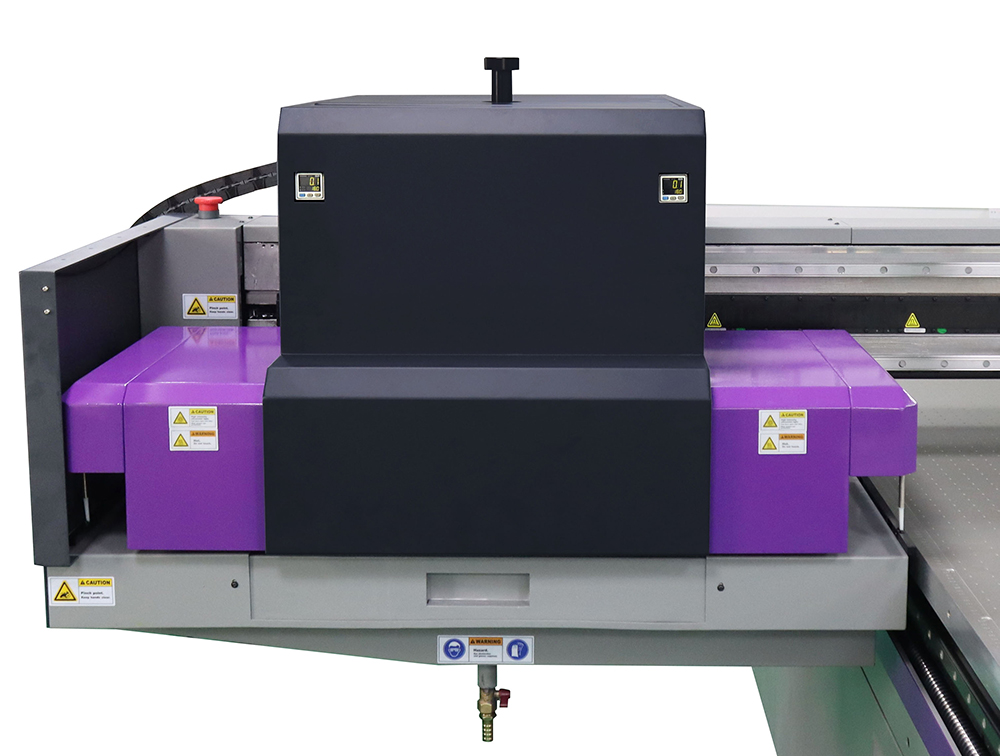
Understanding the Basics
Before diving into the intricacies of printer settings, it’s crucial to have a grasp of the fundamental aspects that influence print quality. These include:
Ink Type and Quality: UV-curable inks are designed to adhere to a wide range of materials and cure rapidly under UV light. The quality and type of ink can significantly impact color accuracy, durability, and overall print appearance.
Printer Resolution: The resolution of a UV flatbed printer determines the fineness of detail it can reproduce. Higher resolutions generally yield sharper images.
Substrate Compatibility: Different materials absorb ink differently, affecting color saturation, adhesion, and curing time. Understanding the characteristics of your substrate is vital.
Curing System: The efficiency of the UV curing system plays a pivotal role in ink adhesion and durability. Proper curing ensures that the ink is fully set and resistant to fading or smudging.
Key Settings for Optimal Print Quality
1. Print Resolution
Setting the right print resolution is foundational to achieving high-quality prints. Most UV flatbed printers offer multiple resolution options, commonly ranging from 300 dpi (dots per inch) to 1440 dpi or higher. While higher resolutions yield finer details, they also increase print time and ink consumption.
Recommendation: For most applications, a resolution of 600-1200 dpi strikes a balance between detail and efficiency. For critical applications requiring intricate details, such as fine art reproductions or high-end packaging, opt for the highest resolution available.
2. Ink Drop Size
The size of the ink droplets dispensed by the printer heads directly affects print quality. Smaller droplets result in smoother gradients and finer details.
Recommendation: Adjust the ink drop size based on the complexity of the image and the desired finish. For photographic images or fine text, smaller droplet sizes are preferable. Conversely, for solid areas or less detailed graphics, larger droplets can be used to improve printing speed without compromising quality.
3. Color Management
Accurate color reproduction is critical in any printing process. UV flatbed printers typically utilize ICC (International Color Consortium) profiles to manage color.
Recommendation: Create or select an ICC profile that matches your specific printer, ink set, and substrate combination. Regularly calibrate your printer and monitor color consistency using color test charts.
4. Print Speed vs. Quality
Print speed and quality are often inversely related. Faster print speeds may result in lower quality due to ink not being laid down as precisely.
Recommendation: For best quality, especially in detailed or critical prints, prioritize quality over speed. Adjust the printer’s speed settings to a slower pace to allow for better ink placement and curing.
5. Curing Settings
The UV curing process is critical to the final print quality. Over-curing can lead to ink cracking or substrate damage, while under-curing results in poor ink adhesion.
Recommendation: Follow the manufacturer’s guidelines for curing times and intensities based on the ink type and substrate. Use test prints to fine-tune these settings, ensuring complete curing without causing damage.
6. Pass Count
The number of times the print head passes over the substrate (pass count) can affect both the color saturation and the overall appearance of the print.
Recommendation: For solid colors or thick layers For, multiple passes may be necessary to achieve full saturation. lighter or more detailed areas, fewer passes can help maintain fine details.
7. Media Handling
Proper media handling ensures that the substrate remains stable during printing, preventing misalignment and ink bleeding.
Recommendation: Use the printer’s media clamps, vacuum systems, or other stabilizing mechanisms to keep the substrate secure. Ensure the substrate is clean and free of dust or debris that could interfere with ink adhesion.
8. Maintenance and Cleanliness
Regular printer maintenance is essential for consistent print quality. Clogged nozzles, dirty print heads, or accumulated dust can all degrade print quality.
Recommendation: Perform regular cleaning cycles as recommended by the printer manufacturer. Keep the printer environment clean and dust-free. Inspect and replace worn parts, such as wiper blades or ink filters, as needed.
Advanced Techniques for Fine-Tuning
A. Halftoning and Dithering
Halftoning is a technique used to simulate continuous tones using dots of varying sizes and spacing. Dithering, on the other hand, blends colors by alternating between different pixels.
Recommendation: Experiment with different halftoning and dithering patterns to find the one that best suits your specific print job. These settings can help improve the appearance of gradients and solid colors.
B. White Ink Underlay
For transparent or light-colored substrates, using a white ink underlay can enhance color vibrancy and opacity.
Recommendation: Apply a layer of white ink before printing the color image. This step can significantly improve color saturation and overall print quality, particularly on materials like glass or clear plastics.
C. Varnish or Spot UV
Adding a varnish or spot UV finish can enhance the visual appeal and durability of the print.
Recommendation: Use varnish or spot UV selectively to highlight certain areas of the print, such as logos or text. This not only adds a professional touch but also increases the print’s resistance to wear and tear.
Achieving optimal print quality with a UV flatbed printer is a combination of understanding your printer’s capabilities, selecting the right settings, and utilizing advanced techniques to enhance the final output. By carefully adjusting parameters such as print resolution, ink drop size, color management, and curing settings, you can ensure that each print job meets or exceeds expectations. Regular maintenance and a keen eye for detail are the cornerstones of consistent, high-quality printing. With these guidelines in mind, you’ll be well-equipped to produce stunning prints that showcase the full potential of your UV flatbed printer.